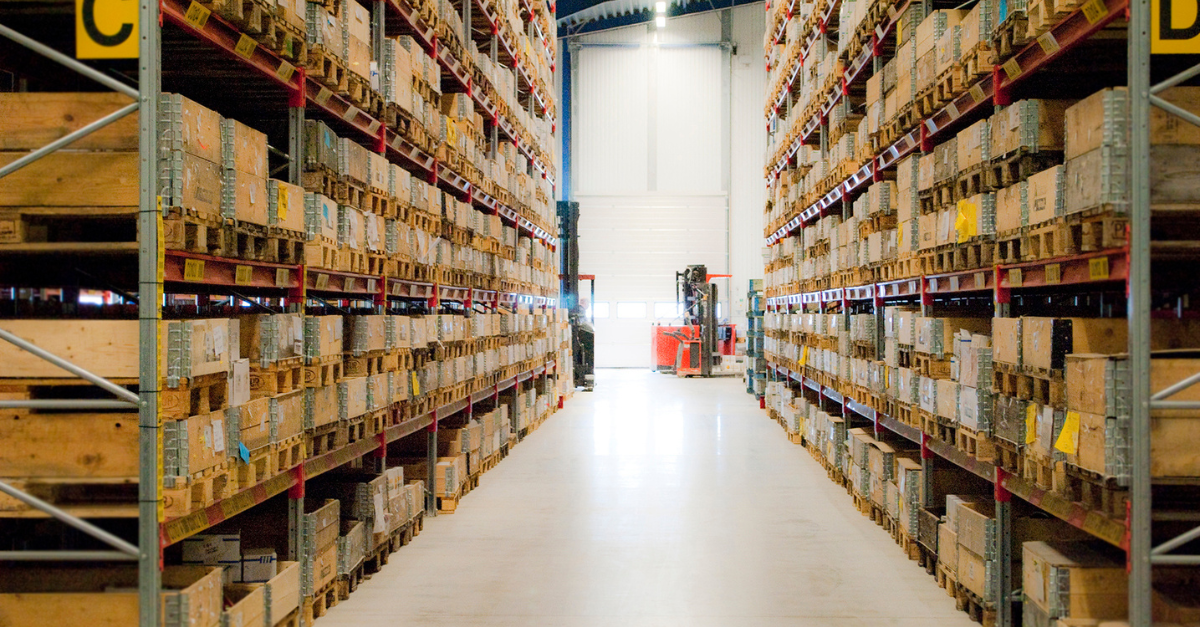
The increasing market competition and the service focus of customers move main attention of the logistics and manufactures to their service providers. Companies improve their distribution functionality through tactical planning of supply chain, production, transportation, delivery and much beyond. Within this process facilities require automatization which depend on digital and mobile network solutions.
Optimalization of facility locations with digital solutions is important decision in strategic planning phase. Many facilities decided long time ago for mobile integration in operations as this approach was expected from the side of their customers. High expectations of the customers is always related to maintaining simultaneously high quality of the services but making that effort in the facility is always profitable in many ways.
Strategic focus in warehousing
We introduced optimalization in logistics and manufactures as challenge of continuous improvement. In highly dynamic environment development goal is the optimization of the time consuming tasks and most affordable processes within its operations. Solutions can be delivered through analyses that help determine unproductivity in operational areas. Particular analyses of operational areas in distribution and manufacture point out as mentioned below:
- Inbound – unloading deliveries of raw materials or products from supplier
- Operations:
- Receiving – control and manual or system registration of commodities
- Putaway – moving goods from the dock area to the stock locations on shelfs or racks
- Order Picking and packing – collecting orders and production preparing
- Inventory control – shop stock control and cycle counting
- Outbound – preparing consignments, load scheduling and customer delivery and shipping goods
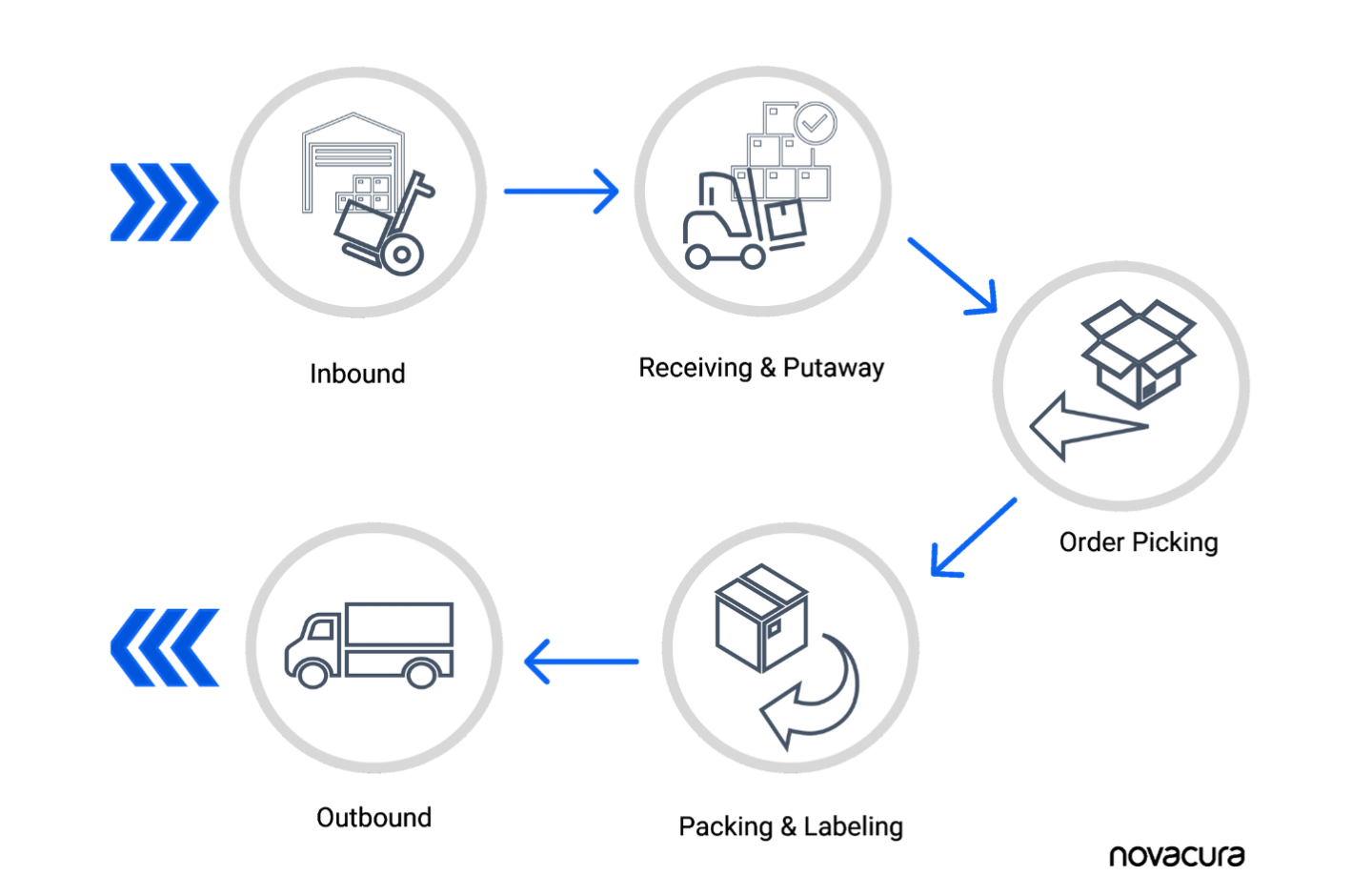
