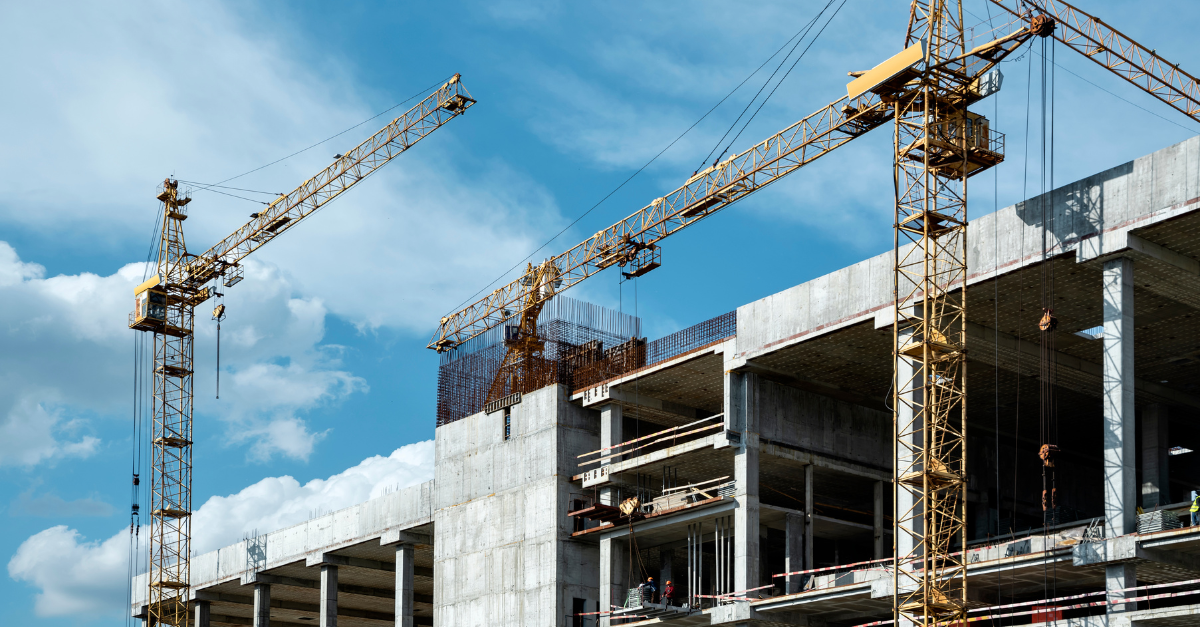
Jensen Precast optimized its proof-of-delivery process and enabled data-driven decisions with the automation of truck scheduling dispatch, product delivery, and mobile accessibility for drivers.
Over 50 years ago, Jensen Precast started as a one-person operation and has since grown into one of the largest independently owned precast concrete companies in the United States. As the company expanded in size and reputation, so did its desire to maximize operational efficiency. One of the first areas, Jensen Precast was looking to overcome was the ability to dispatch and gather proof-of-delivery documentation through a mobile application.
What took our team three weeks to develop in-house only took 45 minutes with Novacura Flow.
Challenges:
- Paper-based delivery process
- Manual data entry
- Limited visibility of orders and trucks
- Lack of responsiveness in prior system
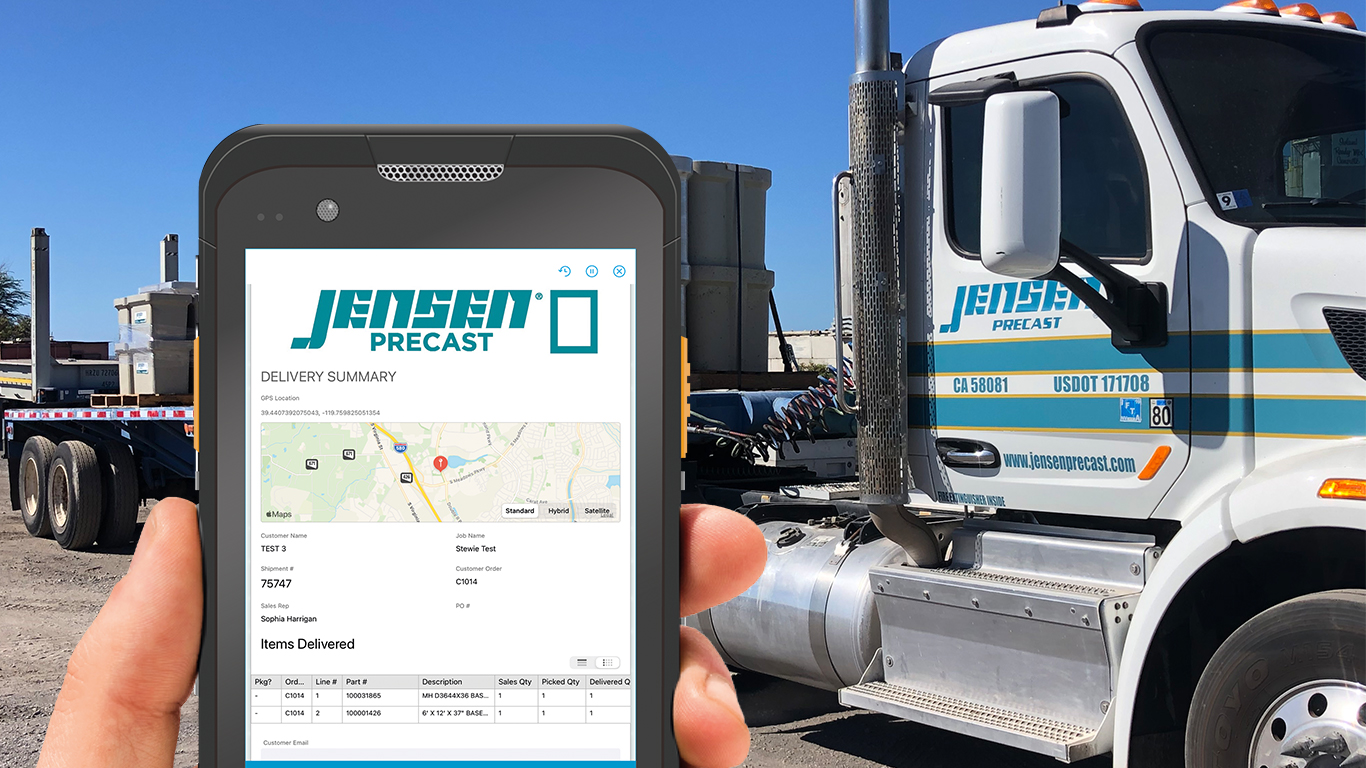
Precast concrete can be expensive to manufacture and ship, and Jensen Precast knew profitability was dependent on making the dispatch and delivery process as efficient as possible.
