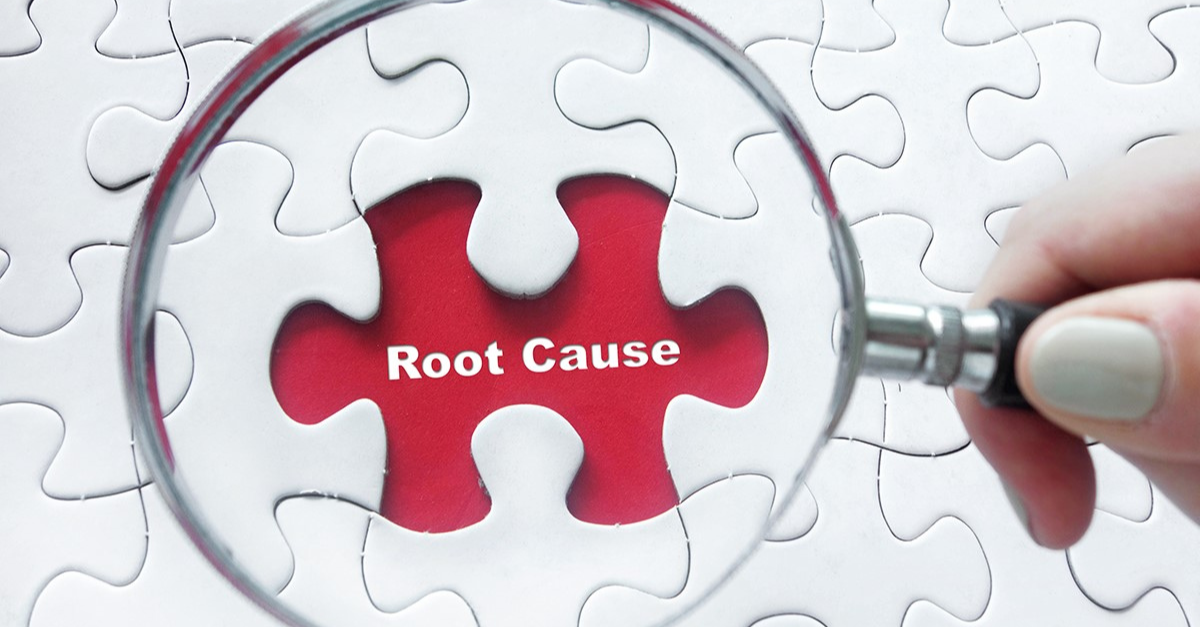
Not every business process is perfect in its first iteration. In fact, almost all business processes need some finessing to achieve the best results. But figuring out exactly which improvements to make can be a challenge. What’s the solution? A root cause analysis.
What is a root cause analysis?
A root cause analysis is a way to identify the true cause of problems, issues and inefficiencies—in business processes or anything else, really—and to develop an approach for responding to them. Fixing the underlying cause of a problem, instead of just treating the symptoms, will improve process quality and save time, too: time you might be spending right now fixing the symptom of the problem instead of the problem itself.
Think of it this way. Imagine you find mold in your house. What’s the first course of action? You might want to start by cleaning the surfaces with mold on them. But if all you do is clean the surface, the mold will keep coming back. In order to get rid of the problem for good, you need to deal with the problem at its source.
How to perform a root cause analysis on a business process
- Assemble a team. Yes, you can conduct a root cause analysis on your own. But when you’re trying to find the best solution to a problem, it’s important to get input from many different perspectives. For example: if the root cause of the problem has to do with data migration, and you don’t know how or where company data is stored, you won’t have the right knowledge or perspective to get to the root cause.
- Together, define the issue. Be as clear and specific as you can.
- Analyze the issue using one (or more) of the root cause analysis techniques described below.
- Once you’ve determined the root cause of the issue, decide on the best plan of action.
- Implement your action plan.
Root cause analysis techniques
Five Ms
The Five Ms is a root cause analysis used in both Lean and Six Sigma. The idea behind the five Ms is to look at the issue from different perspectives to try and pinpoint the cause, not just the symptoms.
The standard Five Ms are:
-
Man/mind power
-
Machine (equipment, technology)
-
Material (includes raw materials, consumables and data)
-
Method (process)
-
Measurement/medium (inspection, environment)
Some people like to add a sixth M here: Mother Nature. Some people like to use an E instead: Environment. But the process is still the same. Think about the problem through the lens of these different factors, and see if you can find the root cause.
Once you’ve analyzed the problem with the Five (or Six) Ms, you may want to visualize the problem in an Ishikawa (or “fishbone”) diagram. This video shows you how:
\
Five Whys
The five whys is pretty much as the name suggests: looking at a problem and asking “why” five times. Here’s an example:
Problem: Items aren’t being shipped on time.
Why aren’t they being shipped on time?
There’s not enough stock in the warehouse.
Why isn’t there enough stock in the warehouse?
The warehouse is too small.
Why is the warehouse too small?
25% of the warehouse space is filled with old office equipment.
Why is there so much office equipment in the warehouse?
We put it there when we renovated the office.
Why did we keep the old furniture when we renovated the office?
Don’t know.
Solution: Remove the old office equipment from the warehouse to free up space for new stock.
You’ll know that you’ve reached the root cause when you don’t have a good response to “why”. In the example above, it took five “whys” to get to the root cause: in some cases it might only take three or four. In other cases, it might take six or even seven.
Tips for getting the best results from your root cause analysis
- Beware of confirmation bias: it can get in the way of finding the real root cause of an issue.
- In addition, be aware of your own internal bias. You may think you already know the answer before you start analyzing. But are you 100% sure? This internal bias can blind you to other causes (and even blind you to the root cause).
- Correlation does not always equal causation. It might take a few attempts to get to the heart of an issue. Don’t let that discourage you. Every step towards fixing a problem is a step in the right direction.
- There might be more than one root cause. Make sure to explore and analyze all possibilities.
If you’re having trouble getting to the heart of an issue with your business processes, a root cause analysis can help you gain clarity on the issue. Just make sure you’re creating solutions that focus on the cause of the problem, not the symptoms.