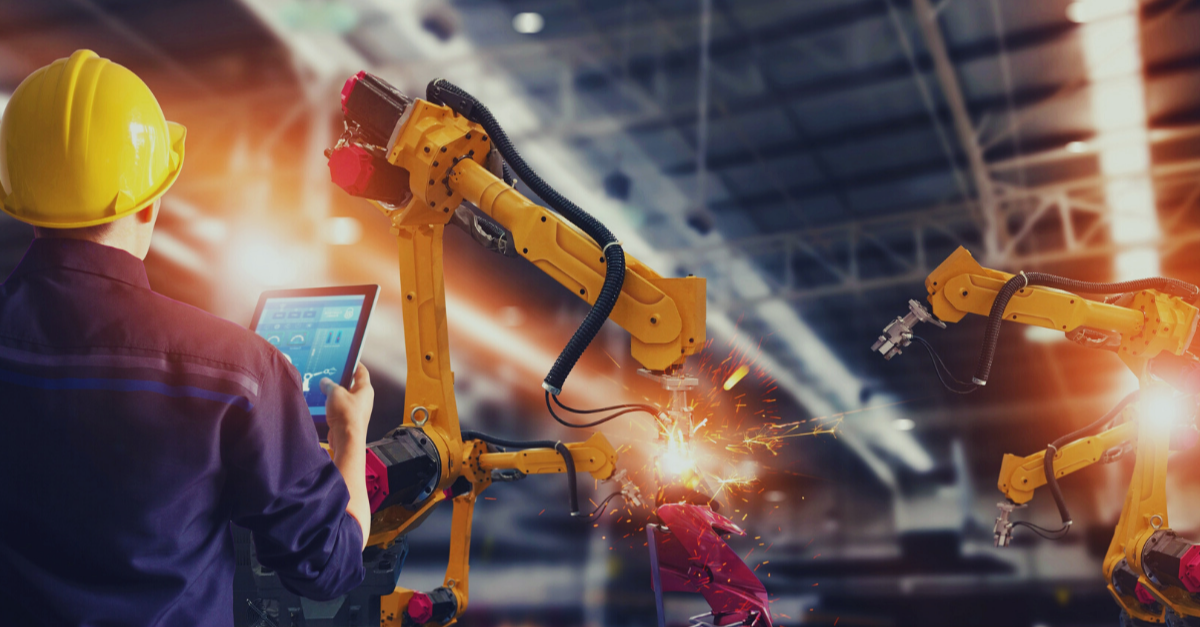
There is no doubt that COVID-19 has had a significant impact on Manufacturers and production downtime. It’s also not surprising that there has been an increased pressure to improve overall efficiency as a natural response to the global pandemic.
In speaking with our Manufacturing customers, we found three key efficiency challenges during the pandemic that consistently stood out amongst the rest. Knowing the challenges that exist—along with the root causes – is the first step in identifying solutions to improve productivity.
So, let’s take a closer look at the top three challenges that our manufacturing customers faced as a result of COVID-19:
Challenge 1: Problems in the supply chain
- Delayed deliveries disrupted production plans
- Limited availability of resources required manufacturers to shift production lines
- Supplier diversification was a necessity to avoid order fulfillment issues
Challenge 2: More competitive market
- Focus shifted from offline to online, putting more pressure on delivery time
- Manufacturers had to improve their Just in Time (JIT) strategies
- A reactive demand-driven approach was implemented as part of the JIT strategy
- The more competitive the online market, the higher the need for product configurations
Challenge 3: Internal problems
- Lack of personnel due to illness and quarantine measures
- Supply chain limitations and unstable demand impacted production capacity
- Enhanced hygienic procedures had a direct impact on production efficiency
Before we started interviews with our customers, we assumed that COVID-19 brought a lot of problems in terms of production efficiency. But we never assumed that the word “downtime” would be used so many times by our customers!
Fredrik Rosendahl
Novacura, Sales Director
DOWNLOAD complete 18-pages report
Manufacturing in the COVID-19 era
- Top 3 challenges for manufacturers during the pandemic
- What are the root causes of the challenges?
