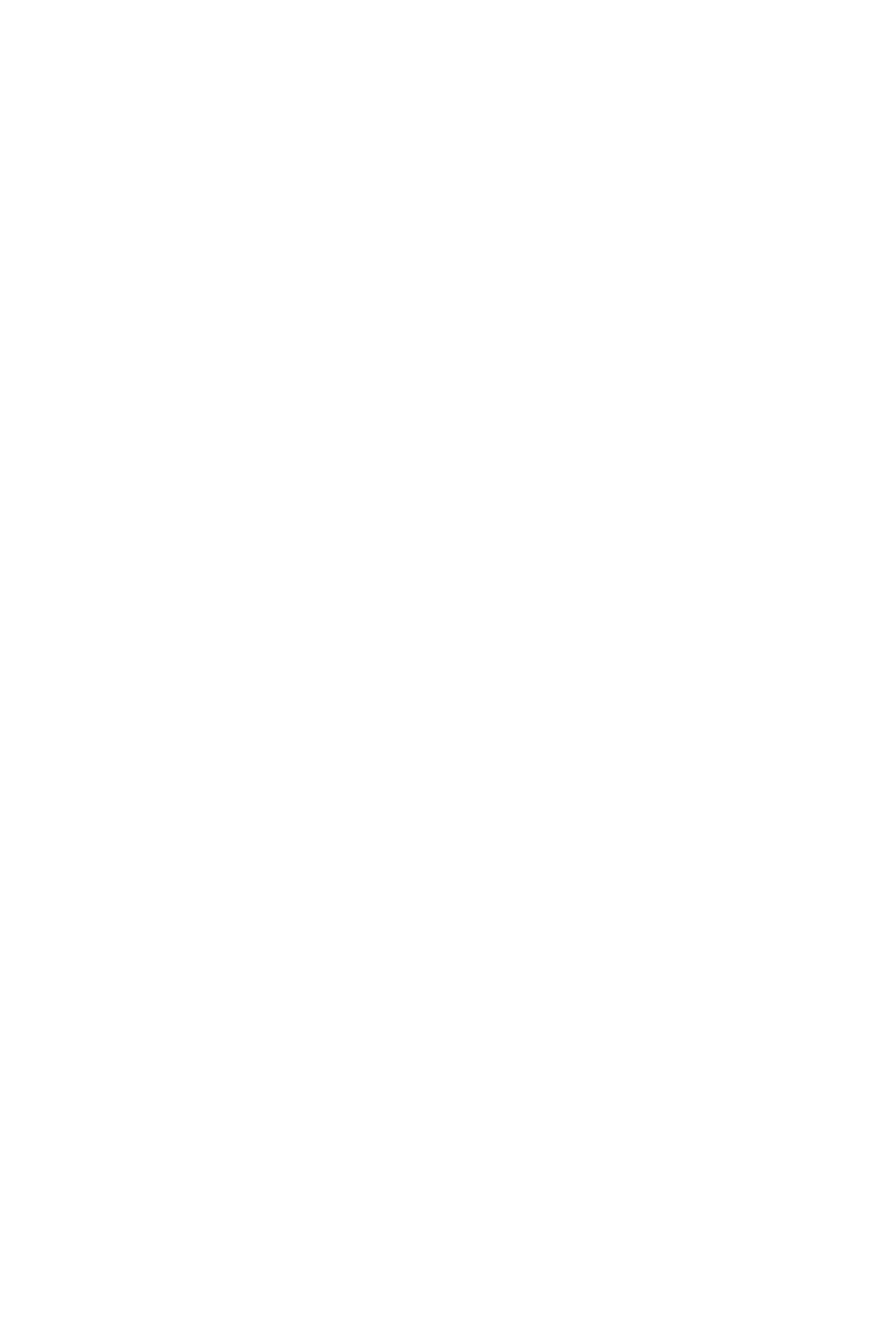
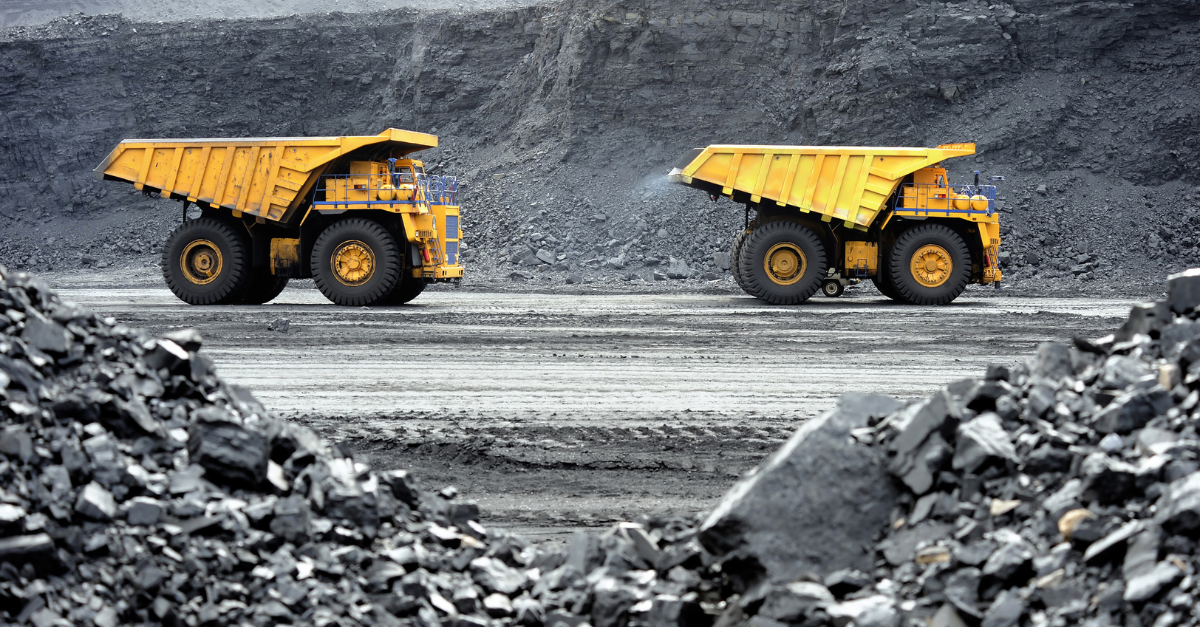
MINING INDUSTRY SOFTWARE SOLUTIONS
Increase forecast accuracy, reduce incidents, decrease cost per ton and improve facility uptime in mining operations with dozens of customizable applications dedicated to your ERP system!
