It feels like every month, there’s a new story about a company dealing with major ERP failure and implementation problems. The latest edition comes from candy maker Haribo, who had troubles getting their famous gummy bears out to suppliers in late 2018 because of problems stemming from their latest ERP integration.
Haribo expected to have a few issues during implementation. But, by their own admission, the supply chain issues they faced after deployment were much larger than anticipated.
For Haribo, the problems eventually sorted themselves out. But other companies haven’t been so fortunate. Let’s take a look at a few other examples of failed ERP implementations and the key causes of their failure:
Woolworths Australia, 2015
After 6 years of planning, Woolworths Australia (or “Woolies”) went live with their new ERP in 2015. They had problems almost immediately, the biggest of which was empty shelves in many stores. What caused the problem? A glitch in the new system prevented Woolworths from placing orders with their suppliers. Suppliers were frustrated and furious… and Woolworths lost millions of dollars in sales.
But that wasn’t the only problem with the new ERP system.
From the Australian Financial Review (AFR):
One of the key problems and failings that occurred at Woolies during the SAP implementation process was the lack of attention given to documenting processes used by staff in the day-to-day running of the business.
Too much of the intellectual property of what was then the best-performing supermarket group in Australia was left in the heads of people who worked at Woolies.
This carried lots of risks because when people left they took with them key pieces of information.
Loss of corporate memory is often referred to as a key risk in companies but it is only when something as critical as a new merchandising system is jeopardised that senior management learn its importance.
What can we learn from this?
- Companies need to map all their business processes prior to ERP implementation. This practical information is essential when designing the new ERP system.
- Every company should have a plan for employee knowledge transfer so that information doesn’t disappear when an employee leaves the company.
- Above all: test everything before you go live with a new ERP system.
Oriola Finland, 2017
Almost every ERP implementation will have a few hiccups when the new system goes live. But what do you do when a small hiccup in the supply chain can mean the difference between life and death? This was the problem Oriola Finland was facing in September 2017, when they launched their new ERP.
Oriola is one of Finland’s largest pharmaceutical suppliers. They deliver thousands of medications to pharmacists around the country, including insulin, cancer medications and anti-psychotics. Any disruption to the supply chain doesn’t just cause lost sales: it can cause great damage to people’s health.
It sounds like Oriola didn’t anticipate any supply chain disruption as they switched over to their new ERP. But in reality, their ordering system was shut down for days. This led to widespread confusion and frustration as pharmacists all over Finland struggled to source live-saving medications. Compounding the frustration, Oriola chose to stay “mum” on the problems, only releasing a statement saying they were focusing all their attention on fixing the issues with the ordering system.
In the end, Oriola managed to sort out the issues with their new ERP. They also hired extra staff to process the backlog of orders. But the damage still cost the company millions of Euros and caused damage to their reputation.
What can we learn from this?
- When going live with a new ERP, always plan for the worst-case scenario.
- Change management is the key to successful ERP implementations. And change management isn’t limited to inside your company: you need to have a change management plan for your vendors, suppliers and customers as well.
- Conflict is, in effect, a breakdown in communication. More open communication with customers may have helped ease some of the frustrations Oriola’s customers were feeling.
Select Comfort, 2015
Mattress company Select Comfort went live with their new ERP in October 2015. A few weeks later, the CEO reported that things were going well, and the ERP implementation had caused minimal disruptions to the supply chain.
But if that was truly the case, we wouldn’t be talking about it.
Here’s what actually happened, according to the website UpperEdge:
Same store sales fell 30 percent, customers experienced delivery delays, and the company experienced higher-than-normal return rates and order cancellations. Company sales were off by $83 million dollars in sales. Earnings were $21 million lower than expected. The struggles with the ERP system implementation were identified as contributing to 43 cents a share in lost profitability. While the worst appears to be over, the company is expecting to take a hit of $40 to $50 million dollars more in lost sales in the 1st quarter of 2016. With the earnings release the company stock price fell 25 percent, destroying $250 million dollars in shareholder value.
So, what went wrong? Insiders say Select Comfort was being pressured by investors to either go live with the new system or cancel the project altogether, as the implementation process was taking too long and costing too much money. There were only 2 options for launching the new system: October 2015 and April 2016. Adding an extra 6 months to the project timeline wasn’t an option. So, they launched in October 2015, even though they weren’t quite ready.
What can we learn from this?
