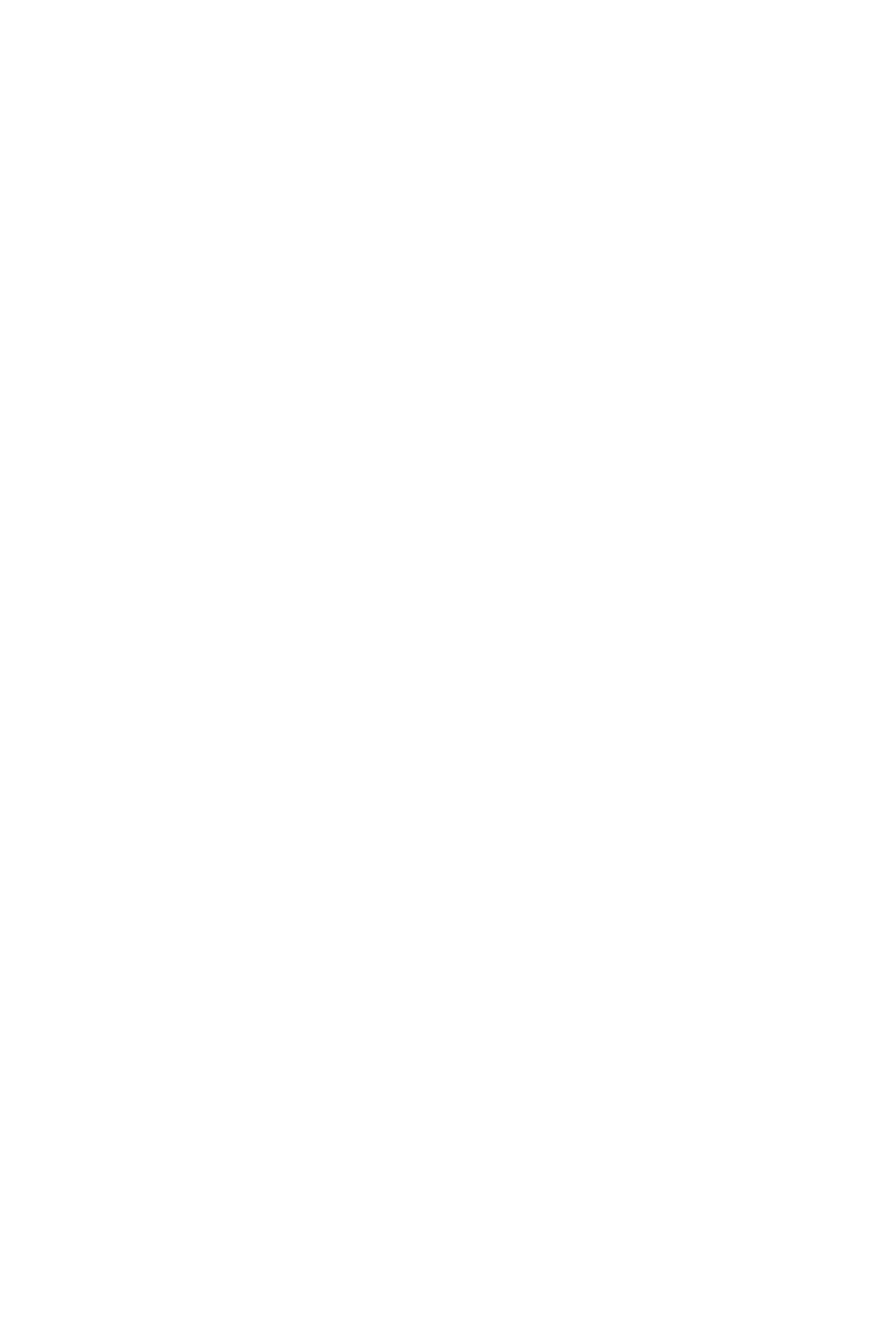
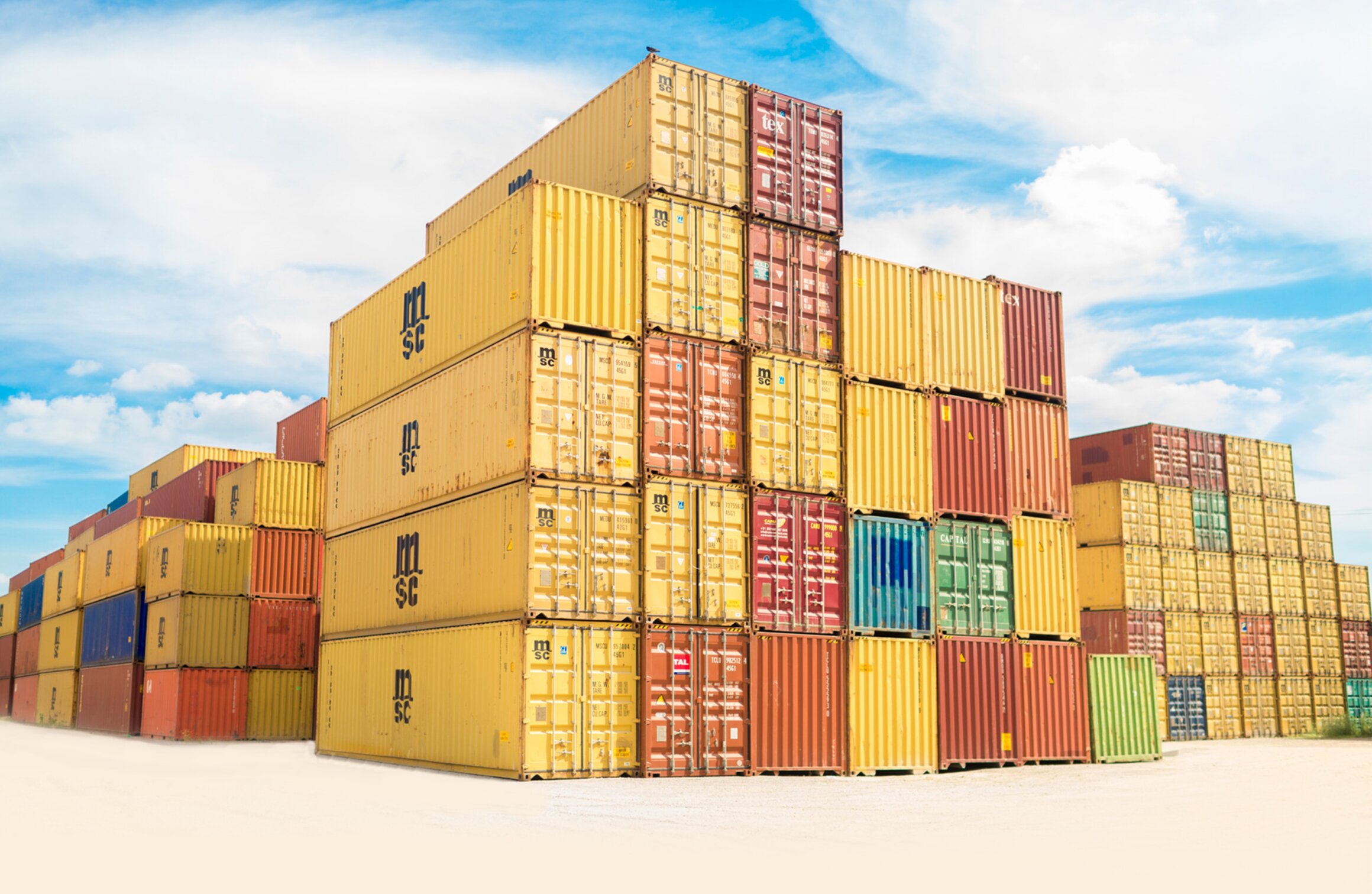
LOGISTICS MANAGEMENT SOFTWARE FOR YOUR BUSINESS
IMAGINE A WAREHOUSE WHERE EVERYTHING RUNS LIKE CLOCKWORK
No more paperwork overload, no more manual errors and 100% accuracy. You can make that happen with Novacura Flow — and it’s easier than you might think.
