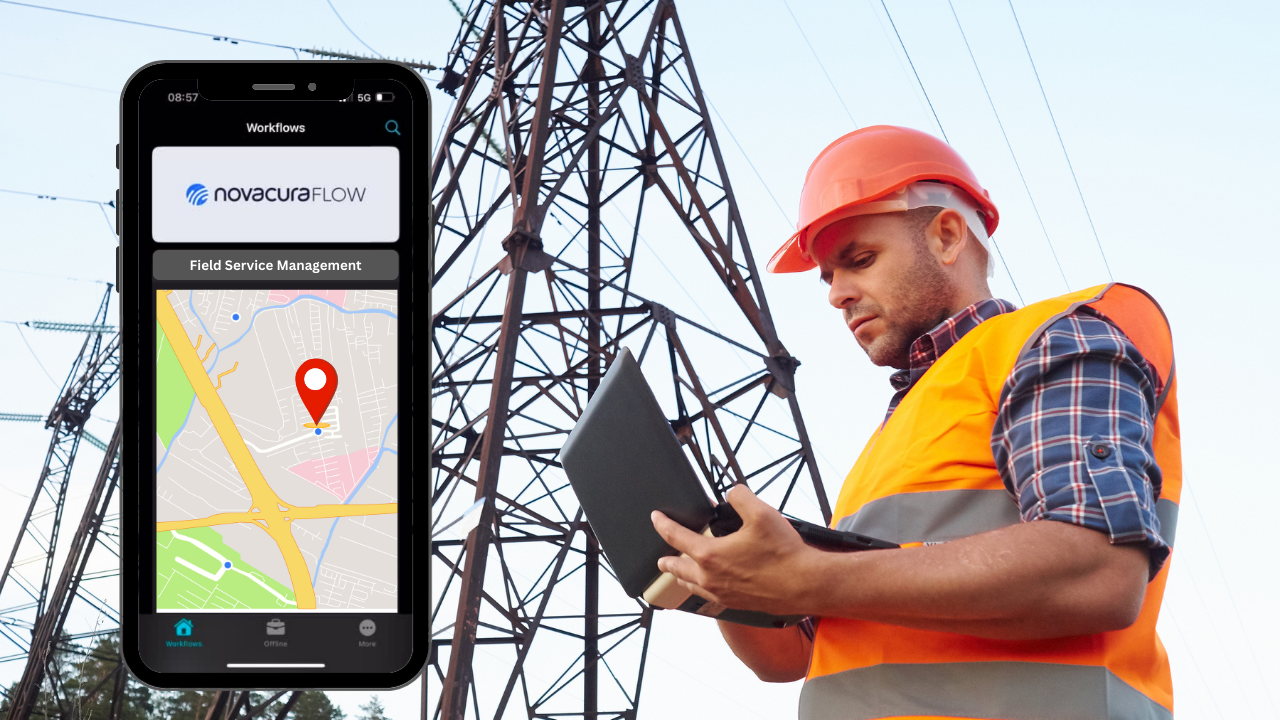
Maintenance and field services for equipment and all electromechanical systems are becoming a strategic tools in most industries, regardless of equipment and network extension complexity.
Monitoring the entire business system and networks provides operational dynamics analysis and supporting technologies to prevent unexpected events that can cause massive operational problems and unplanned downtime. Field services are needed to ensure the equipment’s ability to accurately determine the operating condition and isolate the root cause of possible aberrations.
Field services and maintenance are mainly applicable to industries that depend on equipment located in remote locations and local installations in their premises. These operations involve property management, which is very common in high-tech industries. Among these, we can point to telecommunications, the energy industry, construction, building maintenance, the railroad industry, various field services, and manufacturing. For all these industries, it is required to provide services that guarantee the standard functionality of equipment in different locations with mobile access to general services and maintenance systems, which includes warranty repairs, parts management, specific price assessment, personnel scheduling with the definition of working hours along with all the logistics processes involved (GPS scheduling, tracking, and tracing operations).
Companies that want to be most efficient in their cost evaluation and process optimization programs within complex service management should take appropriate precautions on preventive and corrective maintenance, as well as maintenance improvement within the autonomous work order.