- Every ERP implementation project needs a strong corporate sponsor. If the Select Comfort project had had a strong corporate sponsor relaying messages to investors and explaining the importance of the project, perhaps the implementation team wouldn’t have been pressured into deploying the new system before it was ready. The corporate sponsor could also have allocated more time/resources to the implementation team.
- Stick to a proven project management framework, ideally one that allocates plenty of time for both planning and testing.
- Every ERP implementation needs an expert Project Manager to steer the ship. And that Project Manager needs the authority to make certain decisions on behalf of the project, such as extending the timeline.
Why do some ERP system implementations succeed while others fail?
ERP implementations are large and complex, which means there’s plenty of room for error. It might seem easy on the surface, but looks can be deceiving.
Want to learn more about ERP failures – and what you can do to make sure your next ERP implementation is successful? Download a free copy of our new guide, Why ERP Implementations Fail.
Why ERP implementations fail?
- Set the ERP implementation team
- Create an effective change management plan
- Communicate with diverse groups
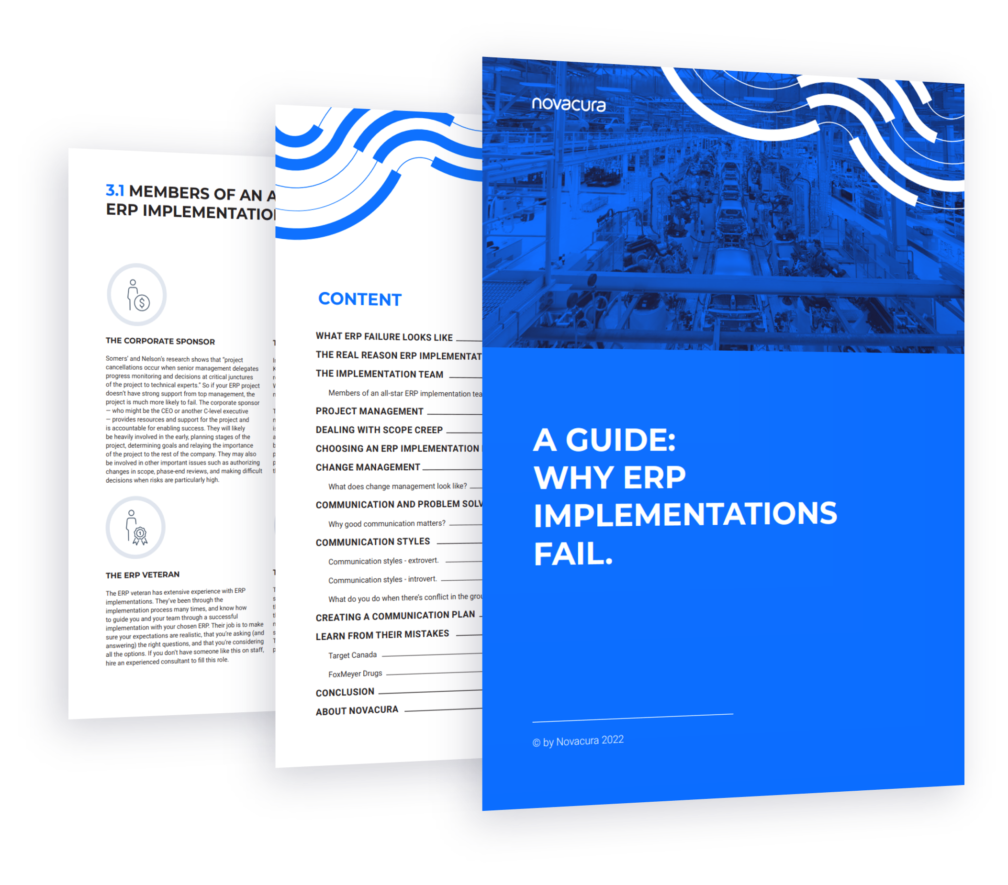
Best Practices for Preventing ERP Failures
To minimize the risk of ERP system failures, companies should adopt a set of best practices that can guide them through the implementation process. First, phased rollouts, where the new system is gradually introduced, help identify and address issues in smaller, manageable stages rather than risking a full-scale “big bang” launch. Comprehensive employee training is equally critical—ensuring all users are familiar with the system reduces errors and enhances adoption. Additionally, creating detailed contingency plans for every stage of implementation, including worst-case scenarios, ensures that companies can respond quickly and effectively to unexpected challenges. Coupling these steps with robust testing protocols allows businesses to catch and resolve issues before going live.
