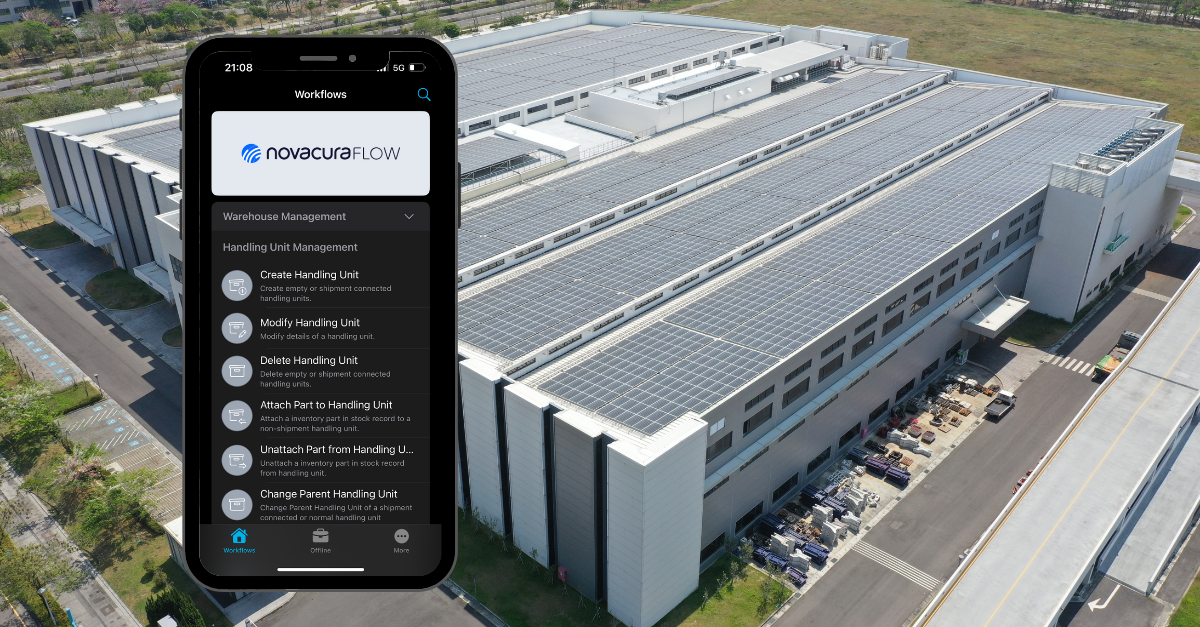
Efficiency in the warehouse relies on the proper functioning of an ERP system. Material handling and warehousing systems are crucial for expanding operational capacity and meeting the rigorous standards of global economies. Businesses should exercise caution when choosing an ERP system, considering key indicators in their final decision. The best ERP system should offer a warehouse information exchange system that ensures a seamless flow of data, simplifying information collection, processing, and presentation to users. Equally important is how the system handles decision-making and processes.
One of the market leaders in ERP systems is IFS, which provides essential core business functions capable of integrating all departments. IFS demonstrates heightened efficiency when paired with WMS functions within the ERP system. The primary benefits of augmenting ERP with WMS include:
- Labor: Minimizing manual operations through mobile solutions and enhanced staff management, offering a holistic view and control over productivity.
- Inventory and Inventory Costs: Reducing inventory discrepancies by improving manual operations related to allocation units, relocations, shipping, cycle counting, storage, and more.
IFS WMS
The most common approach to building a business case for a WMS involves evaluating a company’s current and future requirements. This assessment helps companies determine which WMS solutions are best suited for their warehouse operations. There are three primary types of system solutions that offer WMS functionality:
- Off-the-shelf (COTS) software: This type of software consists of pre-packaged, commercially available solutions designed to handle standard warehouse operations, such as receiving, a limited range of storage options, and shipping. These solutions typically offer no room for customization, and many tasks still need to be carried out manually.
- Enterprise resource planning (ERP) software: ERP software integrates various departments within an organization and often includes specific ERP components tailored to meet operational needs. These components are selected to cover the functionalities provided by COTS-WMS software.
- Custom-developed software: This software is custom-built to address specific operational requirements. It often includes tailored customizations to extend its functionality. However, subsequent upgrades can be costly and time-consuming, frequently requiring support from external programmers.
Standard Commercial Off-The-Shelf (COTS) software often falls short in providing extended functionality. Although ERP systems are pivotal in warehouse operations, they may encounter limitations in delivering comprehensive support for the evolving and dynamic needs of a growing business. Conversely, custom-built software might lack the capacity to address unforeseen warehouse challenges that may arise in the future. Each of these options comes with its own set of strengths and weaknesses, underscoring the importance for companies to carefully select the most suitable solution based on their unique operational requirements.
The cornerstone of the WMS software designed for IFS was predominantly WADACO, a solution enabling the integration of custom functions as an additional layer to an ERP system. However, numerous international warehouses chose to swiftly enhance their mobile capabilities within operations, presenting a considerable challenge. The task became particularly daunting as constructing a business case for a WMS primarily involved quantifying the financial advantages of digitizing the system.
