Why should CMMS be integrated?
“Is it worth it?” is one of the fundamental questions that should be asked before any business decision. It is no different when it comes to integrating enterprise systems. When talking about manufacturing automation, integration should not be overlooked. But what are the benefits, risks and finally – is it worth it?
Computerized Maintenance Management System (CMMS) are intended to coordinate all maintenance activities, thanks to which production is continuous. This approach requires the coordination of the work of many departments. The CMMS needs to be informed quickly of any update from which it will recommend or make decisions.
The overall value that CMMS system can bring and all investments spent on its implementation might be ruined, if CMMS doesn’t operate on accurate and updated information. A good example is the planning module of the CMMS system, which – if implemented correctly – might have a huge positive impact on downtime optimization in production. But maintenance plan prepared in CMMS will simply be incorrect if it is based on incorrect or outdated data (and this is usually the result of manual data rewriting between systems). As a consequence, the prepared plan will not utilize natural breaks in production for maintenance activities, or the company can order additional spare parts that are already in the company’s possession but have not yet been in the evidence possessed by the CMMS system.
Inefficient business process solution
Through integrations, data can be shared and exchanged between different software applications directly and without delays, to better understand your business processes. And no doubt – the most important system to integrate CMMS with is the ERP system.
Moreover, all systems should see the same production infrastructure objects and the same resources and therefore, the company will be able to track all operations related to the same objects in different areas and systems (financial perspective, maintenance perspective, utilization in production, etc.).
We’re technologically ready to do the integration and the cost of such an investment is worthwhile. Automation, precision and efficiency in data propagation are some of the major reasons why modern companies integrate CMMS. Integration of software is a key for streamlining business processes, simplifying data analysis and reporting. Also, it will contribute to higher profitability and growth.
Efficient business process solution
Where is the master information in CMMS or in ERP?
Before we consider different integration scenarios between CMMS and ERP system (what data should be transferred? should it be sent or received?) we should firstly decide on where the master (primary) information resides. Multiple objects and transactions related to maintenance will be stored and processed in both systems (like physical assets, maintenance expenses, etc.). So before planning the integration, we should decide on where is the primary copy for that data and in which system should we process these data. As a consequence of that decision, we will be able to plan the data exchange direction (from CMMS or to CMMS) for particular objects.
There is no one and right scenario of selecting where to put master information and where to handle related processing. It depends on such factors as “how complex is your CMMS system”, “what maintenance support offers your ERP system”, “who is responsible for CMMS / ERP” etc. Hence, we only present some general suggestions on what should be considered when designing a master information source.
Purchases of consumables and spare parts.
Purchases can be initiated automatically when the stock level drops below the minimum – this strategy can be supported by ERP or CMMS, it seems optimal for the selected goods to be done by CMMS because it has access to more information and will be able to order purchases more precisely.
Asset management.
Plan machine inspections, marking the expiry dates of technical certificates, etc. – modules of this type appear in ERP and are the domain of CMMS; often CMMSs are more advanced in this matter, so it makes sense to delegate all such activities to them for the objects they manage, rather than dividing them between two systems.
Registration of service technicians' working time.
Some CMMS offer it, although billing takes place in ERP anyway – so you can leave these tasks only in ERP or transfer some of them to CMMS, which will result in the need for additional integration.
Settlement of the total cost of repairs (materials, time, subcontractors).
It is difficult to find directions here – can be managed by CMMS, and ERP will only receive its summary and implemented directly in ERP, without involving CMMS in that process.
Purchasing processes in the field of materials and services.
CMMS can initiate them automatically or only display a list of needs, and the order on this basis will be handled independently in ERP.
Remember, however, that these are general guidelines, and the final decisions should also depend on how well the company has developed standards for the use of ERP, whether it is ready to depart from them, and what the scale of the activities is.
Undoubtedly, all registers (master data, dictionaries, lists of objects, records databases, etc.) should be stored in ERP, downloaded by CMMS and it should operate on them in a manner consistent with ERP. In addition, it is necessary to ensure that all changes in the state of objects through CMMS are documented in the ERP system (the handling of data entry itself can be performed by CMMS, as long as it immediately sends the data to the ERP).
