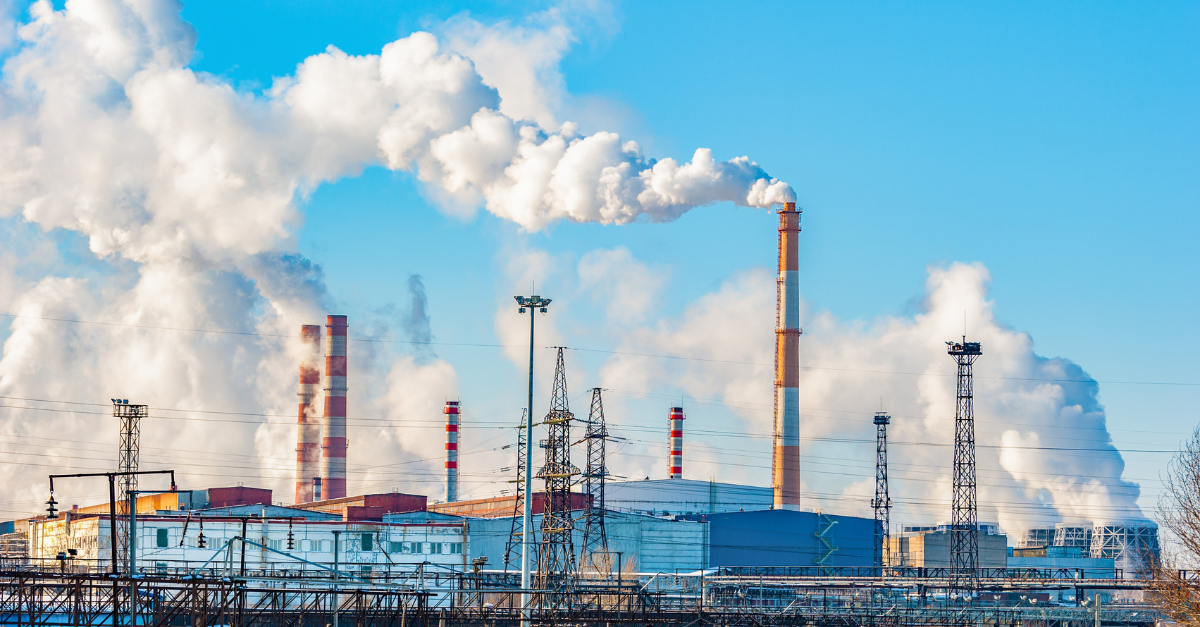
To manage means to measure. And your management decisions are as good as the quality of data you used to base them on. Management decisions are made based on “business systems” (Reporting systems – business intelligence, ERP systems, Planning systems APS, MES systems). But these systems have problems with acquiring appropriate information from original information sources.
Integrating the systems would be a solution to this, but it’s challenging due to two problems:
- On the Shop floor side – different devices have different protocols, some are new and some can be over ten years old.
- There are various business systems on the IT Systems side (APS, MES, ERP, MRP, WMS, QMS). They all use different protocols, provide other information and have independent databases (usually not synchronized).
What Is Shop Floor Control Software?
Shop Floor Control (SFC) software typically – but not always – part of a Manufacturing Execution System (MES), is a tool that captures, compiles, and analyzes the data needed to make your manufacturing tractable. This set of software constantly gathers data on human input as well as automated systems to inform what is happening right on the shop floor as work is in progress.
With shop floor management software, you gain the ability to monitor every detail of factory activity in real time. Detailed reports can reveal essential metrics such as machine runtime, material usage, work remaining, and overall production efficiency. These insights empower managers to make timely, informed decisions that can improve productivity and reduce downtime.
Moreover, SFC software can provide a broad perspective that spans multiple departments, individual machines, or even various manufacturing sites. This capability allows for the tracking of key performance indicators (KPIs) from numerous data sources, offering a comprehensive view of the factors driving your company’s production performance. By leveraging SFC software, businesses can pinpoint areas for improvement and better understand the variables influencing their overall output, helping to optimize operations and support continuous improvement across facilities.
Solution
The low-code BPM platform, Novacura Flow can integrate with all devices on the shop floor side as well as all systems on the IT side. This makes it an ideal solution for bridging the gap between equipment and business systems.
Protocols that Novacura Flow support – by devices side
How we can communicate with different products:
- Via a rest-based IoT-Hub, as Azure IoT
- Via a OPC-UA server
- Via a machines PLC over ModBus
- Directly with a machine over TCP/IP
- Directly from the Novacura Flow-app with a device over BLE (Bluetooth Low Energy)
What type of equipment can we connect?