Key capabilities of mining industry software:
01. Provide reliable data for the operational planning
The operational planning process is effective and provides reliable plans when it has access to detailed historical statistics and freshly updated information about ongoing operations. Novacura Flow helps gather this information by acting as a communication gateway and monitoring tool between mining equipment and business systems. It can retrieve the data directly from machines (using OPC-UA, PLC or ABB 800xa). Novacura Flow also gathers current work statuses from all employees thanks to the Mobile Work Order application.
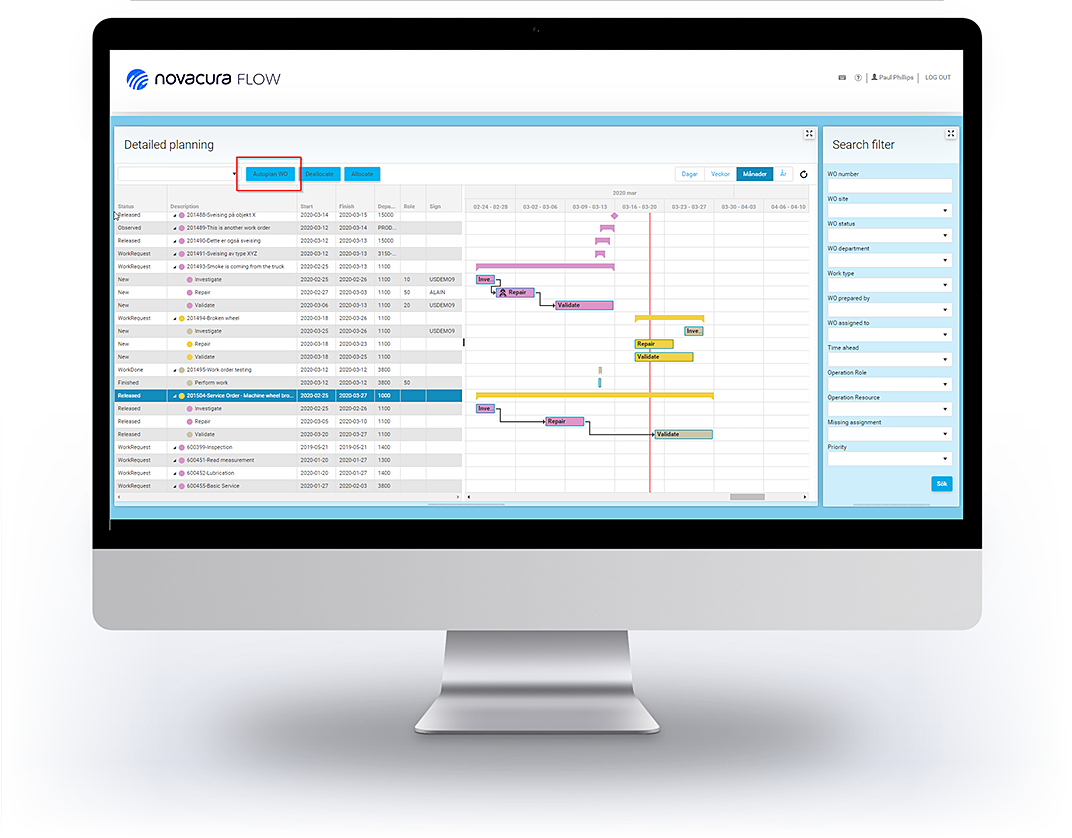
02. Improve planning with visual tools
Novacura Flow offers an advanced visual interface that can be used to improve the operational planning experience. The planning specialist can switch different charts (including Gantt, Kanban, and bucket chart). The solution can present plans from different perspectives – the machine, the person or the production site. And all these perspectives can be shown simultaneously to make planning very efficient.
Thanks to the connectivity with operational applications, plans can be then converted to work orders and synchronized with mobile applications used by operators. This makes Novacura Flow an ideal mining management software, providing a robust solution for efficient planning, scheduling, and execution in the mining sector.