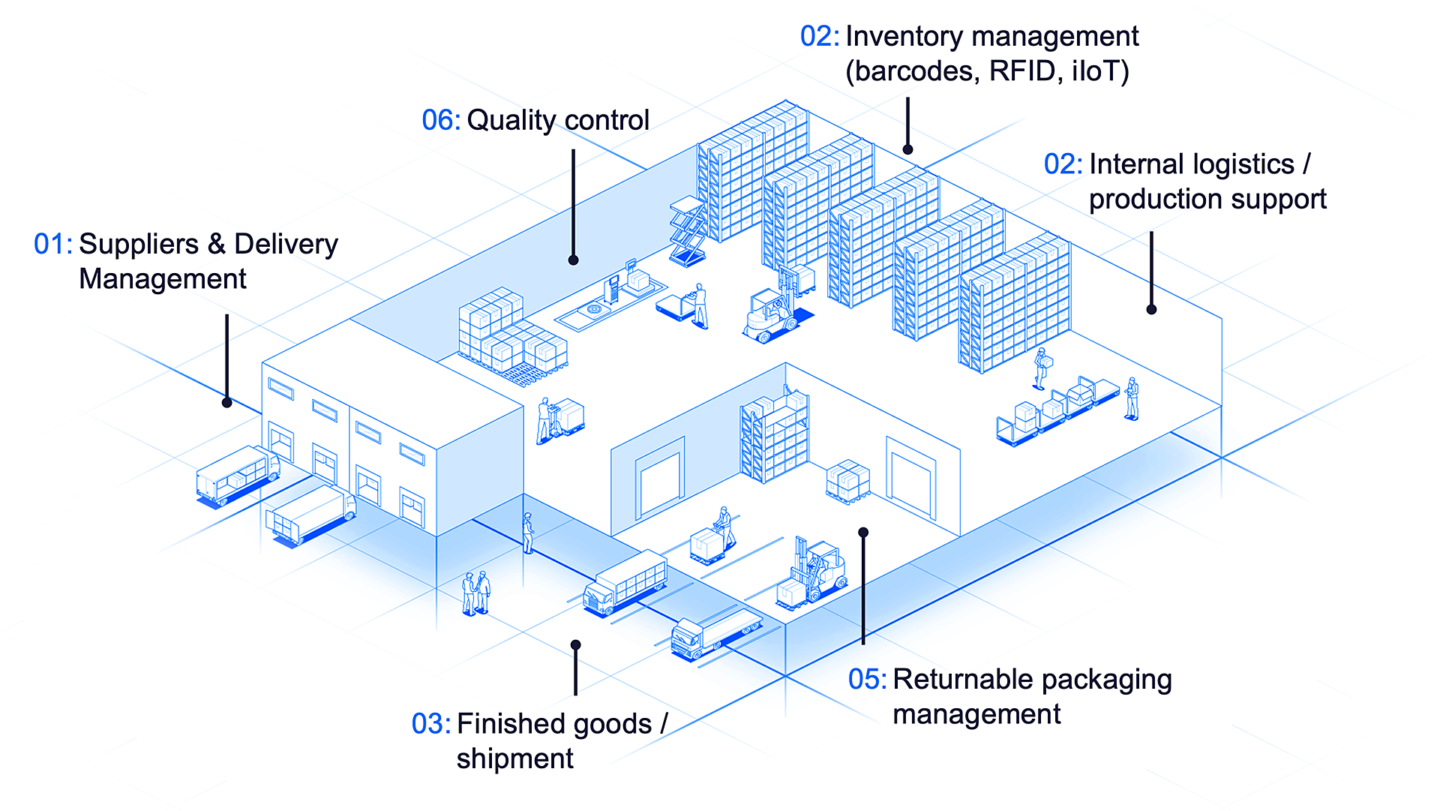
key capabilities of software for logistics:
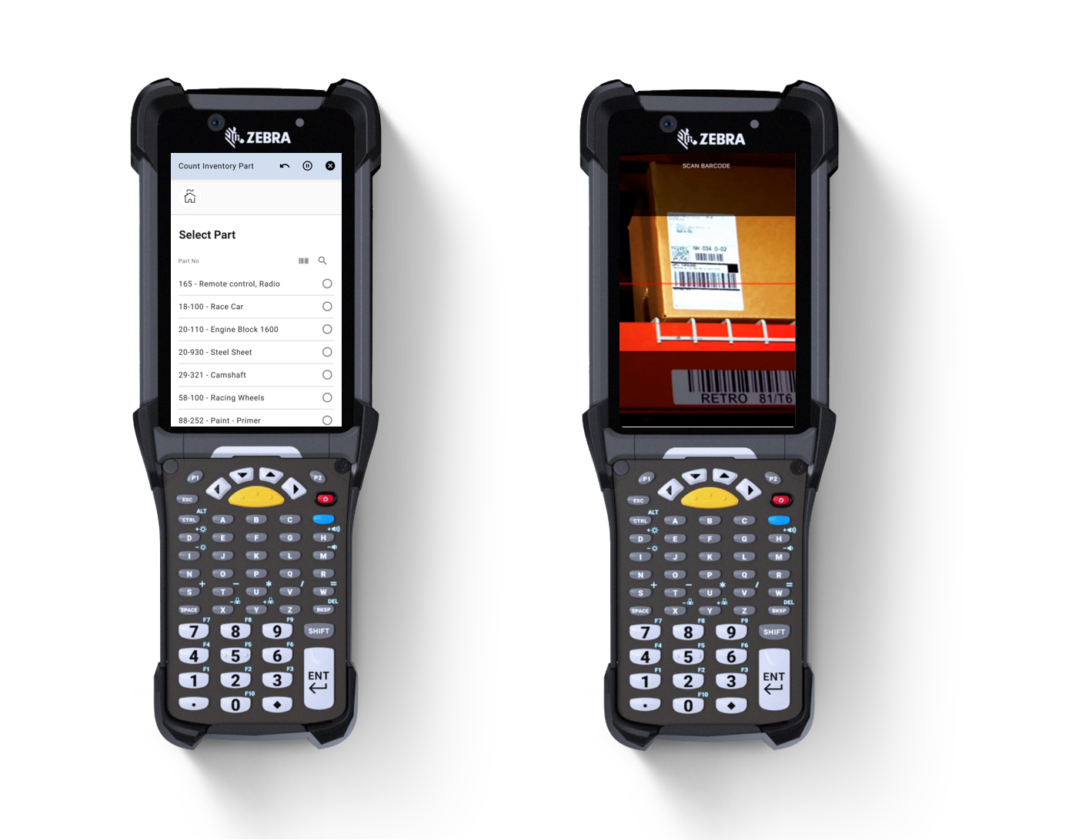
User-friendly logistics solution with mobile integration
Our logistics solution offers a very simple and effective user interface. We offer a set of mobile applications running on all types of mobile devices and systems: barcode scanners, tablets and smartphones. In addition, we offer a Portal solution to visualize complex data. It is useful for planning and reporting. This logistics management platform supports all important processes belonging to the logistic area, offering a comprehensive system that includes solutions for warehouse management software (WMS): deliveries management, picking, counting, inventory moves, shop floor cooperation, material traceability, finished goods shipment, internal logistics (material requisition processing, internal deliveries to/from production, packaging management), transportation management (route planning, fleet monitoring, deliveries scheduling) and more. By leveraging a cloud-based logistics platform, businesses can optimize their operations and streamline logistics workflows effectively.