Logistics and anufacture remain above as a key areas inextricably linked. A responsible strategic planning phase will not allow any of these areas to fall apart.
Top 10 most common warehousing mistakes
Dysfunctionality in described above key areas can cause tremendous implications in entire distribution and manufacture processes. We can briefly define group of characteristic problems that have potentially highly negative impact:
- Unloading the wrong pallets with the wrong quantities as a result of incorrect invoice checks;
- Sorting out the wrong units during receiving and getting mixed up with the wrong invoices or RMAs as a result of unclear documentation;
- Putaway in the wrong places on racks and shelves as a result of miscommunication and unclear inventory structure;
- Completing wrong orders as of result of mixed picklists;
- Incomplete orders from results overlooked products and locations during order picking;
- Incorrect units on the locations, resulting in the inability to perform day-to-day inventory control without mobility;
- Delays with shipping due to lack of picking path optimalization and lack of the replenishment;
- Shipment delays due to the lack of an adequate system for continuous replenishment at available locations;
- Shipping of products at risk of damage due to the use of inappropriate materials and packaging methods for shipment;
- Shipping to the wrong destination due to lack of organization and poor labeling system;
These 10 problems became classic challenges in logistics and manufacturing. The correlation between introduced incidents is related to ineffective procedures and the weakness of an internal systems. The large number of possible blockages in key areas of operations makes it difficult to create procedures for all incidents. Therefore, lean techniques are required to ensure comprehensive information exchange. Knowing the root causes is a milestone on the way to implementing good corrective actions.