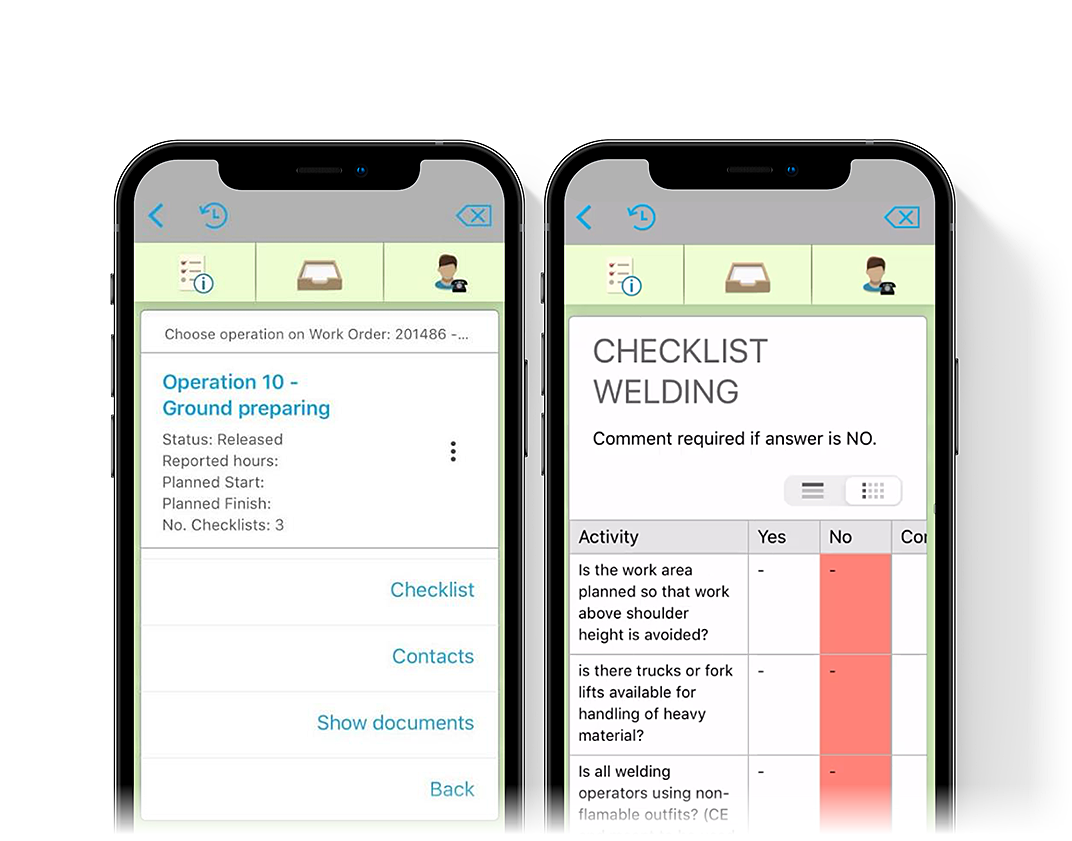
03. Streamline mining operations
With the Novacura Flow solution for mining, every mine crew member can be connected to the solution thanks to the “Mobile work order” application. With this powerful mining program, all users get their daily tasks with priorities. The application for the mining industry can provide them with further details (additional documentation attached to the task). The application can force a specific way of task execution by providing a performance checklist that needs to be completed by the team member before finalizing the task. The application collects status changes on the tasks and transmits them directly to managers who can then use them to plan operations. And it all works as well in offline mode.
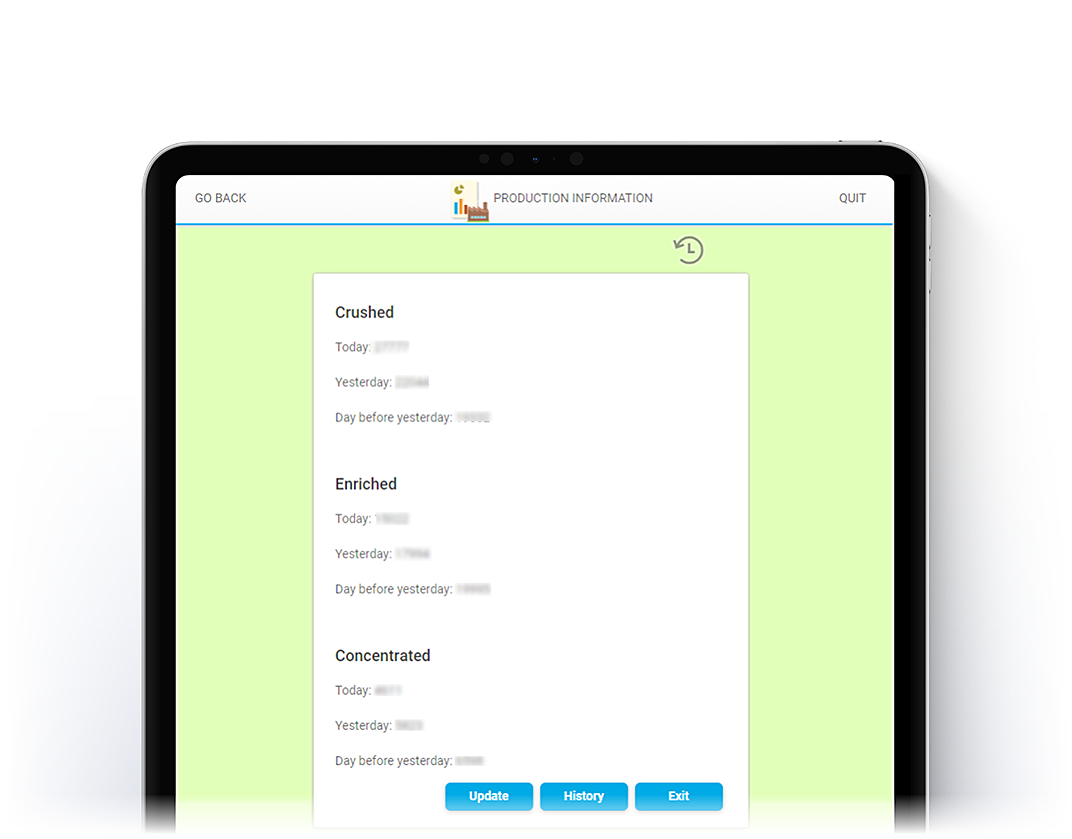
04. Supervision supported by real-time-data
Thanks to the “Mobile work order” application and iIOT connectivity – Novacura Flow can gather tons of data about the performance of tasks and all unexpected situations (like downtime or damage).