Improve data-entry efficiency with barcodes and RFID
Novacura WMS Package supports two industrial standards especially important in logistics and manufacturing. Users can scan barcodes from any package, asset, or location. This ability is available automatically - each input field in the mobile application offers the possibility to scan the data instead of typing it by using the keyboard. The application can also be integrated with RFID gates and automatically track information about parts and finished goods moved inside the inventory. This powerful feature makes it a robust logistics and transport software solution.
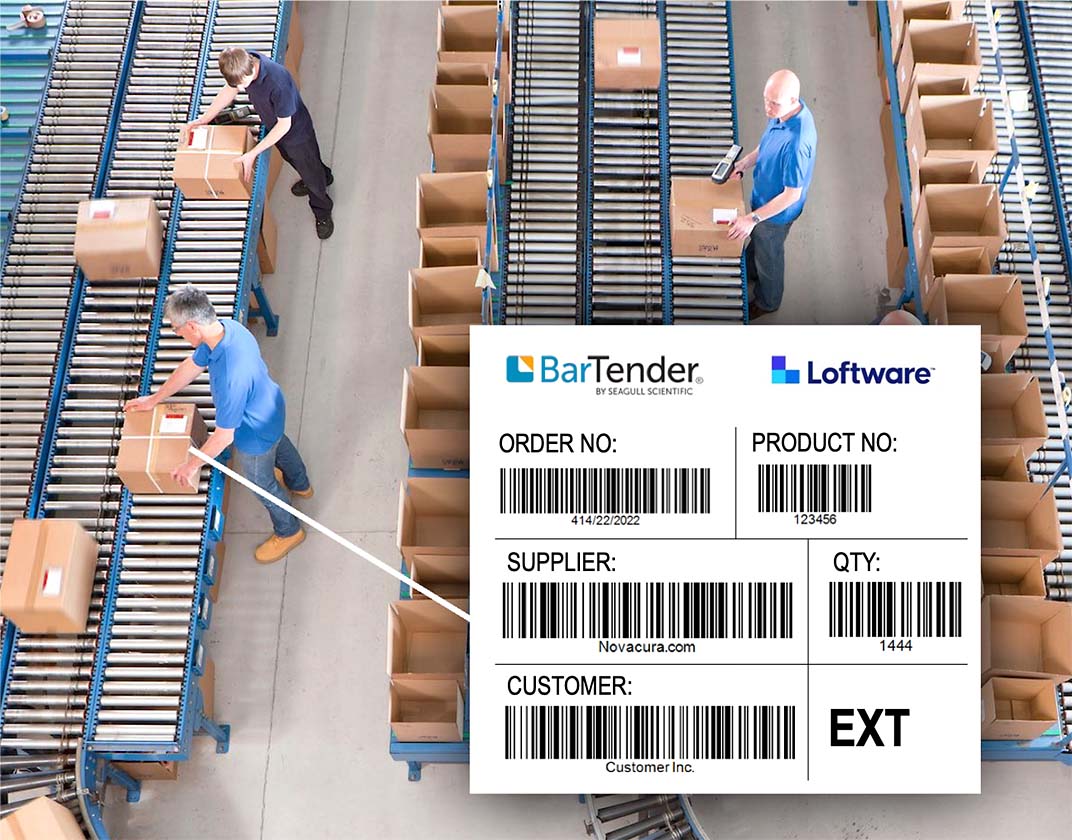
Print, scan and manage labels directly from the ERP application
Our WMS package is integrated with the labeling systems – Loftware (previously NiceLabel) and BarTender. Our mobile applications can initiate the label printing process and feed the label system with all necessary data. This operation can be done as one of the regular process steps meaning the user doesn't have to care about labels in a separate tool. This integration is bi-directional, which means that the warehouse solution understands all the information encoded on labels. This makes our system a robust logistics cloud software solution, perfectly suited for businesses.
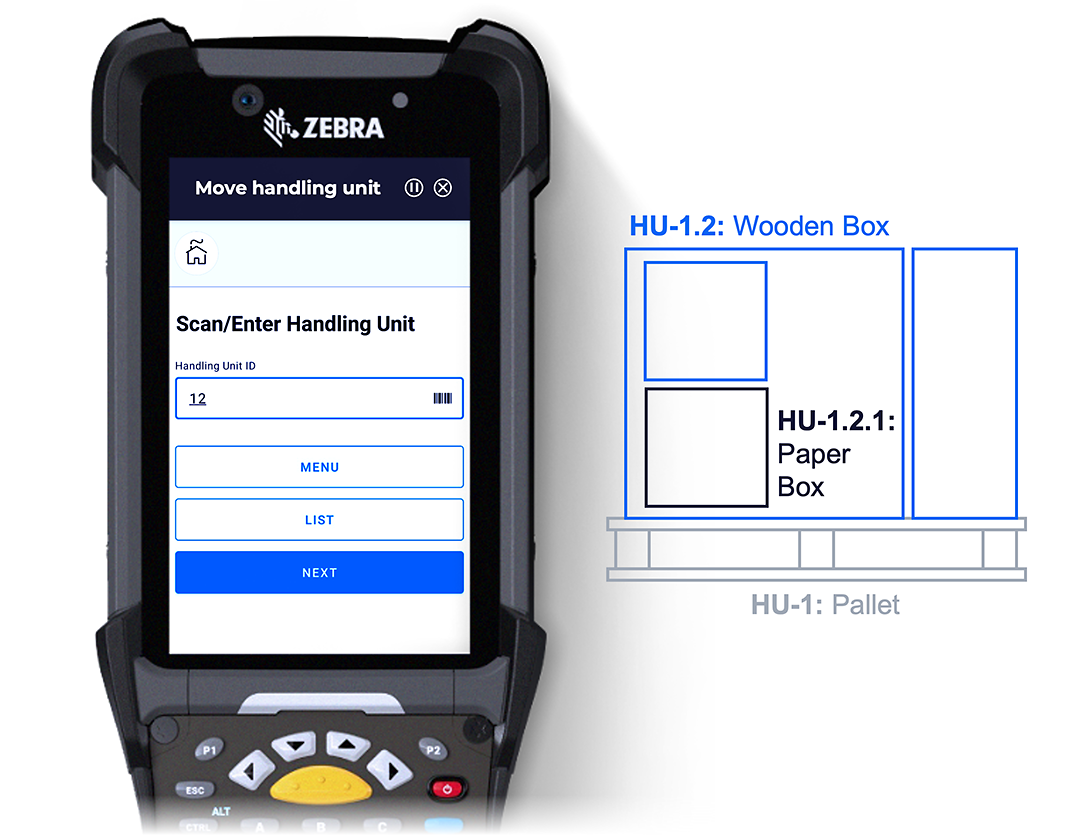
Use handling units
Our solution uses a flexible mechanism to organize materials, components and parts stored in packages. Users can define a whole hierarchy of packages (called "handling units") – where the smaller package can be stored in a bigger package, and this can be stored on a pallet. And so on... These handling units can then be used to easily move all embedded inventory goods from one location to another, to the shop floor, or to the shipment zone. Therefore, instead of moving single items, users move entire packages, which has a huge impact on warehouse operations efficiency. This approach is ideal for businesses seeking efficient and scalable logistics software solutions tailored to their needs.