Warehousing optimalization
The common characteristics of the logistics and manufacture maintenance show that there is the need to develop specific control systems.
We’re perceive a simultaneous optimization of neighbouring key areas as better exploit the entire potential of internal operations. Extending strategy model with focus on several operations areas at once, can fetch promising results in entire warehouse. We can provide plan to integrate services to solve more -or less- complex and complicated problems. Considering internally-focused performance small and large instances can be solved with software solution and mobility.
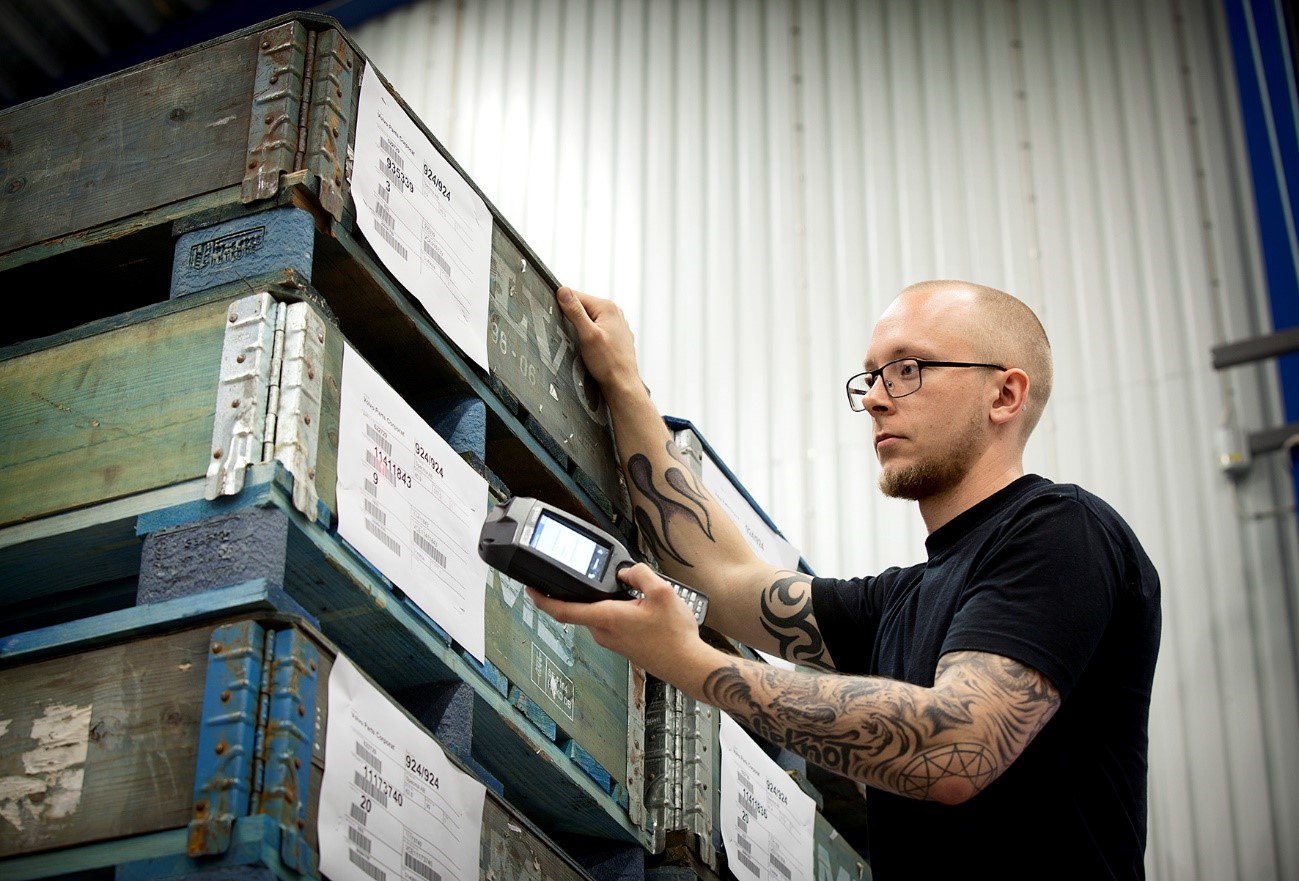
An example of handling units in a warehouse using a handheld scanner (moving parts into place in boxes). Operations can be carried out with generally available barcode scanners and mobile terminals such as: Motorola, Zebra, etc.
