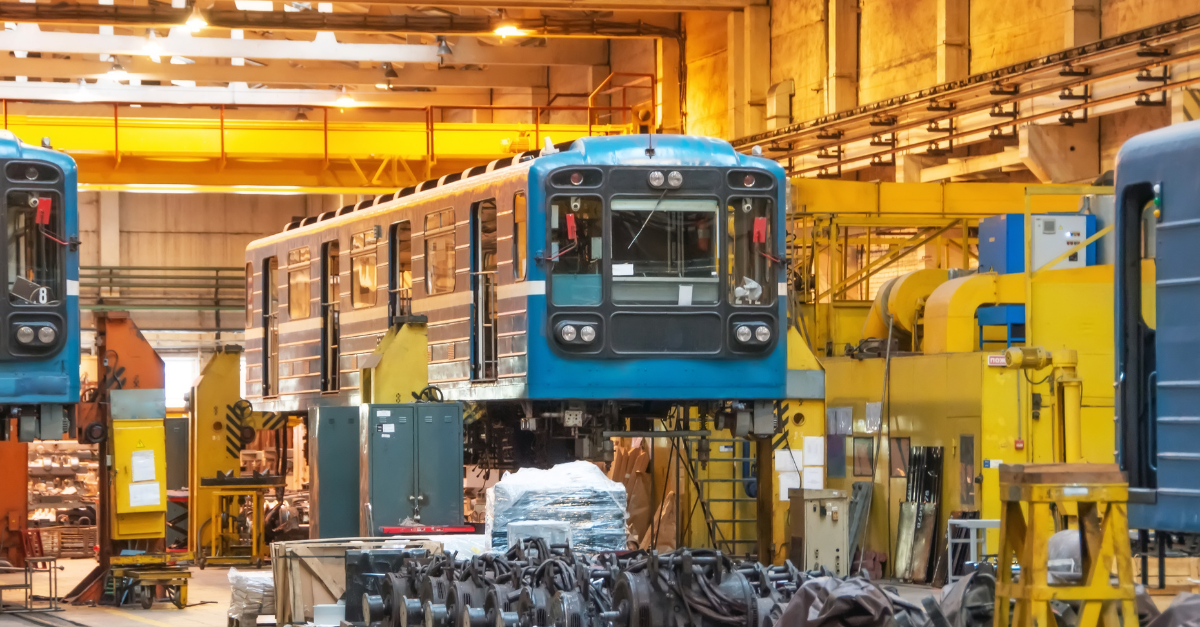
Mobile solutions are the future of business — a fact that is already well-known to managers all over the world, including Western Europe and Asia. Why are they still used by so few firms in Poland? Are they afraid of the high costs of deployment? Or maybe that it will be time-consuming and unprofitable? Nothing could be further from the truth.
Is it possible to streamline processes and save money at the same time? We asked Marcin Gudynowski, who is responsible for warehouse management and cooperative purchases at PESA SA. His experience highlights how low-code warehouse management and mobile ERP solutions can revolutionize operations, fostering digital transformation in warehousing.
What problem was your firm facing when it decided to expand its ERP system?
At PESA, we sought a solution to streamline the flow of materials, both within the organization and at points of contact where materials were received or shipped. We needed warehouse solutions that would ensure transparency and quantifiability in our processes while increasing efficiency from the start. However, after surveying the market, we found that most standard Warehouse Management System solutions were primarily designed for distribution firms, leaving a gap for Polish manufacturing companies.
Despite assurances from consultants, preliminary discussions revealed that their competences fell short of our expectations. We needed warehouse solutions that would ensure transparency and quantifiability in our processes while increasing efficiency from the start. This highlighted the importance of adopting bespoke warehouse logistics solutions rather than relying on generic offerings.
The entire solution, both Flow and other elements such as notifications, labels and integration with the logistics portal, has enabled us to reduce the time required to process incoming goods by 13% (...)
What was the greatest challenge for you?
At PESA SA we carry out several dozen projects every year, and the variety of the process paths taken or the methods of, for example, packing the same material, given a database of up to 20,000 indexes, is hard to even define. We took the decision to carry out a deployment based on our existing ERP system. Very quickly, while we were still at the concept stage, it turned out that the proposed solution would not provide us with the flexibility that our organization required. While conducting another market survey, we discovered a company specializing in warehouse software solutions and process enhancement tools that were highly customizable. Their approach allowed organizations to parameterize processes internally, provided they had the appropriate skills. This low-code warehouse management strategy was so unique compared to standard industry practices that we doubted its feasibility at first. However, with their warehouse logistics solutions, the implementation succeeded, exceeding our expectations and proving its value for warehouse management optimization.
What solutions were proposed by the company that you decided to work with?
We decided to work with Novacura. That company’s solutions are based on the standard of our ERP system, and the tools it offers are very easy to parameterize. This makes it possible to act very quickly and extremely flexibly in preparing a solution, and the high level of competence of managers and consultants was confirmed during the project.
Our expectations were that multi-variant warehouse processes would be handled online, using a scanner or tablet. Before the Novacura project, we had not been able to find solutions or consultants who were willing to listen to us and understand our processes.
Moreover, Novacura showed that the parameterization of the system to meet needs as they arose would take less than 1–3 days. Previously we had been used to the standard experience that modifications after the writing of a large specification took between two and three weeks, and even then the results were usually unsatisfactory.
With Novacura we outlined the processes, discussed them over three days, and the system was in place and ready for testing in less than two months! In our work we use the Flow tool.
How do your employees use Novacura Flow?
We use Novacura Flow on scanners and tablets in all warehouse processes involving incoming goods: notified orders, management and recording of shipments, and traditional receipt of ordered goods. We also handle all warehouse movements, and most importantly, the making up and delivery of shipments for production. We have also deployed processes for stocktaking, kanban filling, recording of movements of logistical units within the organization, and many others.
What goal did you set for the deployment?
The main goal of the project was to increase process efficiency and transparency. The pre-existing problem, or imperfection in the process, was the lack of responsibility of employees for the tasks they performed. They were anonymous in the system, because registration in the system took place reactively, via office staff. What’s more, most of the work was done on paper sheets. And here I can state quite frankly that there has been a huge change. We often pose the question of whether it is the firm that should adapt to the software, or the software to the firm. In my opinion the answer should be a balanced one, lying somewhere in the middle. On the one hand software must not impose unnatural changes on the organization, but on the other hand, good software supported by a well-designed warehouse management platform should force employees to make certain positive changes which in the final balance will lead to increased efficiency or, as in our case, greater process transparency.
What specific expectations did you have before Novacura, and were they in fact fulfilled?
Our main expectations were system flexibility and the ability to handle multiple variants of solutions. And, of course, the speed of making changes, as I have already said. Now I can say with 100% certainty that these expectations have been fulfilled to the maximum possible degree.
Do you notice a change for the better after deploying Novacura Flow?
Novacura Flow is a very dynamic environment which makes it possible to shape and improve processes with just a little computing knowledge. It enables additional hidden resources of mobility to be drawn out of them.
The entire solution, both Flow and other elements such as notifications, labels and integration with the warehouse logistics solutions portal, has enabled us to reduce the time required to process incoming goods by 13%. But above all the process has become more controlled and transparent. We are now analysing things which, before this deployment, we were not even able to detect. On the basis of this, we are planning further improvements.
And what do the employees themselves think about Novacura Flow?
This is a big change for our employees — moving from paper sheets to electronic online flow control. Of course this requires a change of approach and some training. Nonetheless, employees can already see the results of the deployment, and moreover they themselves are proposing changes, which following evaluation are put into practice on a continual basis.