The Role of Technology Partners in ERP Success
A successful ERP implementation also hinges on choosing the right technology partner. Companies should seek partners who not only offer technical expertise but also understand their industry and unique business needs. A reliable partner will provide tailored solutions, assist with process mapping, and ensure seamless integration with existing systems. Equally important is their role in offering ongoing support post-deployment to handle system tweaks or issues. To aid in partner selection, businesses should prioritize factors such as proven experience, customer testimonials, and their ability to align with the company’s long-term goals. Collaborating closely with the technology partner ensures that the ERP system not only functions as intended but becomes a valuable tool for driving efficiency and growth.
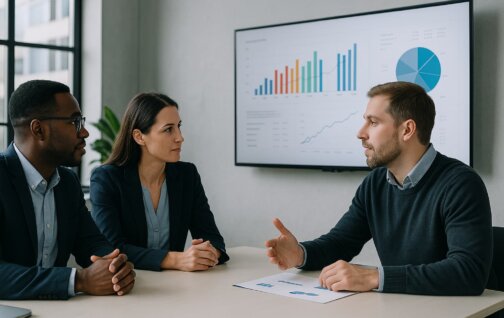
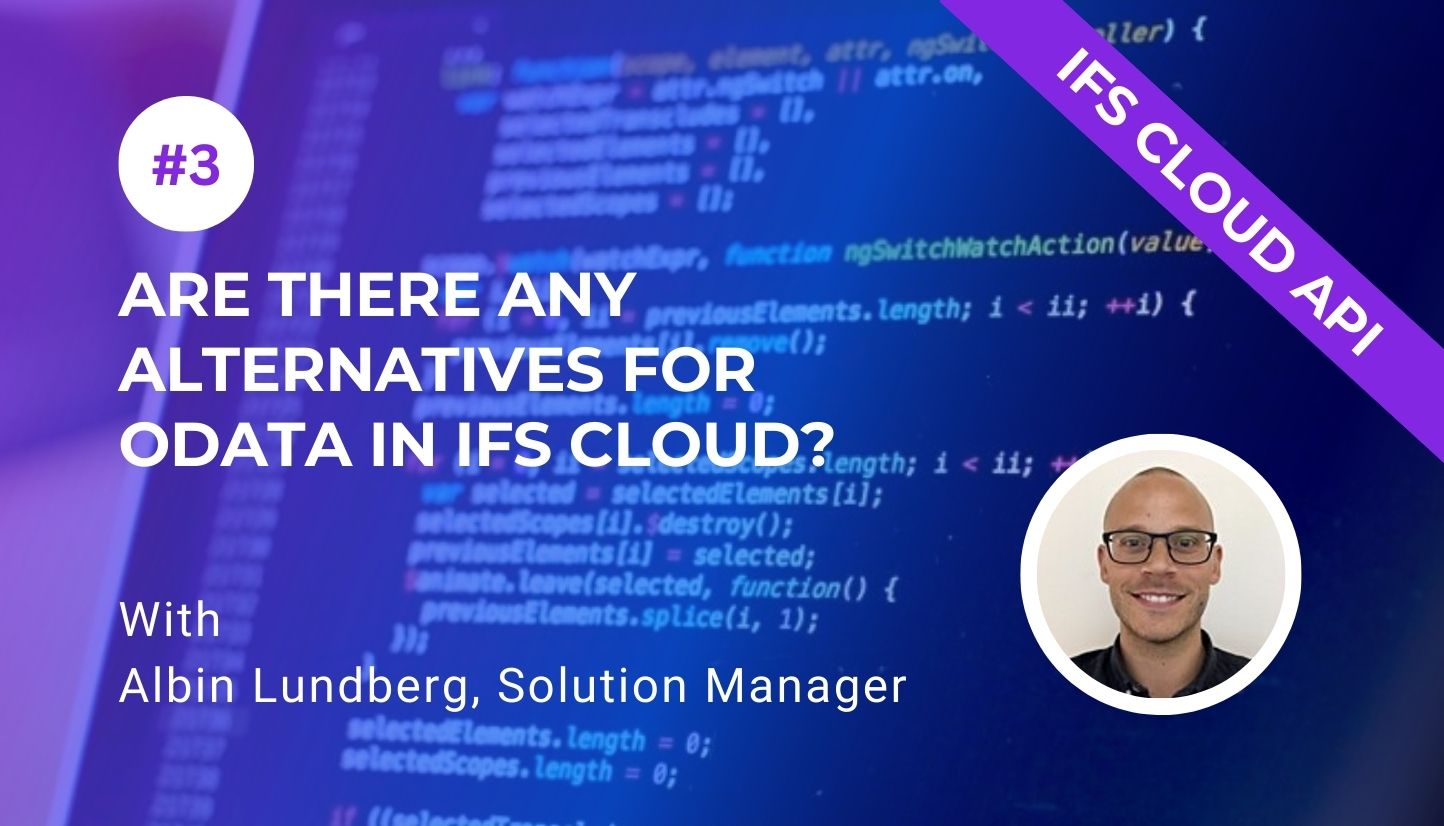

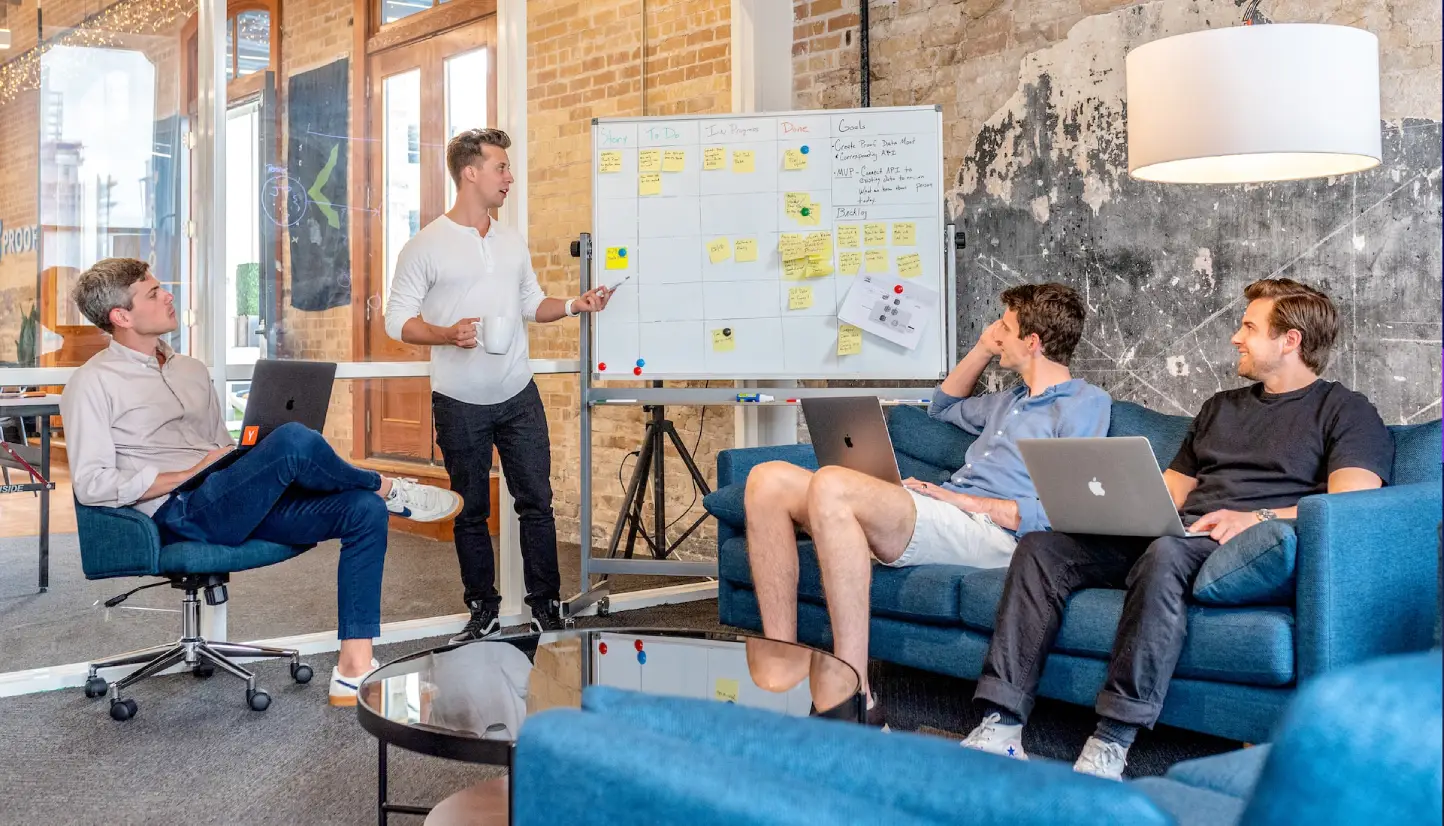
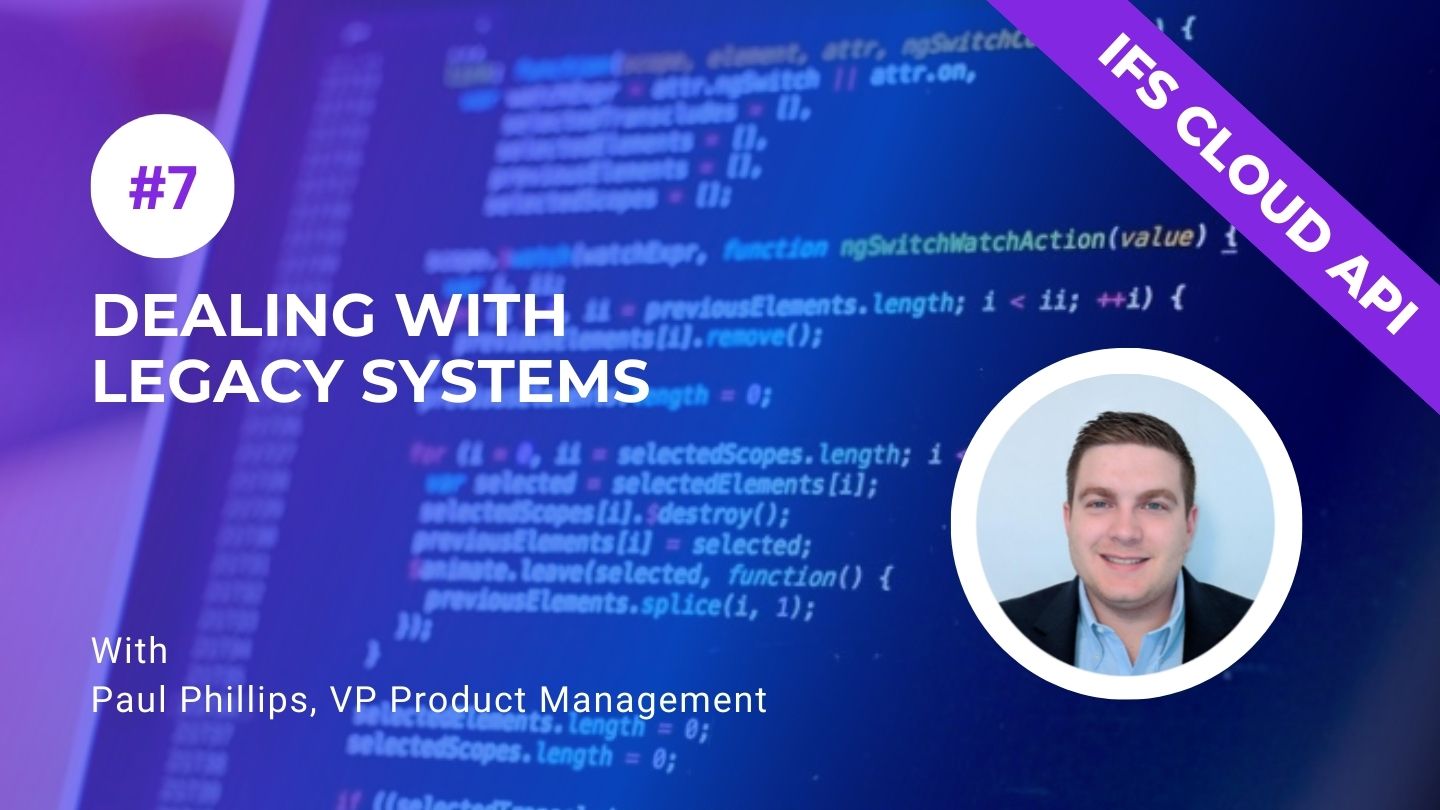
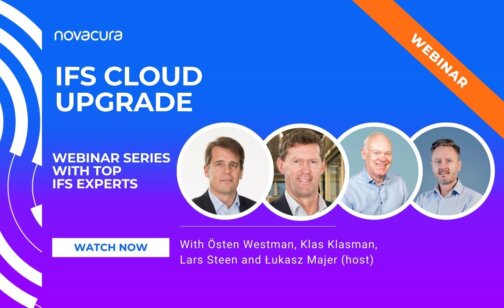