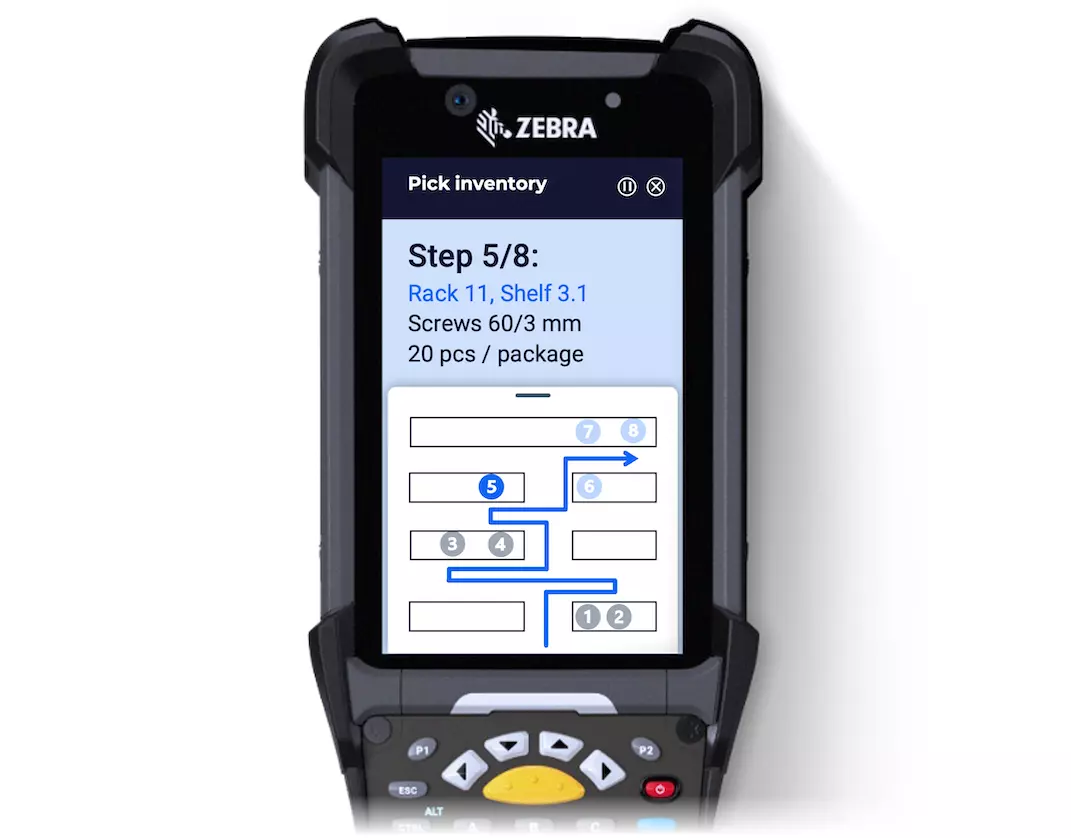
Optimize picking paths
Picking different materials and components for production might be complicated – warehouse operators have to gather different elements spread out across the entire inventory. And since they operate in a “JIT” environment, they are under time pressure.
Our solution optimizes the picking path based on the location, weight, further unloading sequence, or even expiration date of particular goods. This means that the warehouseman doesn’t have to go “back and forth” to complete the picking list. As part of our customized logistics solutions, this feature enhances productivity and ensures smooth integration with distribution ERP solutions to support seamless production workflows, streamlining service delivery solutions.
Integrate with the inventory equipment (with iIoT)
Novacura WMS package (powered by Novacura Flow technology) can be integrated with iIoT machinery, equipment and other devices that operate in a warehouse. A typical example where this connectivity may be used is the integration with industrial scales. The weight information can be used to double-check the delivered package, to count materials that return from the shop floor (i.e. the length of the cable), or to verify the contents of the package prepared for shipment. This weight can be automatically read from the scale and the number of goods (or its size) can be then automatically determined.