This data can then be transferred into KPIs and presented on different charts using the Novacura Flow Portal. Employees can also see their individual goals and check their current performance in their mobile applications, with solutions designed specifically for employee management in the mining sector.
05. Control the weight on every stage
Because of Novacura Flow's ability to directly connect to the iIOT devices for mining, the entire product journey through the mine can be precisely traced. Novacura Flow can use industrial scales and read the weight of the product at every stage (i.e before crushing and after). Our solution can then compare losses versus standard and alert the operator or supervisor if the loss exceeds an acceptable threshold. Thanks to it, the manager can identify the exact location of the loss and take measures to increase efficiency (reduce cost per ton).
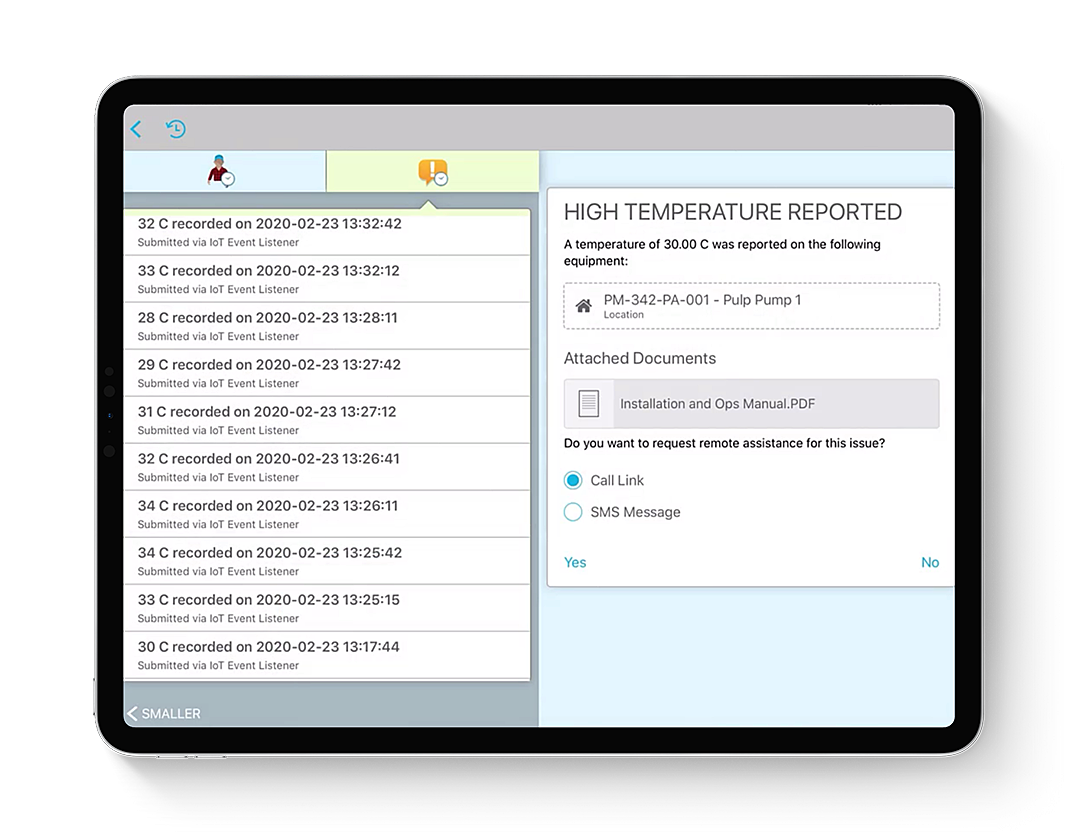
06. Integrate the maintenance
In our software solution, all areas of mining from planning, to logistics to maintenance operations are integrated. Thanks to that, maintenance operators get access to all the statistics gathered from the machines (like pressure, temperature, or km traveled by the truck). Directly in their application, using our mine maintenance software, they can start a new preventive maintenance action if any of the parameters warn them.
The maintenance tasks are visible in the mobile application dedicated to maintenance crews – they can see task details, asset documentation and report work statuses.
Moreover, all maintenance actions (planned or ad-hoc) can be included in the updated production plans via the planning module. This makes our solution a comprehensive software for mining, perfectly suited for enhancing efficiency and reliability across operations.