While companies could pinpoint various financial expenses upon assessing their warehouse needs, they found themselves in need of assistance to evaluate the long-term financial benefits. This predicament underscored the necessity to develop solutions that could encompass specific features while remaining cost-effective.
One solution for companies facing this problem is to shift their focus toward business process improvement. This approach enables them to continually assess current expenses and identify weaknesses, allowing them to address these issues by implementing new WMS features. Companies seeking ongoing warehouse enhancement should explore WMS solutions that seamlessly integrate with ERP systems and permit the addition of new system features without the need for costly system modifications.
Why Choose IFS for Warehouse Management?
IFS offers a comprehensive, integrated ERP solution tailored for warehouse management, giving businesses access to a suite of tools that streamline inventory control, operational efficiency, and decision-making. Recognized as a leader in ERP and Field Service Management, IFS brings together multiple business functions within a single system, including dedicated applications for inventory, human resources, manufacturing, and customer experience.
Here’s how IFS stands out in warehouse management:
- Automated Data Collection: IFS streamlines productivity by automating data capture, reducing manual entry errors, and increasing reporting speed. This automation is essential for both high-volume distribution centers and lower-volume operations, such as spare parts management, ensuring accurate and efficient material handling.
- Intuitive User Interface: With its easy-to-learn, customizable interface, IFS simplifies training and helps reduce turnover-related costs. The system’s adaptability allows users to personalize which warehouse functions and data fields are displayed, making it easier for employees to perform tasks accurately and efficiently.
- Extensive Transaction Library: IFS offers a built-in library of configurable warehouse transactions to support essential processes like inventory counting, order arrival, and material issuance for production. This feature accelerates deployment and allows businesses to tailor warehouse transactions to their specific needs.
- Full Mobility: Supporting a wide range of devices, including mobile phones and laptops, IFS empowers staff with access to real-time data and warehouse functions from anywhere. This mobility optimizes workflow, enabling faster responses to changing demands.
- Global Support and Updates: As part of the IFS ecosystem, businesses benefit from worldwide support and access to future system updates, allowing seamless integration of new IFS features as they’re released. This robust support network ensures that IFS ERP adapts to evolving business needs, maximizing the return on investment.
Implementing IFS for warehouse management enables companies to enhance productivity, meet customer demands, and reduce costs as they scale. For companies looking to optimize their warehouse operations without extensive custom development, IFS offers a powerful, integrated solution that grows with their business.
Novacura WMS
The implementation of the IFS warehouse management system is highly effective when paired with Novacura’s solution, a longstanding business partner of IFS. Novacura presents the Novacura Flow software with WMS functionality, serving as a layer atop the ERP system and delivering the following features:
-
Total Mobility: Novacura Flow addresses all WMS-related business requirements through mobile applications, enhancing remote control within the organization. This eliminates the necessity for paper documentation, streamlines manual operations, and mitigates errors and inventory discrepancies.
-
Customized Features: Novacura Flow users can consistently expand existing features with new ones using a low-code platform. This allows the creation of new mobile and desktop apps without requiring extensive programming knowledge, enabling the swift deployment of solutions in a matter of hours (with new mobile apps taking as little as 3-4 hours to build).
-
Deep ERP Integration: Novacura Flow seamlessly integrates with IFS ERP and other renowned ERP systems in the market. Novacura provides over 50 connectors to support system integrations for diverse environments and meet advanced business requirements.
-
Modifications-Free ERP: IFS users can enhance their ERP system without making modifications. All operational changes can be implemented within the Novacura Flow layer, which is based on a low-code platform, facilitating easy implementation and business process management (BPM).
- Ready-made solutions: for warehouses that are unable to assess their current needs, Novacura has created its marketplace with ready-made solutions for WMS. Novacura provides the Warehouse app package, which includes over 100 ready-to-use mobile and desktop apps that can be deployed directly to the warehouse and connected to the ERP system.
- Easy training process: apps built on top of IFS are fully customizable with interfaces that can be tailored to the needs of individual employees. As a result, users see only the required options on their mobile device or desktop screen, reducing training time for employers who need to become more familiar with computers while eliminating errors in the process.
The example presented above explains how users can use Novacura Flow, with access to Novacura Flow Studio, environment for developing applications for internal operational needs in warehouses.
Summary
A typical WMS should provide four primary benefits within its capabilities:
- No information errors: reducing manual data entry errors.
- Decreased information lead times: decreasing the generation time of warehouse reports toward data entry.
- Increased productivity: remote access to the system across all departments.
- Increased warehouse capacity: reduced percentage buffer inventory and better inventory management.
Customer case
Learn more about WMS implementation from Novacura in an high-tech manufacturer in Switzerland, at MAXON company.

Novacura Flow offers its users these benefits through features that assist companies in assessing their long-term return on investment. With two decades of experience deploying our solutions across diverse industries, we have aided companies in expanding their warehouse capacity through Novacura Flow-based WMS features. Our solutions are entirely customizable and seamlessly integrate with IFS ERP. In addition to WMS capabilities, we offer IFS implementation services along with WMS capabilities. Reach out to us today and discover the possibilities for your company.