Pick by voice system
Novacura WMS package can be integrated with the “pick-by-voice” technology. With that solution, the warehouseman can listen to the instructions in his headset, having free hands to perform physical operations (which has a huge impact on efficiency). Then, when the requested operation is completed, the warehouseman can confirm it using his natural voice (thanks to the microphone and voice recognition technology). This capability can also be used for inventory counting and reporting anomalies, making it an essential addition to ERP for logistics
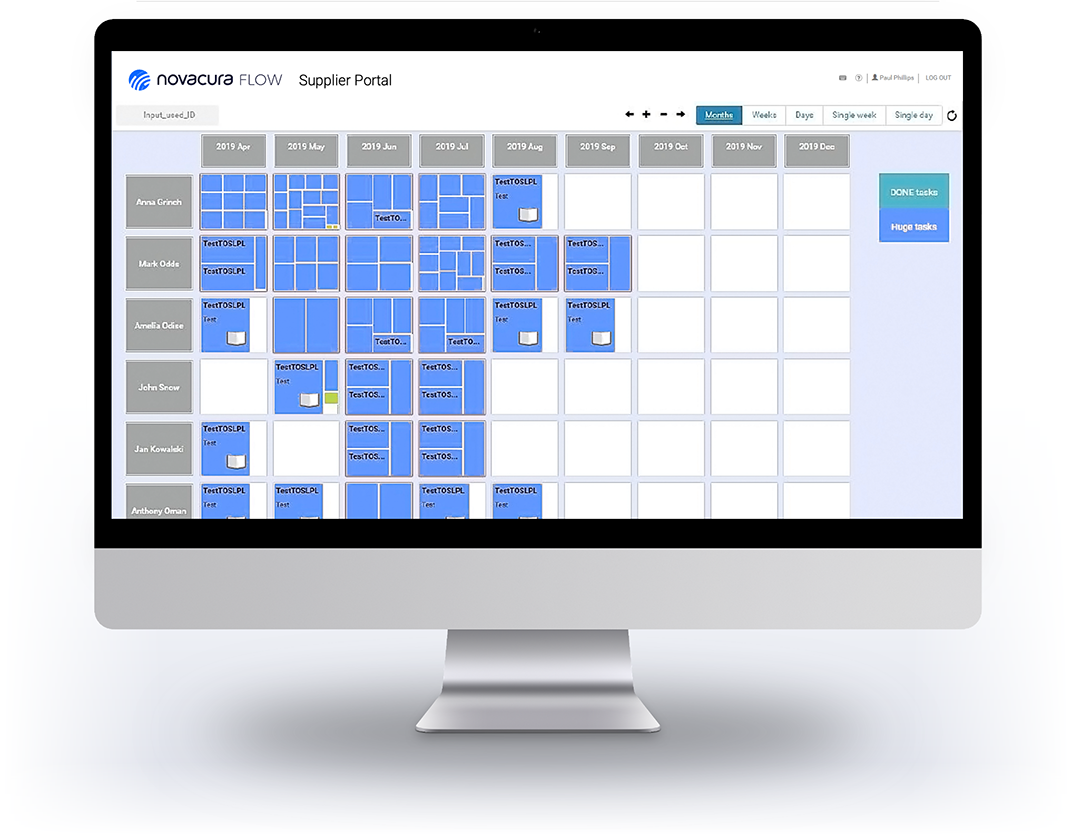
Manage your deliveries and shipments
Novacura WMS package is not only limited to supporting the core inventory operations. This logistics software offers support for supplies/delivery management and is used to manage the shipment of goods to customers.
You can use B2B Portal to confirm the delivery schedule with your suppliers and book a suitable time-slot and a free ramp for unloading! It can also be integrated with external transportation exchange systems (like PaceJet) and helps you find an optimal transport method for your shipment, making it a key part of complete delivery solutions.
Recognize your supplier’s codification
Typically, when delivery comes from a supplier, delivered goods are identified by codes according to the supplier’s codification system. These codes must be mapped on the internal coding system that is used within a company for all the goods. Our solution can support multiple codifications for the same goods and can automatically recognize foreign codes and map it onto internal codes.
Integrate with other departments
The ultimate benefit of using our WMS package is that this can be connected with other packages, that support other divisions in the company – quality inspection, production, procurement, maintenance and more. Thanks to that, a warehouseman can pick materials based on the material request issued by the production planning specialist that uses another element of the Novacura package. Or, broken components reported by the shop floor operator can immediately invoke additional internal transportation that will bring the correct components right to the work center.
Let us show you our complete package of applications dedicated to supporting logistics processes!
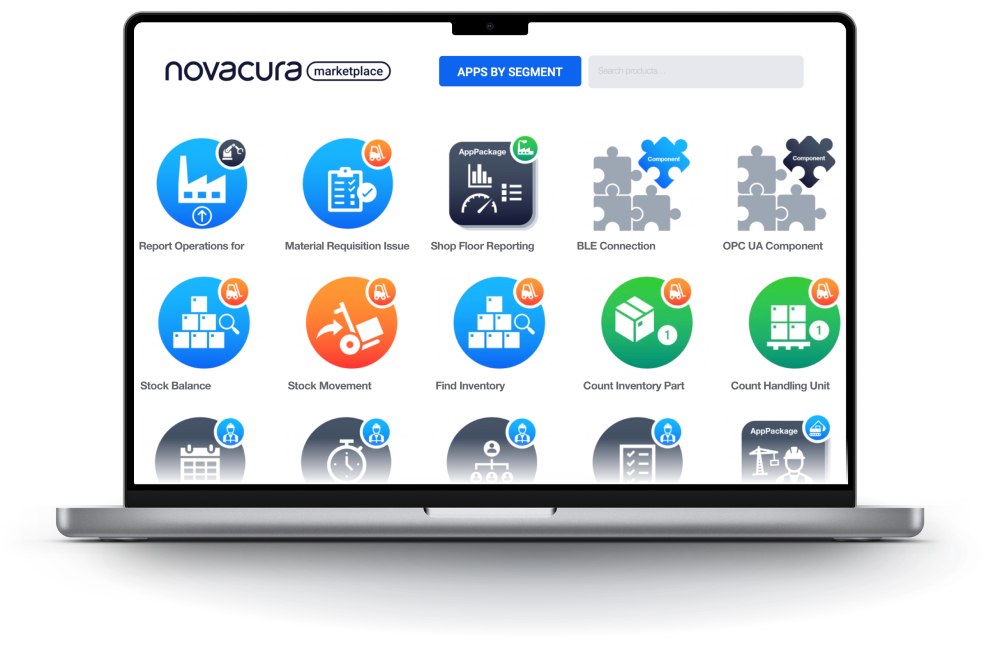
OUR CUSTOMERS:
“Thanks to this solution, warehouse workers have increased their efficiency by about 30 percent, and the error rate has dropped radically.”
Leif Repo
Group Logistics Manager
Specma AB
"I really like Novacura Flow because of its flexibility. From a software engineering perspective, the flow and processes can easily be visualized and modified."
Mario Bischofberger
Lean Manager Logistics
Maxon
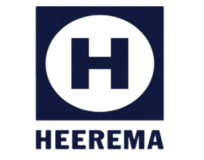
“Implementing Novacura Flow would save 250 working days, it means a saving of €80 000 per year."
Arjen Hoefkens
Solutions Manager
Heerema Group (HFG)
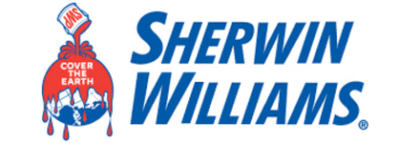
“Sherwin-Williams has advanced product flows, and creating a solution that included everything while still being simple and user-friendly was a real challenge."
Sabina Wenker
Manager Distribution Center
Sherwin-Williams
Key benefits:
01:
Custom warehouse management
Combine mobile apps, steered workflows, GPS and barcode scanning to create a warehouse that’s virtually foolproof. No more shipping errors, misplaced inventory or paper picking lists!
02:
Barcode scanning and RFID solutions
Code scanning is 10X faster and more accurate than manual input. Adding barcode scanning to your warehouse helps you fill orders faster and improve traceability too.
03:
Quality assured processes
Combine process management, process automation and QA best practices to deliver consistent, reliable services to your customers every time.
04:
Connected workflows
Combine data from your ERP, WMS and other business systems to manage your logistics processes, automate what you can, and optimize everything for peak efficiency.
05:
Customer self-service
Customers want transparency. With Novacura Flow, you can create a customer self-service portal that gives customers the info they want—on your terms.