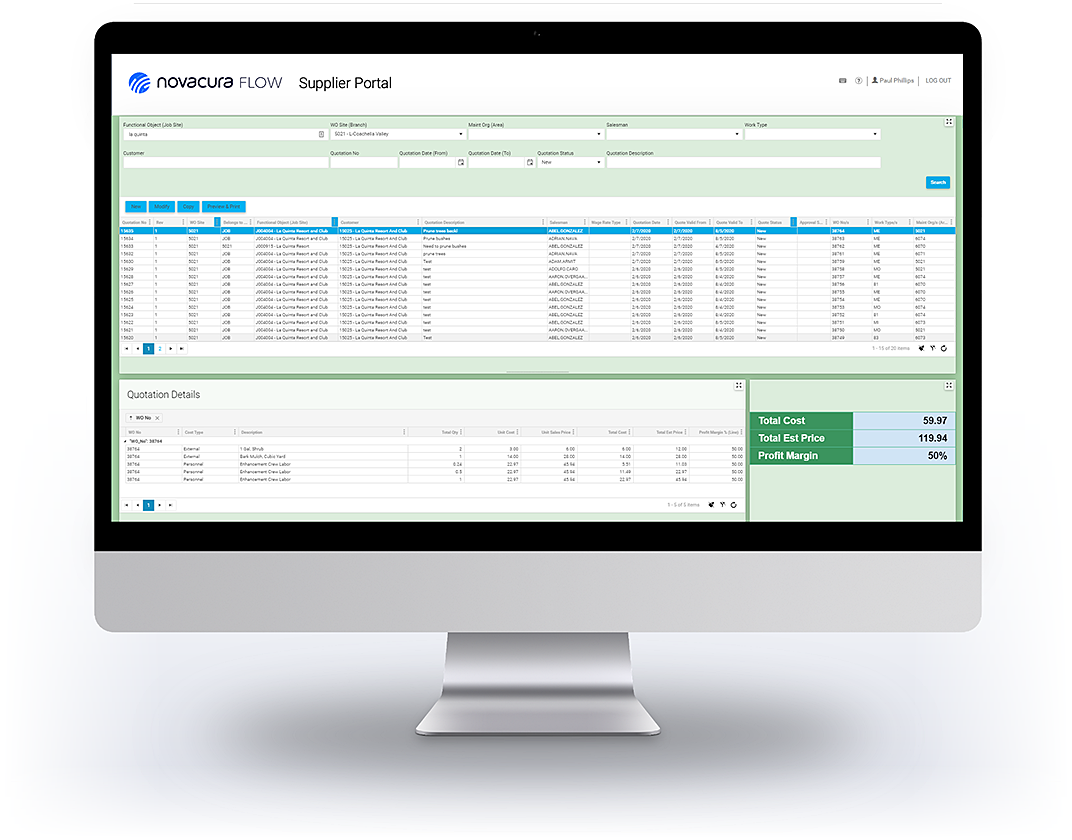
07. B2B Portals
Novacura Flow Portal is perfect for B2B Portals. This software solution is perfect to manage the communication with mine customers and suppliers (maintenance subcontractors, laboratories etc.). The B2B portal can be used by 3rd parties to define new customer orders, confirm deliveries, present and approve financial settlements and handle invoices flow.
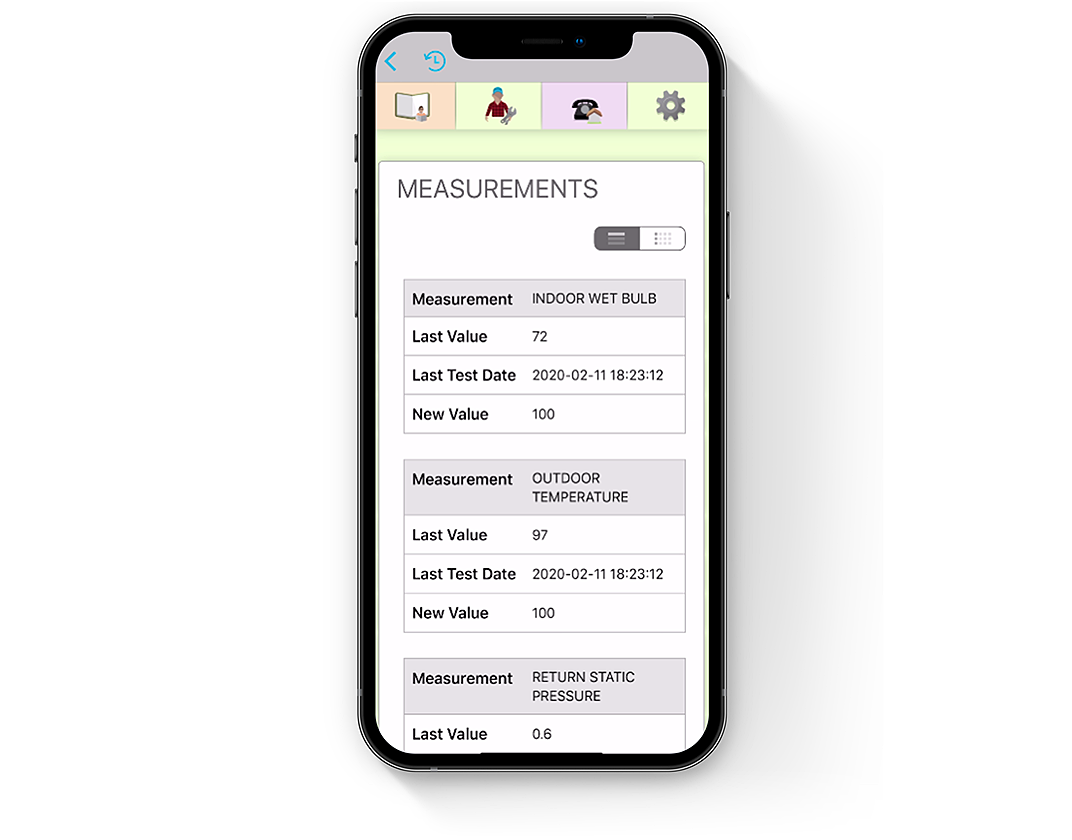
08. Safety & Compliance Management System for the Mining Business
Being compliant with regulations, especially in the safety area is crucial in mining. All the safety, quality, and environmental checklists can be managed within a specific mobile application. Inspection results are then stored in the database and can be printed if necessary. This mining risk management and compliance software solution ensures that all regulatory requirements are met efficiently.