As a part of this analysis, we also recommend defining the routines in case of some data integrity conflicts occur – for particular objects, we should decide if the information from CMMS is master or should be overwritten by information from ERP.
What to integrate?
What data do you need to remember during integration? What should be transferred to CMMS and what should be left in ERP? This is again a very individual matter. We decided to propose a list of areas that need to be considered. However, it is worth remembering that we have not included production planning here, often carried out by additional systems, which should also be related to the CMMS.
Data sent from ERP to CMMS:
- dictionaries and basic data, including, for example, a dictionary of “types of service orders”, a dictionary of “operations and service activities” used in the settlement of order costs (per machine)
- list of assets to be maintained within CMMS, their types and hierarchy (preferably stored in ERP, although it can be extended in CMMS, e.g., by creating sets of the “production lines” type).
- list of employees, contractors, data on the availability of employees (L4, vacation)
- commodity indexes (parts, materials) and current stock levels.
Operations originally handled in CMMS, the results of which are transferred to ERP
- creating service orders (although order numbering is good to do in ERP and send to CMMS),
- settlement of working time, materials and parts used (per object) during a service order (collected in CMMS, sent to ERP),
- settlement of investment and renovation costs (as above),
- CMMS initiating orders for parts, materials, and subcontracting services in ERP,
- initiating reservations for parts and materials in ERP with CMMS, creating “advice notes” for warehouse releases for service orders in ERP
- updating documentation in ERP regarding certificates, inspection and acceptance protocols for objects managed in CMMS.
It will also be important to establish the integration cycle – while in some tangential points it is enough to do it periodically, the initiation of a purchase order or the booking of material under the order should be done online.
It should be remembered that strong integration of systems reduces the company's flexibility to changes. Therefore, you shouldn’t integrate all areas listed in this article and full integration is not always recommended.
Technology is not everything (a hidden problem)
Suppose we purchased a CMMS from a company that already has experience in integrating with our ERP, and the planned integration interfaces have been implemented and successfully tested.
Even if the integration from ERP to CMMS works automatically and immediately, it is the operational data in the ERP itself that must be up to date. Someone must enter this data into the ERP.
Today, handling of basic processes (orders, purchase approval, goods receipts) in many companies is carried out largely outside the system, with the use of paper or e-mails. For example, if the receipt of a delivery is first documented only on paper, then until the entire delivery is completed and mapped in ERP, no one knows its details. Even the best integrated CMMS in the field of inventory will not find out that urgently needed materials are already waiting on the ramp until such information is in the system.
An additional system will come to the rescue –The Low-code platform
The quality of data in the system and the smoothness of the processes related to their introduction are the keys to the success of CMMS integration with ERP. At the same time, modeling these processes is prone to changes and difficult to computerize. How to resolve this conflict?
Fortunately, modern solutions for process management – “Business Process Management Platforms” (BPM or BPMS) come to the rescue. On the other hand, establishing business processes between multiple systems increases the need for integration. Complex integration, that will connect different systems using different protocols. But again – solutions like “Integration platforms” might help here.
We know that the right implementation of the CMMS system equipped with all reasonable integrations and connected to business processes is a very complicated process. But we feel very confident to propose a unified solution that helps solve this problem. Our product – Novacura FLOW – the first low-code platform dedicated to production and logistics processes can play multiple roles.
You can run BPM processes between systems, establish all integrations, bring mobility to your paper-based business areas by implementing just one comprehensive low-code solution.
Our Low-code platform might control warehouse management, transport and production while communicating with popular ERP. It works natively on popular barcode readers and mobile devices and can also communicate with IoT devices. As a result, it has over 100 implementations in the production and warehouse area, where it successfully eliminates paper and brings mobility.
Conclusion
CMMS systems are very valuable tools that can realistically increase the efficiency of the entire production company. However, they will not be effective without proper integration with other systems in the company, especially ERP. Although it is a technical challenge that requires many business decisions, it is worth taking and planning them individually concerning the specifics of a specific company.
The weakest link in this chain is the data available in ERP. The benefits of integration will be commensurate with the timeliness of the information in the system. Therefore, the potential of the CMMS system can be fully used only if we think about the processes around and properly map them in the system. As a result, CMMS will receive relevant data on an ongoing basis, and its decisions will translate into real activities that we will be able to monitor.