Logistics management solutions and a detailed list of features:
Below we summarize the list of areas supported by Novacura WMS package:
01:
Suppliers / delivery management
- Dynamic stock level management
- Purchase orders management within B2B portal (EDI support)
- Delivery management solutions within B2B portal (JIT system support)
- Double-codification for goods delivered from suppliers - ability to use external labels / codes
- Financial settlements with suppliers within B2B portal
- Integrated carrier communication within B2B portal
02:
Internal logistics / production support
- Material requisition processing
- On-demand material delivery orders processing management
- Warehouse order picking optimization (picking paths optimization, strategies support FIFO, FEFO, LIFO)
- Transportation management for the shop floor (trolleys configuration & delivery route management and planning)
- External inventory usage optimization (delivery time transport duration, production returns management)
03:
Finished goods / shipment
- Finished goods storage
- Shipment planning process and confirmation with customers (B2B Portal)
- Transportation management system, planning (schedulling / adhoc – premium freight)
- Transportation preparation control and management (packing, loading, warehouse dock and ramp allocation)
- Transportation costs optimizations (route planning, post-analysis)
04:
Inventory management solutions
- Material and component storage
- Traceability solutions, batch / LOT identification on every stage
- Handling unit management
- Material movements (inside inventory/ cross-inventory)
- Inventory counting ("on the fly" cycle counting / periodical)
- Aging stock and scrap management
- Locations management (virtual locations, cross-inventory operations)
05:
Returnable packaging management
- Packages pool planning based on production demand
- Packages in a loop monitoring
- Package damage reporting
- Packages picking / packaging-sets completing from the shop floor
- Constant packaging quantity and quality control within B2B Portal
- Track & Trace back and forth packaging among distribution center, suppliers and customers
06:
Common technology support
- B2B Portals (connecting suppliers, customers)
- Deep ERP integration - dedicated to working with ERP systems as ERP extensions
- Machines and Data Integration (industrial IoT)
- EDI integration process & solutions
- RFID gates & data integration
- Barcodes / QR Codes support
- Pick-by-voice technology support
- Computer vision (solution for visual inspections, truck plates recognition, documents processing)
THE Simplified Implementation PROCESS:
The implementation process of custom logistics software takes less time than usual. We have a flexible solution that can be easily integrated with existing systems.
No risks thanks to PoC
We know, that the implementation of a new software solution is always risky. To reduce this risk, we put a lot of attention into the demo stage. We offer PoC (Proof Of Concept) phase, when customer can test the solution in the real environment.
Mature methodology & Industry expertise
We have a mature implementation methodology divided into clear stages (like initial requirements workshop, feasibility study, etc.), that gives project predictability.
We also have 17+ years of experience in manufacturing & logistics. This helps us identify real needs and propose adequate solutions.
Easy for the customer
We know, that software implementation project is not a regular activity for our customers. Therefore we help them plan the project, verbalize and prioritize requirements, choose the best elements, prepare tests, and go live. Moreover, our solutions are deeply integrated with popular ERP systems (out-of-the box), so we eliminate one of the biggest problems!
With ability to change. Anytime!
Our solutions are based on a low-code platform – so we can implement everything our customer wants, and every element can be adjusted to specific customers’ needs. Any requirements omitted in the planning phase can be easily met later, during the implementation, tests phase, or after "go-live"!
FLEXIBLE TECHNOLOGY BEHIND OUR logistics software:
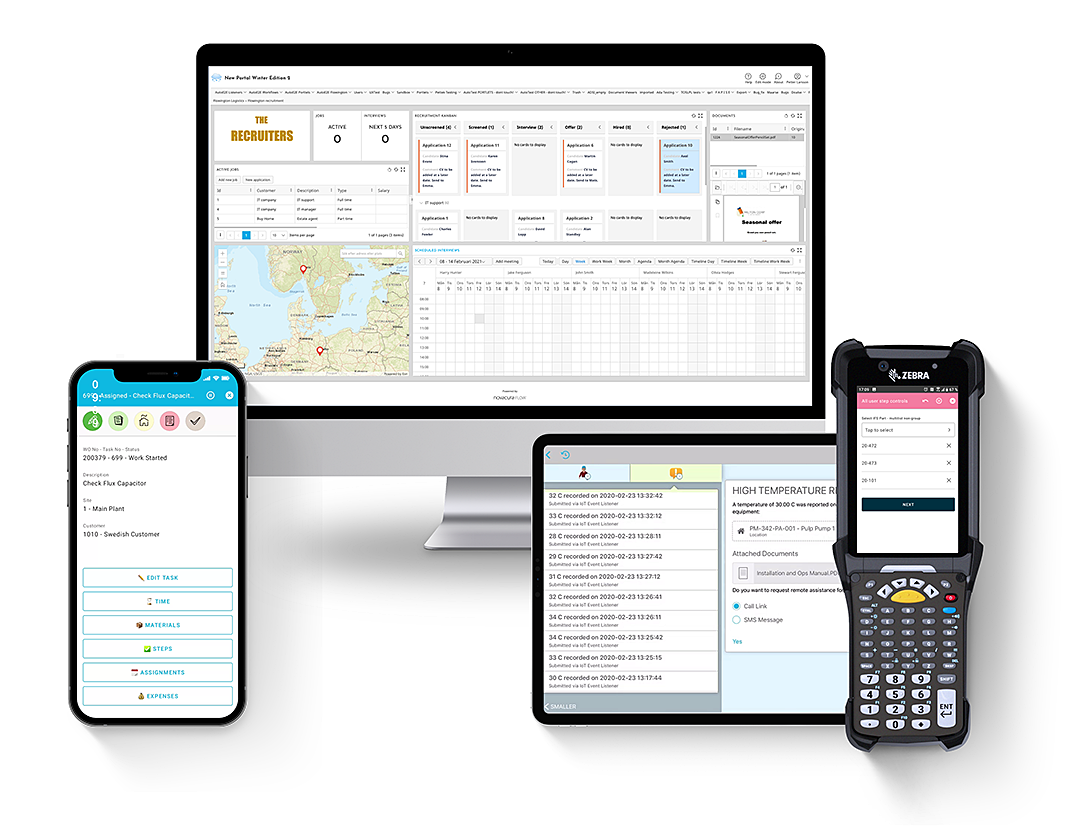
An interface optimized for thousands of operations daily
Our applications run on a sophisticated software platform – Novacura Flow. One of the key foundations of this platform is to run on every device – from barcode scanners, via mobile phones and tablets, to desktop workstations equipped with large screens.
But we are not just another SaaS software that offers that. We have optimized our user interface for users that work on a shop floor, in a warehouse, or in the field. We know that every “click” matters for these people because they run 1000+ operations a day!