The application can also manage employee certificate validity and automatically alert if a team member lost his entitlement to perform a complicated or dangerous task. And as a versatile underground mining software, this solution helps maintain safety standards and regulatory compliance across all operations.
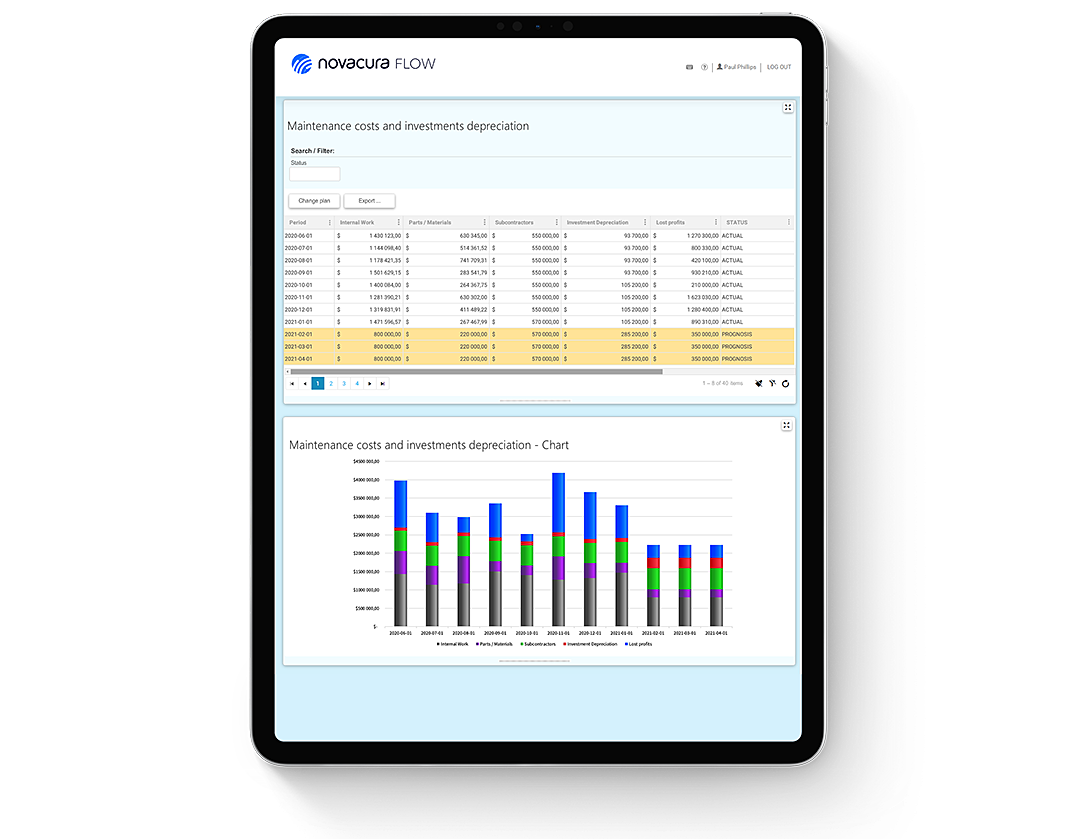
09. Strategical investments management
Our software solution can support mines in strategic investment planning. Because all the modules of this solution are integrated – managers get access to all historical data – from asset utilization via maintenance history and ending with the drilling area efficiency and financial costs of operations. By combining all these dimensions managers can evaluate trends and take the right strategical decisions based on facts. For example, they can decide whether it is better to invest in new equipment and thus reduce maintenance costs that increase month by month.
Novacura Flow can also help plan and execute investment projects, supporting the budgeting phase, defining scope, reporting project progress, project finance analysis, supplier management and much more, making it an ideal mining management software.