- Production Robots – automatically read all information, detect downtime, track the number of cycles, and identify alerts.
- Vision AI cameras – to identify mistakes, take action and record the “incident” for quality purposes
- Semi-automated Machines used for production – like CNC, 3D Printers – as above, to read information about performance progress, number of prepared components, downtime, alert detection
- Different gauges/measurers – measure various parameters on the shop floor, such as dust, humidity, temperature, noise, vibrations, and power consumption (including voltage and amperage).
- Internal access control system – to monitor if a worker leaves or enters the warehouse, track their availability, and notify managers when a person is not logged into the work center.
- Warehouse automation systems (such as automated pick-up systems, movable shelves) – to read some info about performed operations/problems/warnings
- Internal transportation units (such as forklifts, micro-trains, trailers) – to read necessary parameters like utilization, numbers of km traveled, who uses the machine (if protected by some ID card), read important operation parameters and warnings.
- Industry scales – e.g., to measure the weight of raw materials at each production stage and to weigh packed finished goods before delivery to ensure the pallet/package contains the correct items.
- Quality control apparatus – e.g., read quality inspection results, number of tested elements and warn about anomalies.
If you think that IoT integration is not enough, and you need some more complex solution, check the other applications that Novacura can deliver:
What else can we deliver?
Novacura Flow is not only a gateway to connect devices. It also connects people (workers) by offering a mobile app that could be used by shop floor workers to shop floor reporting, machine monitoring, preventive and corrective maintenance, alerts, etc.
That way, we can measure how employees perform the manual work. It opens an additional layer of information for management (business) systems – that way, these systems have information about devices and “real-time” information on how people perform their work. It all gives a complete insight into what is going on the shop floor and helps analyze historical cases.
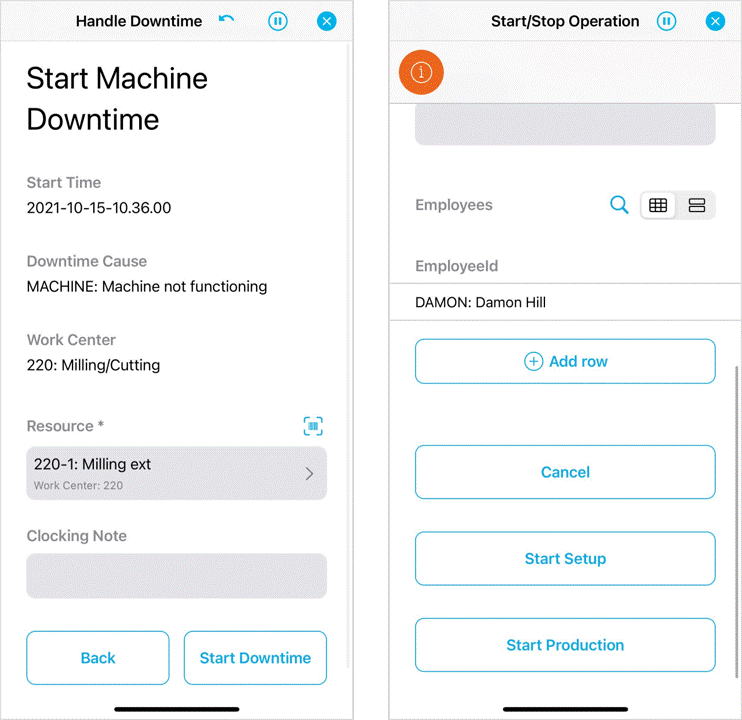
Novacura Flow Portal adds an extra dimension to Novacura Flow where you can control your entire business. Customers can use the portal to display machine statuses, produced/scrap count, queues, productivity graphs and more. All of this, live on a big screen. We have a special display mode in the Portal just for this.