The delivery method at Jensen Precast was mostly paper-based, which caused inefficiencies and impacted productivity. For each product delivered, three separate documents need to be completed, signed, and returned. The stack of papers then had to be manually entered into their ERP system, IFS Cloud, which was time-consuming, error-prone and delayed invoicing.
Jensen Precast was also using a home-grown delivery solution, but it was not user-friendly and lagged in responsiveness. Dispatchers often had to make decisions with incomplete information, which led to errors and inefficient scheduling of trucks. Due to the unique nature of its business, Jensen Precast knew that regardless of the solution selected to expedite delivery processes, the company needed the ability to customize.
Solution:
- Automation of paper-based processes
- Mobile accessibility for drivers
- Real-time visibility of orders and trucks
- Integration to IFS Cloud
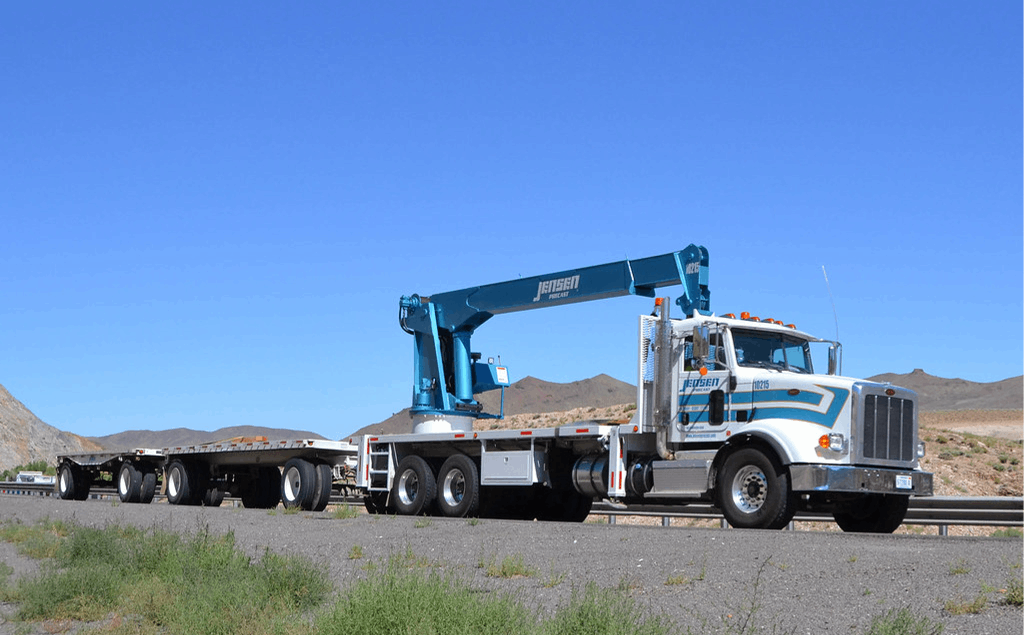
Jensen Precast evaluated whether to build a 100% custom app in-house or use a low-code development platform to make its dispatch and delivery method more efficient.