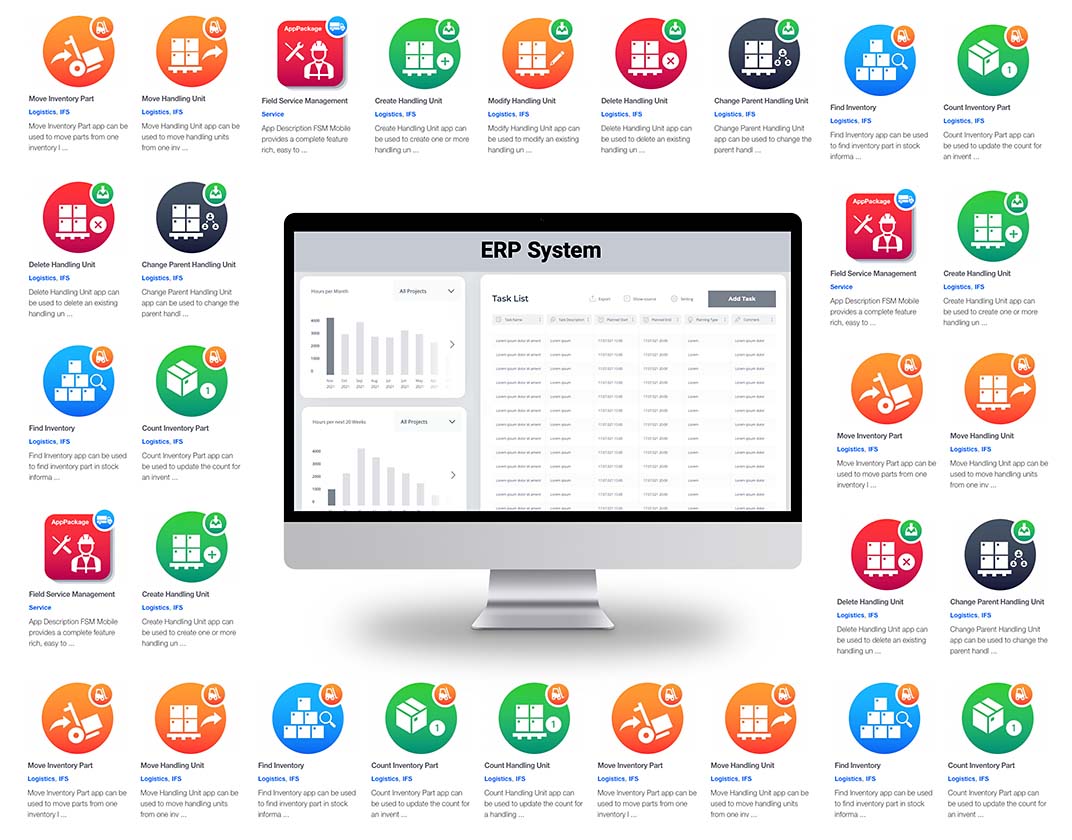
ERP extensions that are fast to implement
Our Novacura Logistics Software is built on a strong foundation: it must be easy and fast to implement! We created it as a package of ERP extensions that are dedicated to working with the most popular ERPs (such as IFS, Infor, SAP). With that approach, you can turn them on and start using them. The ERP system integration (that is usually the most complicated part) is prepared “out-of-the-box”.
The true advantage of this approach is that it doesn’t disrupt existing ERP processes. Warehouse operations performed in Novacura are fully visible in the ERP, ensuring all users retain the same access and transparency. This makes it an ideal solution for businesses looking to enhance their distribution ERP software with robust, user-friendly logistics capabilities.
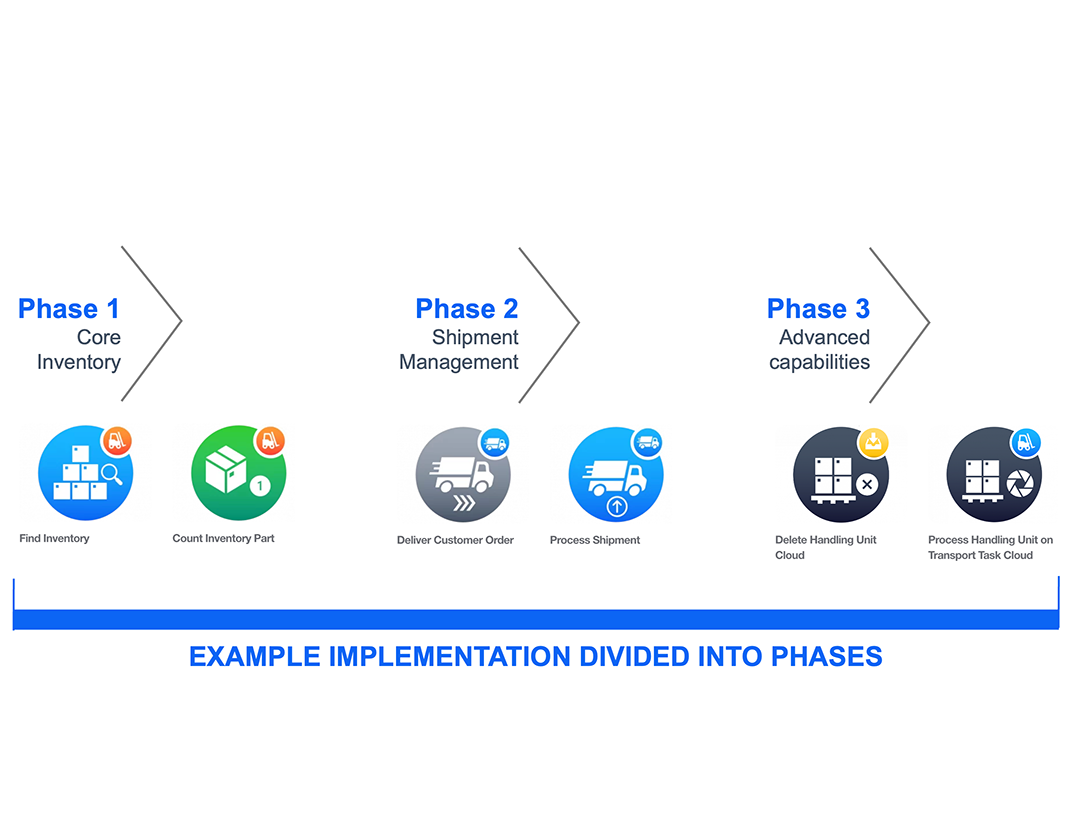
An iterative approach, no revolution needed
Novacura Logistics Software offers various applications to support and optimize warehouse operations. As these apps are prepared as ERP extensions, they share the same source of information: the ERP database. As a result, you don’t have to implement all of them at once. If you don’t want to implement some applications in the 1st phase, the standard ERP functionality will still be used instead of them. So you can add them later when the first package of process changes is adopted by your organization.