Mining software solutions and supported areas:
Below we summarize the list of areas supported by our package of mobile applications for mining companies:
01:
Operational planning
- Gathering the data about real performance directly from the machines and from mobile work order applications
- Visual planning using a multi-dimensional perspective
- Integration between plans and work orders in mobile apps – task assignments based on the plan
- Integration with laboratory – direct access to the attached analysis – mining operations are always drilling in the most cost-efficient area
02:
Mining operations management / Enrichment / Laboratory
- Mobile work orders for mine crew – access to task details, task performance checklists, task status reporting, time tracking & reporting
- Complete workforce (crew) management for mining, including mobile solution (task assignment, task progress monitoring, reported time verification, holidays scheduling, replacements)
- Downtime reporting
- Incident reporting
- Precise production monitoring – from drilling to every enrichment stage
Mobile app for the lab assistant to scan the drill-hole RFID and printout an analysis barcode
03:
Mining Automation / Technology Software Solutions
- Offline mode available for all mobile applications
- Industrial IoT (IIoT) connectivity for the mining industry – Integration between machines and ERP using OPC/UA, PLC, ABB 800xa / Siemens standards – real performance & maintenance statistics processing
- Computer Vision
- Augmented Reality for remote support for maintenance operators
04:
Mining Supply Chain & Logistics Management
- Monitoring of the entire material / product flow at each delivery point by integrating IoT industry scales / RFID
- Mobile apps for truck drivers – GEO location monitoring – ability to track product stock at each location
- KPI dashboards to analyze truck utilization (ton*km) / monitor material loss in logistics
- Transportation planning based on operational plan and real amount of product on particular stages
05:
Maintenance & Asset management in Mining
- Maintenance tasks planning – Integration with operational planning
- Mobile Work orders for maintenance (preventive & reactive) (incl. asset documentation management, inspection checklists off-line mode support)
- Tools management / Spare parts management
- Automatic gathering stats from machines to determine preventive tasks (i.e. based on the ton-km for trucks)
06:
Safety & Compliance
- Compliance audits planning
- Audit execution on mobile devices with offline capabilities and checklists
- Integration of Health, Safety & Quality instructions in all work processes (applications)
- Safety incident management
- Safety certificates management/ access privileges checking
- Safety reporting & analysis
- Printable documentation management
07:
Operational supervision / Strategical management
- KPI Dashboards / Portals – presented information based on the data gathered in a real-time
- Team target boards
- Operational effectiveness analysis (cost per ton, material losses on every stage, drilling area effectiveness etc.)
- Maintenance effectiveness analysis (MTW, MTTR, maintenance costs, MTBM)
- Asset utilization analysis (downtime, ton*km, defects)
- Safety events monitoring
08:
Contractor management
- B2B portal for customers – formal communication with the customers inside one portal solution
- Features: demand confirmation, customer order processing, deliveries confirmation, financial settlements and more
- B2B portal for maintenance & laboratory subcontractors
- Features: task assignments, performance reporting, financial settlements, maintenance stats accessing and more
09:
Strategical management
- Strategical analysis support – access to the historical data, trends analysis
- Strategical projects planning – ROI analysis
- Strategical project planning – scope, financials, resources, suppliers, schedule etc.
- Strategical projects execution – progress supervision, cost tracking and suppliers management
Our Software Platform:
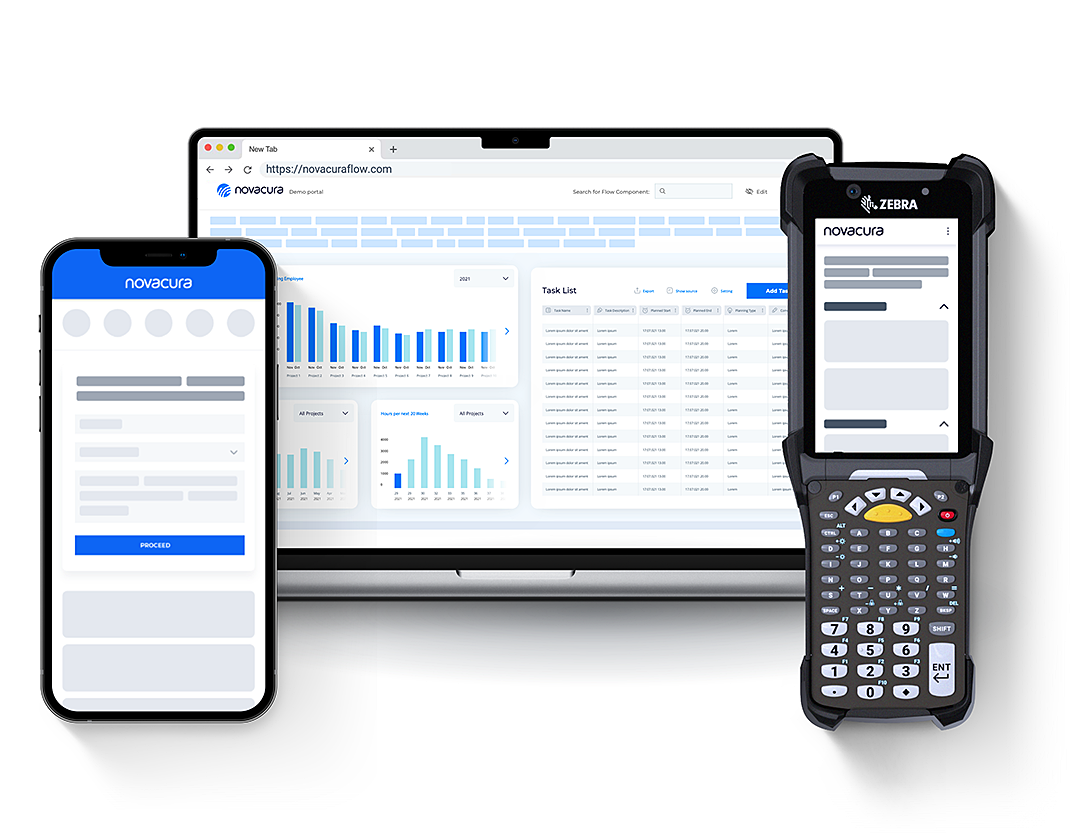
Interface optimized for heavy industries
Our applications run on a sophisticated software platform – Novacura Flow. One of the key foundations of this platform is to run on every device – from barcode scanners, via mobile phones and tablets, to desktop workstations equipped with large screens.