To get an apples-to-apples comparison, we came up with an app concept to test. What took our team three weeks to develop in-house only took 45 minutes with Novacura Flow’s IFS connector, and that’s when I knew it was the right solution for us.
Once Novacura was selected, the first step was to map out the entire proof-of-delivery process and determine what processes could be automated. Jensen Precast quickly got up to speed on Novacura Flow and built out a mobile application that its drivers would use to show proof-of-delivery.
Novacura’s knowledge of IFS has been a tremendous benefit, and since everything is developed using the same language, issues are easier to resolve (...)
Since Novacura Flow worked seamlessly with IFS Cloud and had drag-and-drop functionality, it made it easy for even non-technical employees to learn.
Results:
- Improved insight of orders and trucks
- Achieved real-time data entry at the time of delivery
- Optimized delivery routes with GPS tracking
- Improved dispute resolution with more accurate insight
- Enhanced the customer experience
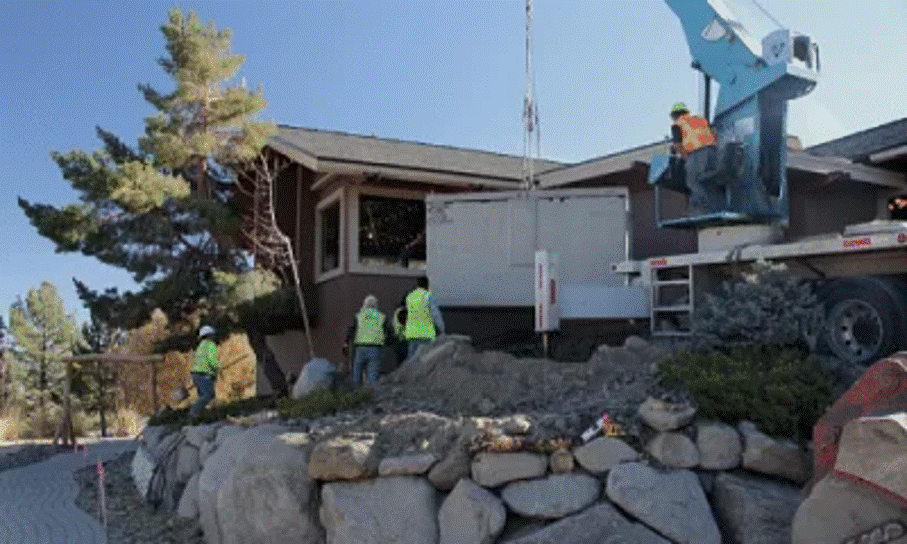
With the new app in hand, drivers had all the information they needed to show proof-of-delivery. An easy step-by-step interface walked them through the entire process and provided immediate access to shipment details directly from IFS Cloud.
The shipment receiver could sign for the order electronically, download a PDF on the spot and a picture of the shipment could be attached to the order to show proof-of-delivery. All the information was collected and synced to IFS Cloud in real-time.
Jensen Precast also streamlined its dispatch process leveraging Novacura Flow’s Portal. With Portal, dispatchers could see orders in IFS Cloud and any available trucks in real-time, making it easier to schedule deliveries.
Once the proof-of-delivery app was deployed, Jensen Precast saw massive time savings in data entry and dispute resolution. Orders that used to take hours to input now were updated in IFS Cloud in real-time and included all associated proof-of-delivery documentation. Dispatchers also gained improved insight into orders that were ready for delivery.
Jensen Precast has already developed more than 100 workflows and 7 portals for IFS Applications using the Novacura Flow low-code development platform.