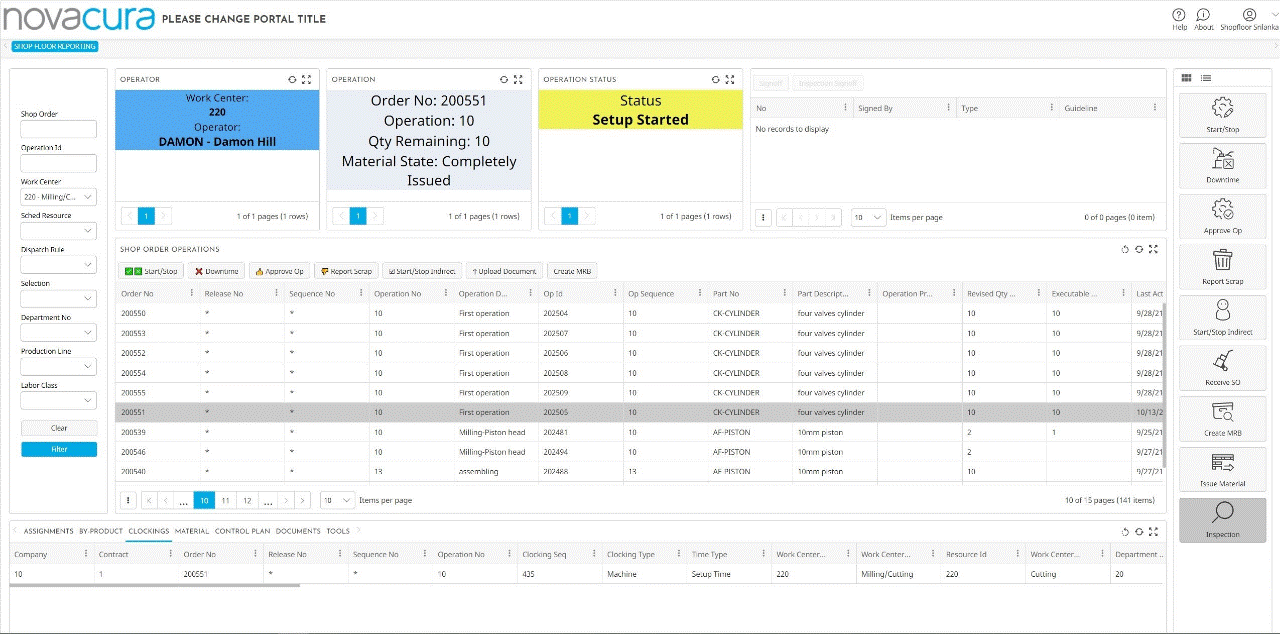
Benefits of integrating equipment with ERP:
- Faster management decisions – If a problem occurs with one machine, the shipment can be stopped a second after. We don’t have to wait until a paper report comes to the planning specialist.
- Better, more accurate planning- factual execution information comes faster to the people who plan production. So they can rearrange plans regularly (seeing that something went wrong and that the production unit won’t be able to realize the current project)
- More accurate/precise/objective data – data measured automatically are more detailed and precise than data reported manually by people. People may make mistakes when reading measurements and may conceal the actual information.
- Process improvements- having more accurate / more complete historical data, you can track all adverse incidents and avoid them in the future. You can find some coincidences between different numbers connected to the incident (e.g., a lousy electricity voltage measured just before a particular machine breaks down). By understanding this, you can eliminate the root causes that lead to incidents.
- Operational efficiency measurement – you can set objective KPIs for your divisions, production lines, or individual work centers when you have accurate data that reflects the true state of production.
- No waste of working time on additional reporting – all information can be read directly from the equipment.
- Flexibility – Ability to quickly add new IoT measurers to measure temperature, pressure, humidity, vibrations, etc. Even if they are not a standard part of the machines (heavy equipment).
This online integration with your production equipment gives you more direct and objective access to all the numbers that are crucial to correctly evaluating and optimizing the OEE (overall equipment efficiency) factor.
An ultimate benefit – Industry 4.0 implementation
There is one more significant benefit of implementing Novacura Flow when viewed from a broader perspective. This integration solution helps you make a substantial step forward toward Industry 4.0.
In the Industry 4.0 concept, every single device and machine is connected to the integrated ecosystem, where all the information is gathered without any delays and is fully automatic. In that context, Novacura Flow could solve one of the key problems that companies have in implementing an Industry 4.0 strategy: there are always a lot of different devices, machines to connect with.
On the other side – you have a lot of business systems that use various APIs. So it is very hard to connect all of them because they use unique communication standards and protocols. Some of them are old and are really hermetic for integration. In such a context, Novacura Flow can be a perfect solution, acting as an Industry 4.0 Integration hub, offering 50+ ready-to-use connectors to various systems and devices.
You may consider Novacura Flow as the starting point of your trip to Industry 4.0. You can start with Novacura Flow, connect it to your ERP system, and then add more and more systems and devices. That way, you will be able to use an iterative approach, which is probably the only possible way to reach Industry 4.0 assumptions one day.
To summarize
As Novacura Flow can both control and monitor the production process, we can make sure that the right things are produced, using the right components, producing as many units as on the order, counting scrap and more.
In the longer run, connecting and controlling machines is also reducing the need for workshop staff, decreasing production costs and increasing efficiency. This means competence can be used in a better way. Instead of doing monotonous work, people can focus on preventive actions and continuous improvements.
With all that being said – Novacura Flow is no doubt a good solution to solve some of the common barriers that exist when companies implement their Industry 4.0 strategy