For solution purpose, we used real data of the one of our customer.
We collaborate with company that headquarters are located in Western Europe. They hire over +3K people and produce customized drive systems and electric components. Their products are manufactured in several places in the world and distributed for healthcare and aerospace industries. They need to meet high customers demand regarding quality of their products and services.
This company use originally IFS ERP system for inventory management. Couple of years ago they decided to improve their operational key areas to cover the whole internal logistics transport and became also the user of our product Novacura Flow. This is digital software solution for warehouse mobility to help prevent top 10 common warehousing mistakes.
Novacura Flow solution for warehouse management
The following is MATERIAL TRANFER application. The name of the application can be freely chosen and the application can be configured according to individual operational needs.
- Two pallets on which 800 units of goods have been delivered have been received into the warehouse. The goods are moved to a specific location by an operator using a barcode scanner.
- Default locations can be identified by a handheld barcode scanner when the application is enabled. The operator started the application and went to the specified location to warehouse the goods.
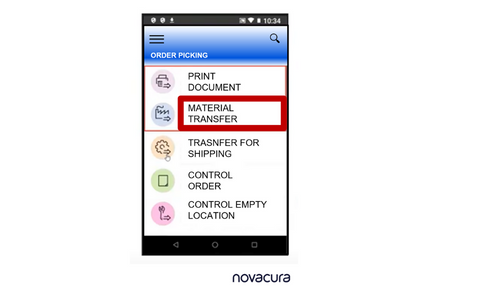
Snapshot from applications menu displayed on mobile device.
3. The operator scans the barcode on the box, enters the amount of goods in the application that can be deposited at the location.
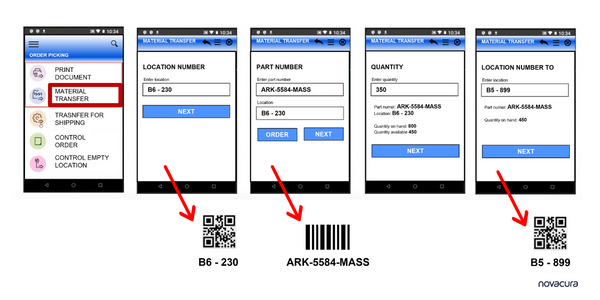
The application has the ability to scan QR codes and barcodes
- The operator scans the direct location on another shelf, which means that 350 units will now be stored at location B6-230.
- The operator moves to the next location to store the 450 units that are still not stored will be moved to location B5-899.
- The data in the ERP system has been updated with the value entered in the application.
The presented application is adapted to the company’s internal needs, and functions can be flexibly modified or expanded. Modifications include the addition of any functions at any stage of the required operational activities and a full language package for many countries.
Meet benefits with Novacura FLOW
The main reasons for optimization is increase productivity through reduction of these unproductive occurrences. Increase functional performance by facilitating mobile applications in your warehouse. Novacura Flow applications increase service levels that might be the extension of existing systems. In addition to these, there are several other strong benefits for you operations:
- Reducing bottlenecks – good scheduled sequence of unloading deliveries from the trailers.
- Reduce orders lead times – speeding up order picking with clear process
- Determine inventory traceability – reduced inventory loss, eliminating dead-stock, surplus and obsolete inventory with improved system transaction controls and better tracing of the inventory movement.
- Beter space management – more effective use of docking facilities, racks and shelfs etc.
- Dropping manual errors – reducing or preventing most common errors caused by manual actions
- Structured distribution system – well organized warehouse with good standards software
- Costs savings – reduced storage and material handling costs and increasing warehouse operations by keeping costs low
- Enhance customer relationship – defeat gaps in customer confidence regarding insufficient inventory management practices;
Summary
In determining requirements of your warehouse is important to understand inventory. You can manage any type of products, but they must all comply with the associated regulations. Complexes processes automated with software mobile devices is the recent answer for overriding issue for warehousing and costs management. This is the major trend in the business growth all over the world.