Some of the apps we have developed so far have helped to streamline our Vault to IFS Part Creation, shop floor reporting, report picking, and employee onboarding. We are also looking to use Novacura Flow as an integration engine to integrate IFS Cloud with Salesforce and Apttus so that our sales team will have an up-to-date view of parts inventory.
We can’t wait to see what they build next with Novacura Flow!
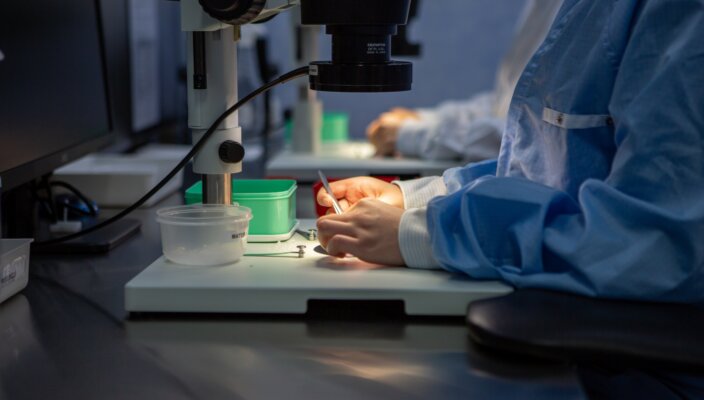
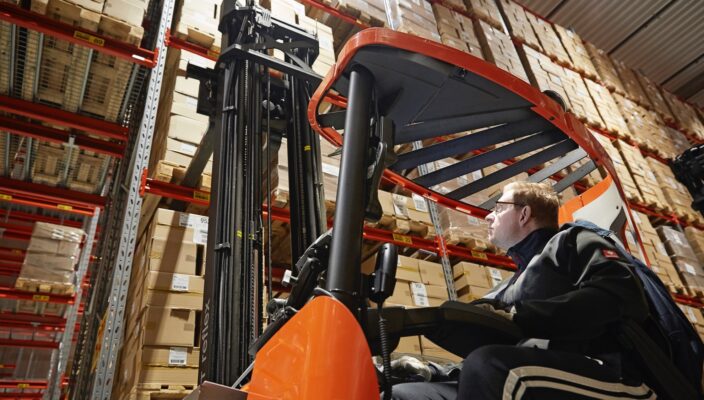
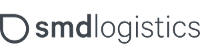
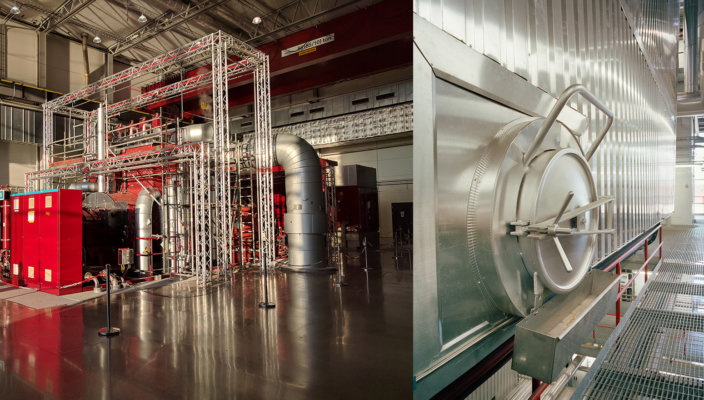
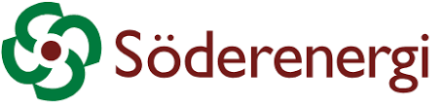
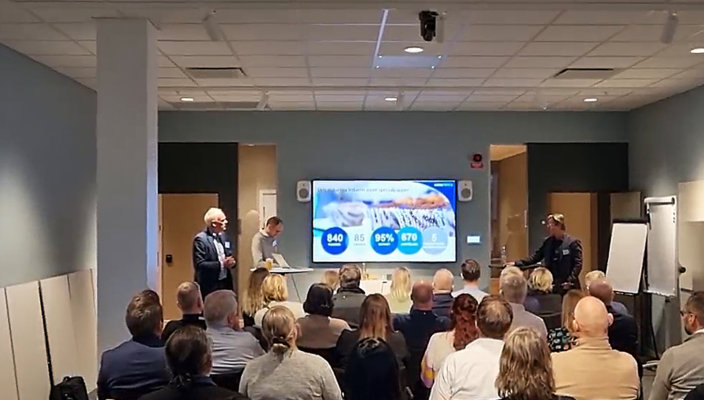