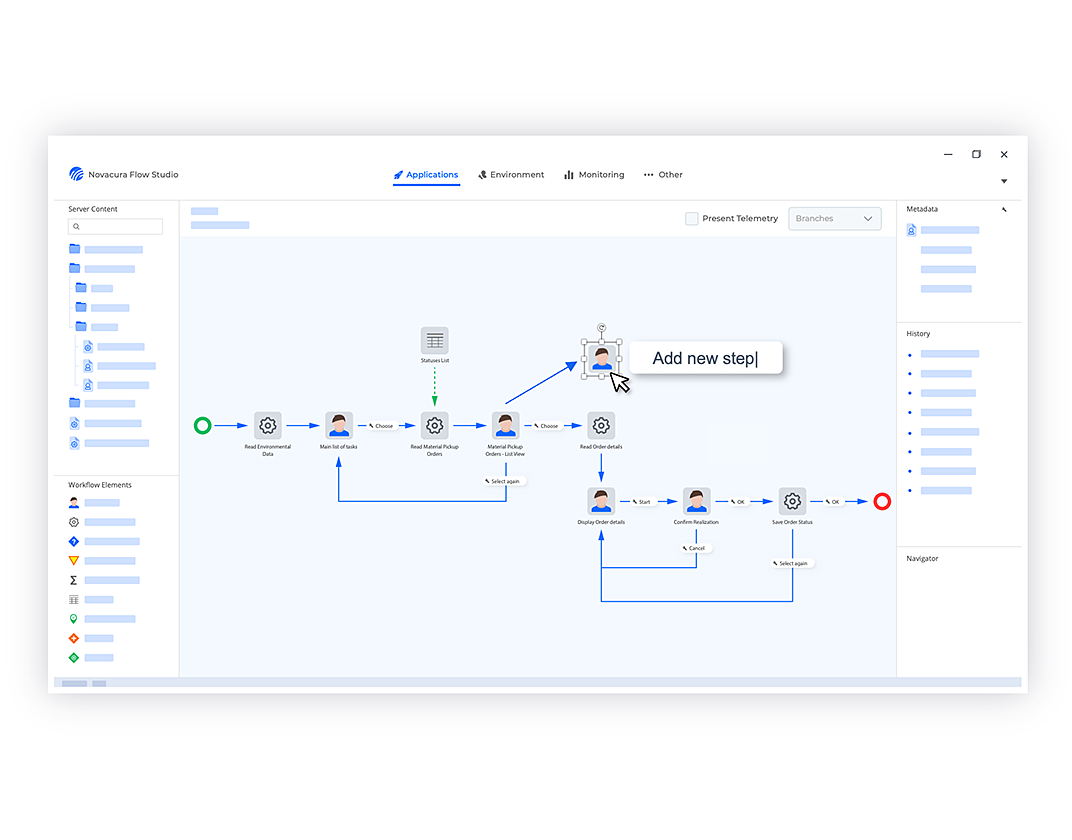
Ready for future changes thanks to the low-code core!
Every company is different from the others. You might have specific processes and require unique features, and we are ready for that! Our Logistics Software is based on the low-code platform Novacura Flow. It means that all our applications are not hard-coded. Our customers can modify them or clone them and create variants. And they can build their own applications. And thanks to the low-code engine, they can create apps by drawing them like they draw a business process. These low-code solutions for logistics empower our clients to quickly adapt and scale their logistics operations.
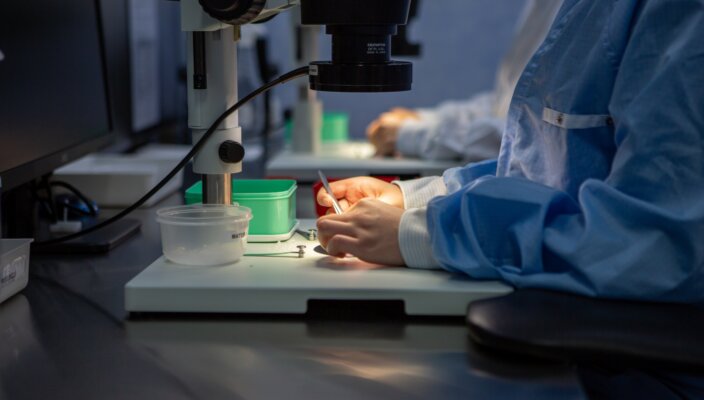
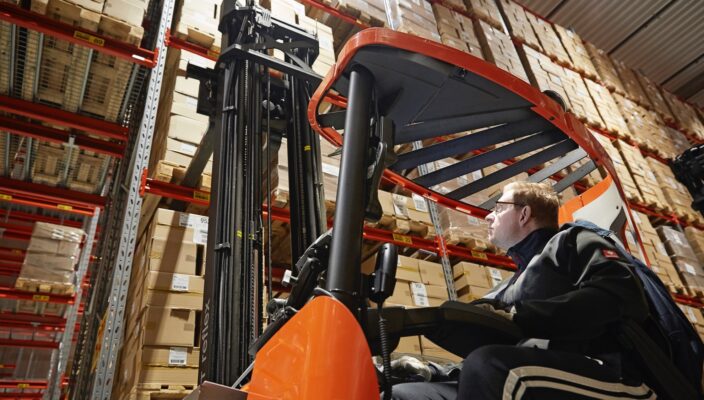
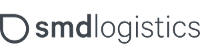
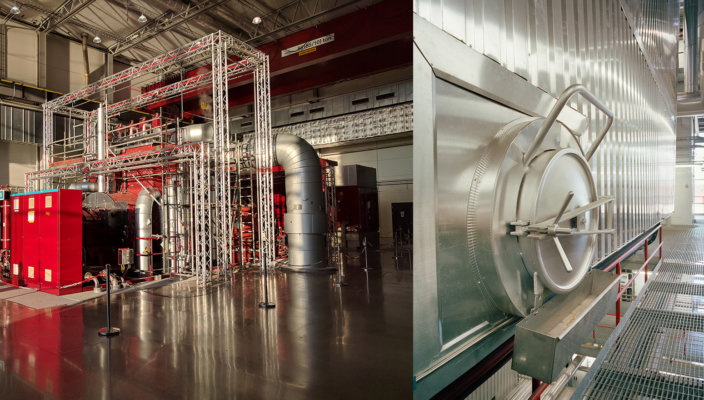
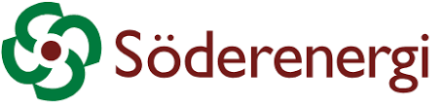
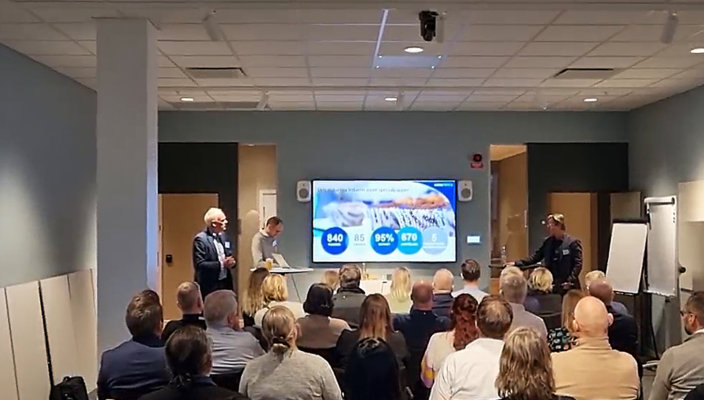

CONTACT OUR EXPERT:
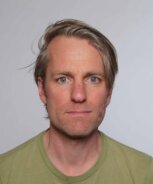