- Proposed solution
- How to implement it
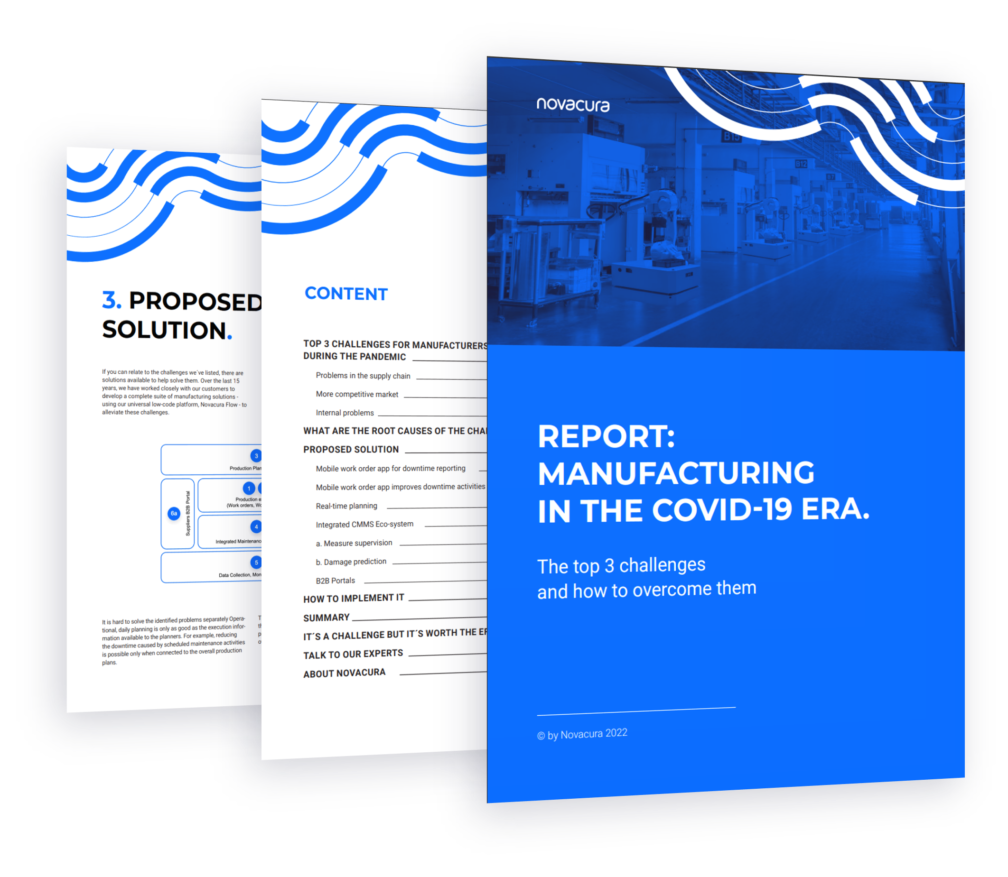
Related articles
:
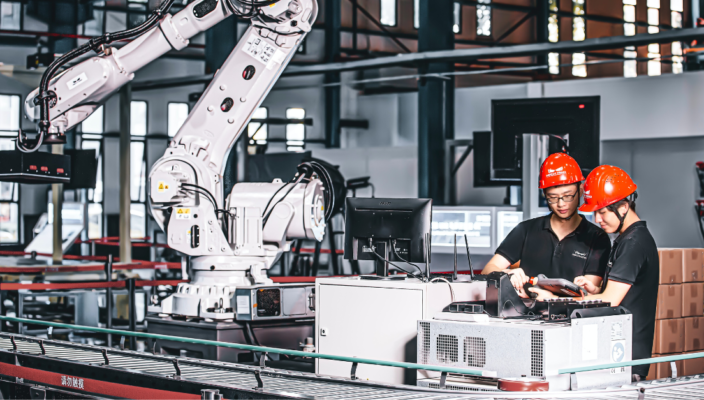
Quality inspections of the production line using computer vision and Novacura Flow
learn more
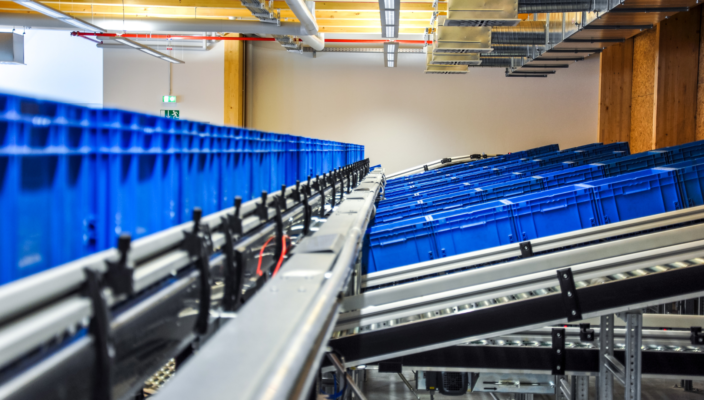
How to improve material traceability in manufacturing
learn more
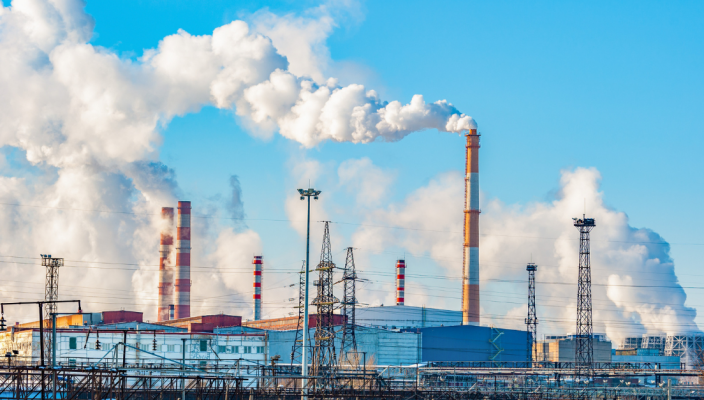
Shop Floor Data Collection Software: How to integrate equipment with business systems
learn more
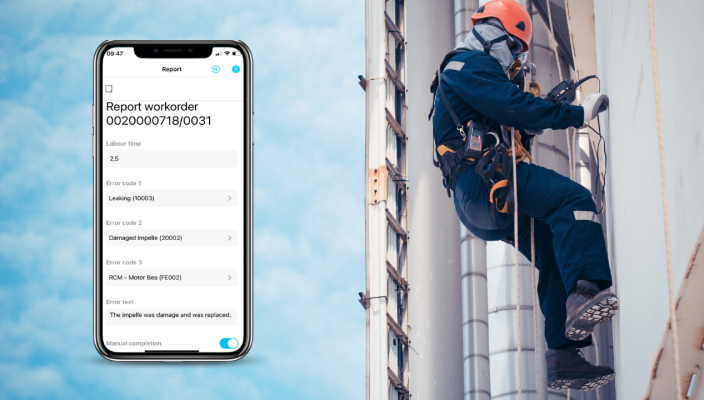
Field Service Management Software connected to ERP
learn more