Novacura Flow provide this solution with almost 20 years of experience in the many industrial areas and warehousing. We offer comprehensive solution for entire inventory management but we support idea of Start Small Grow Big. Many of our customers started with pilot to spare time learning how to build apps. Good suggestion is start with small tests apps that will make changes step by step in your internal processes. People can start using the new system to find out how does this work before they asked about another extensions. Our customers are satisfied and happy with the new solution right away.
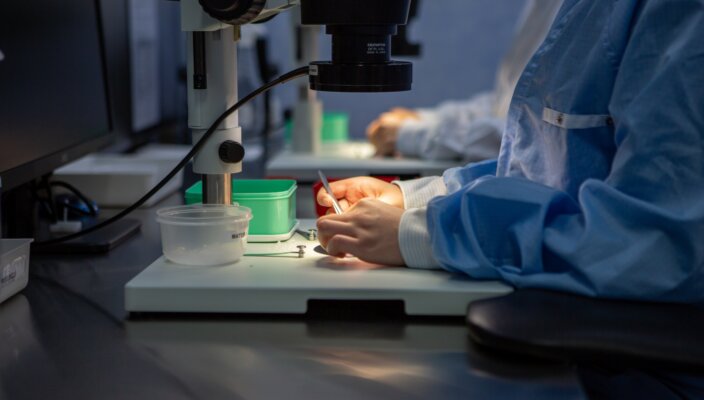
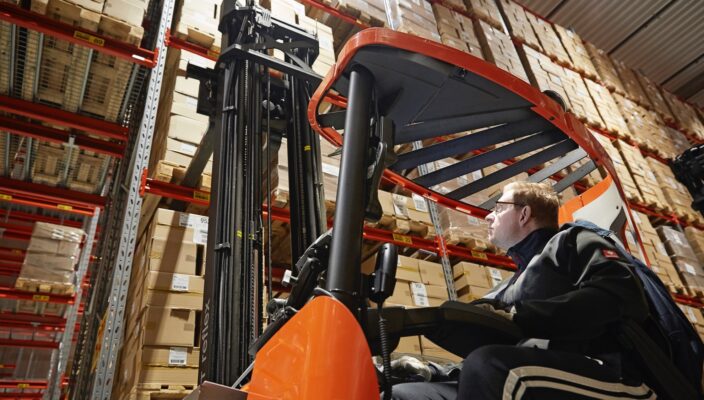
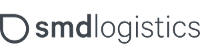
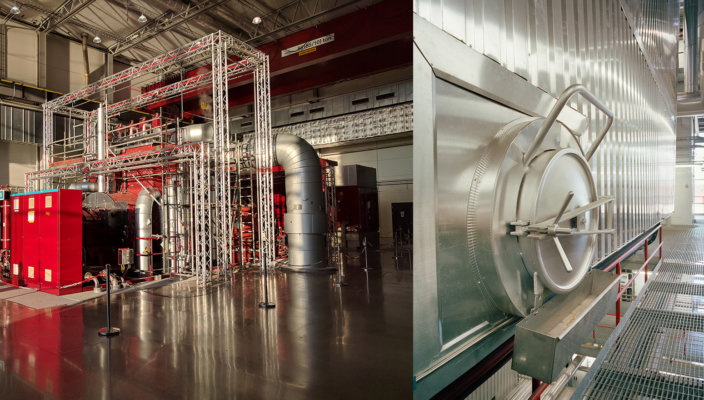
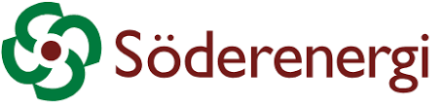
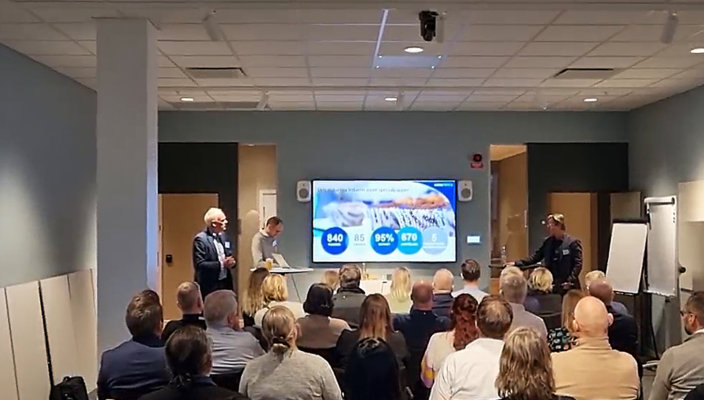