And although the whole concept might look complicated from the technical perspective, the implementation doesn’t have to be painful because there are modern software solutions (like low-code platforms) that can overcome all challenges in one place. So – trying to answer the preliminary question: Yes – it’s worth it!

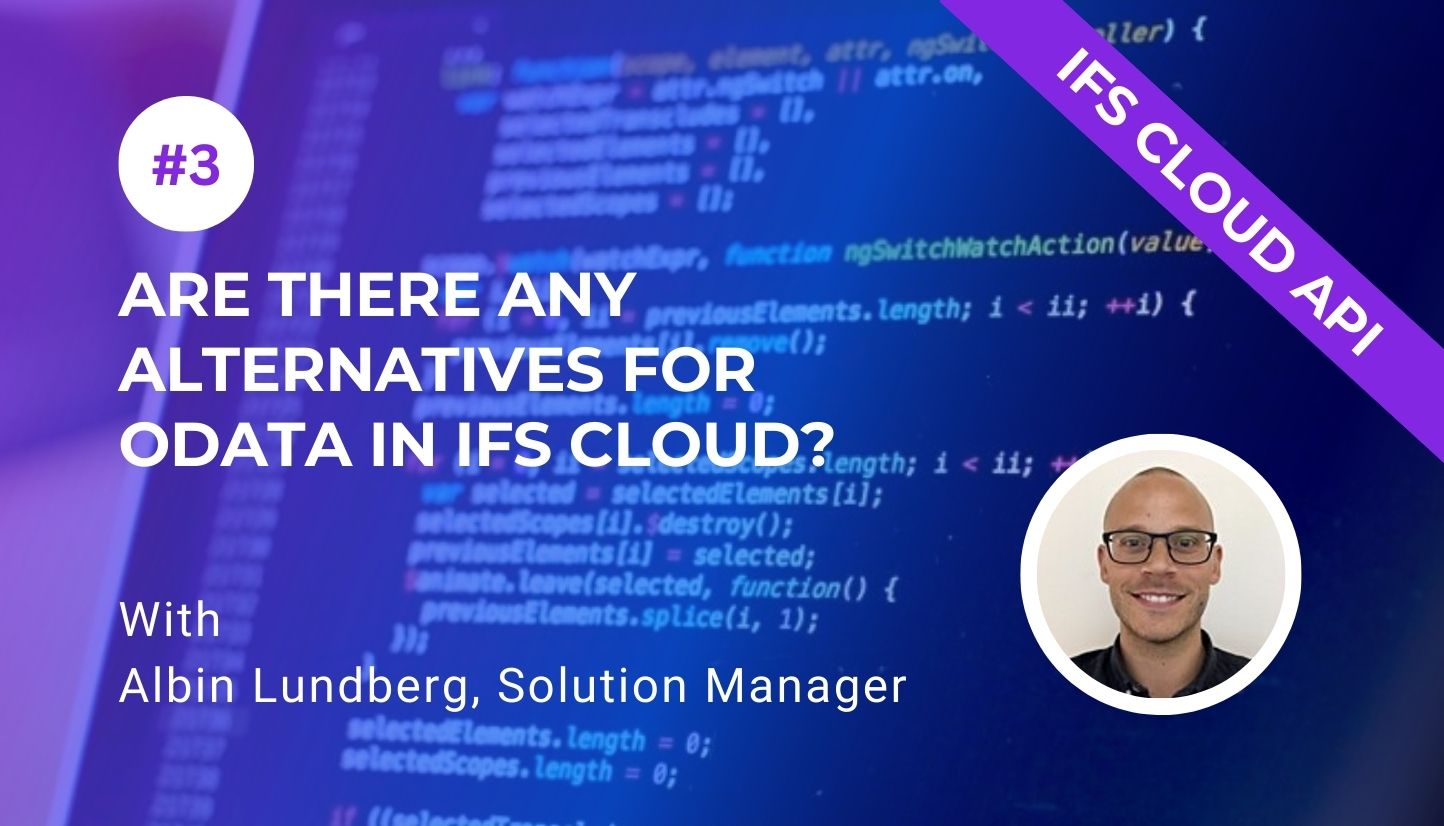

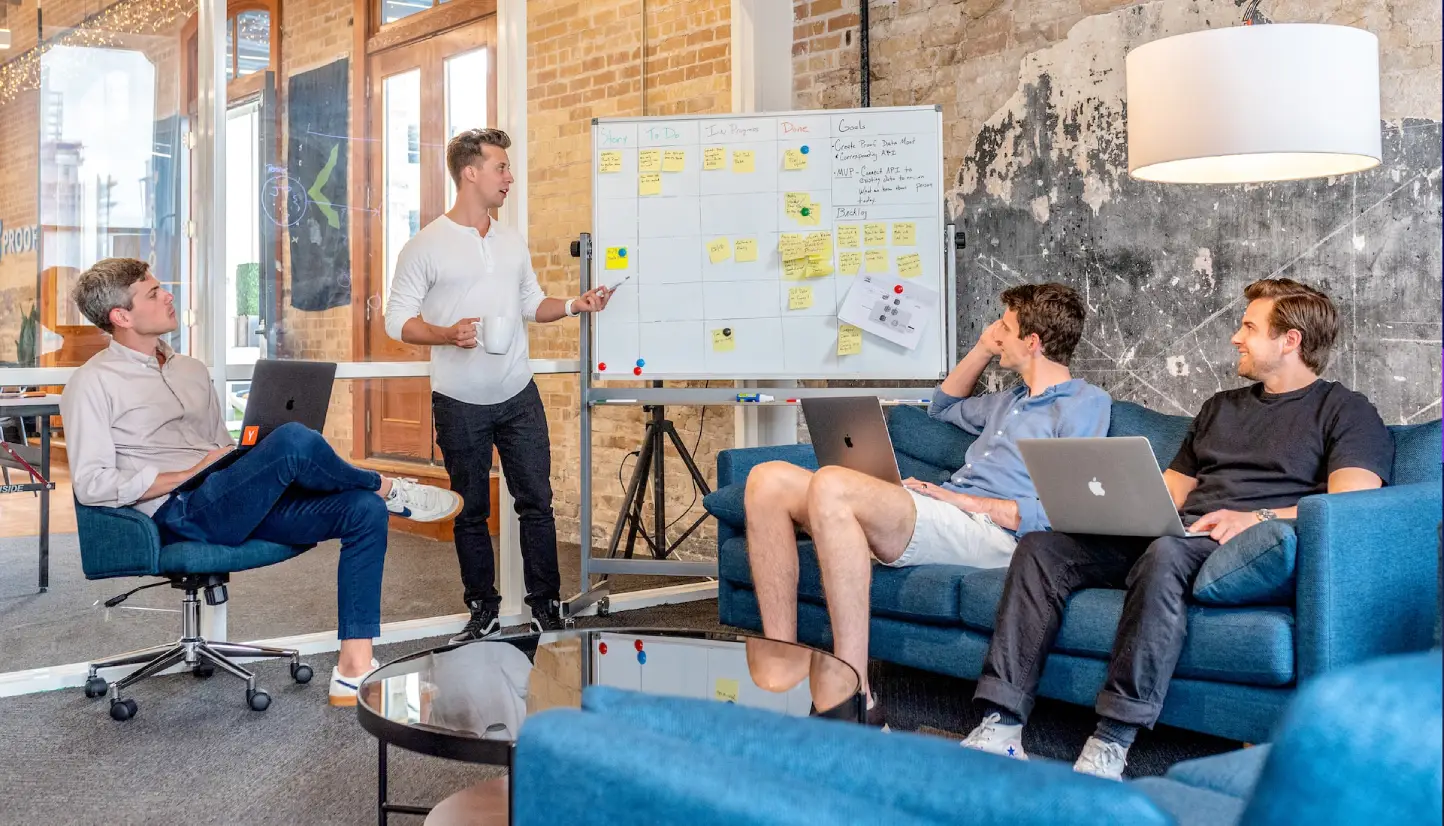
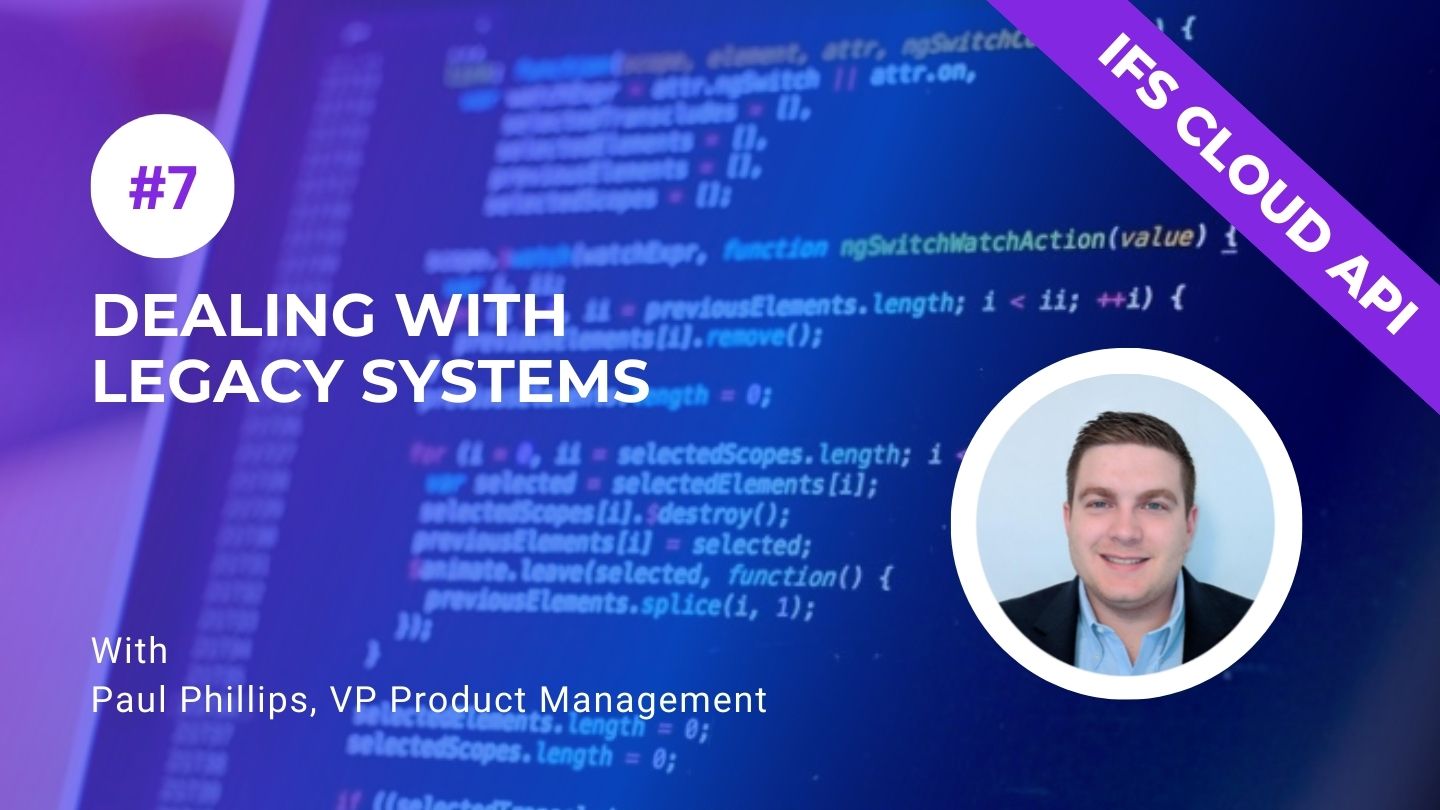
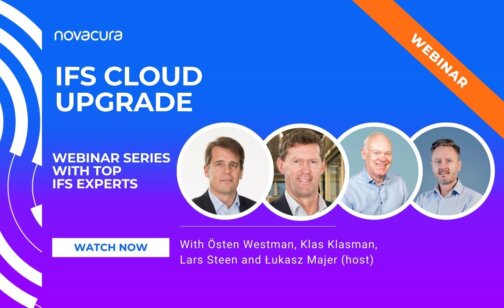