But we are not just another SaaS software that offers that. We have optimized our user interface for users that operate in harsh conditions. I.e. – our applications for mining industry can run in the field without any internet connection using a specific offline mode.
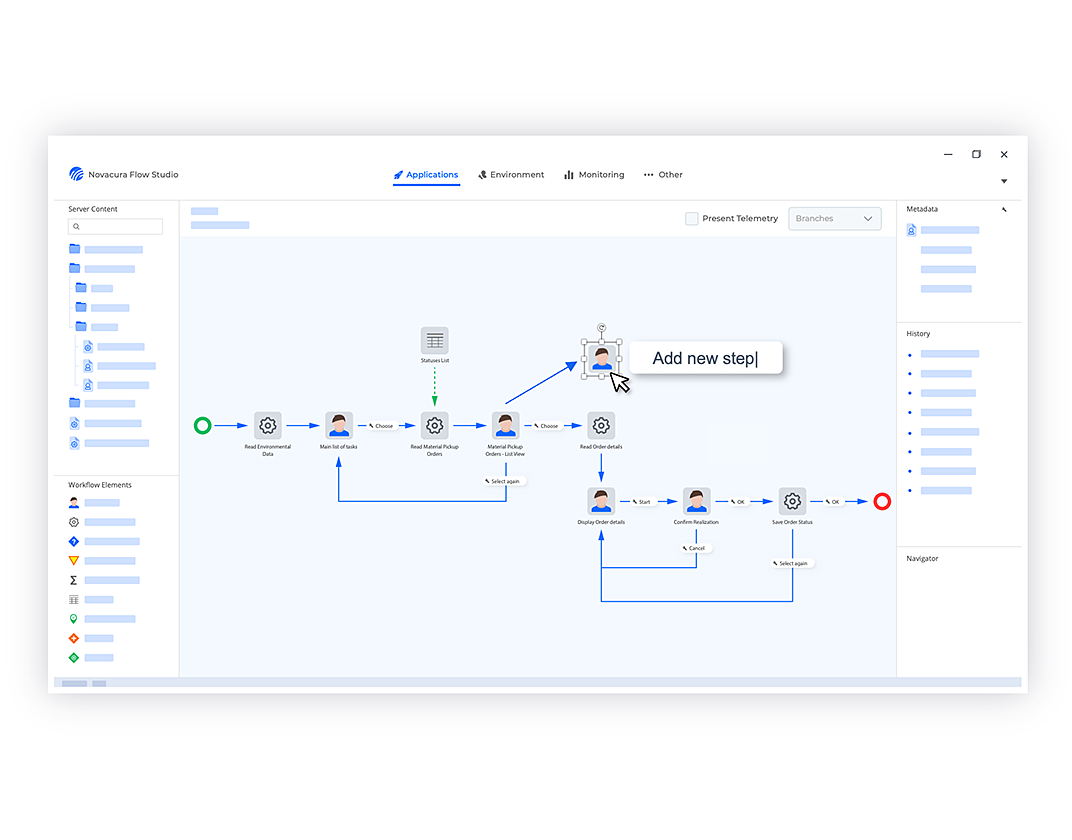
Ready for changes thanks to its low-code core!
Every company is different from the other. You might have specific processes and require unique features and we are ready for that! We created our applications for mining based on the low-code platform.
Our applications are not hard-coded so our customers can modify them or clone them and create variants. And they can build their own applications. And thanks to the low-code engine they can create apps by drawing them like they draw a business process.
Integration with ERP. Deep integration!
Our low-code platform Novacura Flow and industry applications can play a vital role in the mining company. But we are not forgetting about the ERP for mining and quarrying production industry!
We treat the ERP system as a primary system – all master data, operations and reported information is stored there. And everything that users do in Novacura is immediately visible in the ERP! This is possible because our platform has specialized online connectors for integration with ERP software for mining industry. You can think of Novacura Flow as an alternative, mobile and efficient user interface for your ERP. Thus, you can easily adopt Novacura Flow without changing surrounding processes which can still run in your ERP!
THE IMPLEMENTATION PROCESS IS SEAMLESS AND RISK-FREE:
1. Mature methodology
We have a mature implementation methodology divided into stages (like initial requirements workshop, feasibility study, etc.) — that way the whole project is predictable and can be fully controlled and coordinated by us.
2. Years of experience
We have 17+ years of experience in mining. There is a library of ready-to-use applications which can be
presented to the customer and customized according to his needs. This library is available in the Novacura Flow Marketplace.
3. Low-code platform
Novacura Flow is a low-code platform – so we can implement everything our customer wants, and every element can be adjusted to specific customers’ needs.
4. Industrial connectors
We have a solid base of industrial connectors – the technology is no longer a problem.
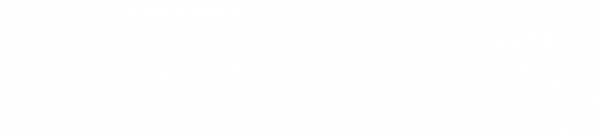
“With Novacura Flow we got the mobility capabilities and solution to retrieve data from different systems”
Martin Hjärtström
Technical Development Manager Kaunis Iron
CONTACT OUR EXPERT:
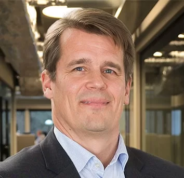