What is IFS field service management?
Process optimization programs include equipment control systems that give a company the correct parameters to evaluate its service and maintenance requirements.
One of the Field Service Management systems has been introduced by IFS as a process monitoring and optimization program for organizations operating in the field service, high-tech, medical equipment, and telecommunications industries. The IFS Field Service Management software system provides its users with the following capabilities:
- Optimized planning and scheduling: resource modelling and planning with travel time, route optimization, and working hours.
- Field service management: work order management and performance management.
- Customer engagement: CRM capabilities within ERP portlets.
- Reverse logistics and warehouse repair: parts management that ensures parts flow back to the warehouse and OEM repair providers when required.
- Intelligent asset monitoring: monitoring technologies with service levels for tracking reparations of individual pieces of equipment.
IFS has been the leader of Gartner’s Magic Quadrant for Field Service Management 7 times, and for the last time in 2022.
What is an FSM solution from Novacura?
The IFS FSM solution has its base on IFS ERP. IFS FSM, despite its extended capabilities, is strictly characterized as an off-the-shelf solution. From this perspective, IFS FSM has limited mobile capabilities in terms of the available customizations that are required in various industries.
Novacura offers its fully customized mobile solution for field service management, combined with IFS ERP as a system layer on top of ERP. With this solution, companies using IFS ERP can enhance their capabilities with customized software that allows easy modifications directly by users. Novacura’s FSM solution was developed as part of Novacura Flow software based on a low-code platform.
The example presented above explains how users can use Novacura Flow, with access to Novacura Flow Studio, environment for developing applications for internal operational needs in warehouses.
The primary goal of the Novacura Flow FSM solution is to provide the best methods for comprehensive, continuous process improvement in domain services, consisting of the best methods from operations, maintenance, financial assessment, and process engineering to serve the well-being of companies in various industries. Novacura Flow provides these FSM capabilities:
- Organizing and scheduling: a system for organizing, directing, and scheduling that combines various planning functions such as working hours, estimating travel time to destinations, scheduling staff shifts, and more.
- Field service management: personnel supervision and work order management with broad functions regardless of application area.
- Customer outreach: customized system with an interface tailored to direct organization needs connected to the ERP system allowing for customer relationship management and more.
- Back-end logistics: scheduling that ensures that inventory resources, such as spare parts, are used efficiently and effectively and delivered by methods to the location and more.
- Real-time monitoring: a system that helps identify key elements in the maintenance process and pulls metrics from condition and performance monitoring.
Benefits of using Novacura Flow FSM solution
In many cases, maintenance and field services are required simply to avoid or reduce accidents and eliminate unexpected downtime. Novacura Flow offers efficient solutions within its FSM system that increase productivity and profits while enhancing service user satisfaction. Companies can determine the higher value of service through a mobile business process management model that includes the following benefits:
- Total mobility: mobile apps tailored to specific business needs and a suite of pre-built apps from the Novacura marketplace that allows to deploy of proven solutions in a matter of hours.
- Customization and flexibility: users of the Novacura Flow platform can create their structure for maintenance and field services, as well as create their mobile apps for different purposes, increasing productivity and user satisfaction.
- Deep ERP integration: Novacura Flow software can be connected to the IFS ERP system and integrated with all other known ERP systems and has its own solutions for connecting equipment and machines with IOT connectors or the most popular digital business solutions.
- Cost-effectiveness: mobile applications help use resources efficiently and can be freely modified whenever needed without additional processes such as SoW (Statement of Work) and external consultants’ involvement.
- No programming knowledge: Novacura Flow platform does not require users to have high programming skills and is entirely user-friendly, enabling employees to design and program business processes and shorten personnel training time.
Summary
Novacura is a long-time partner of IFS and a three-time winner of the annual IFS Channel Partner Award. We provide our solutions to existing IFS customers, helping them increase operations so they can function more optimally and efficiently when building mobility-supported maintenance and field service programs.
Customer case
Learn more about FSM implementation from Novacura in SweMaint, Northern Europe's leading company for repair and maintenance services.
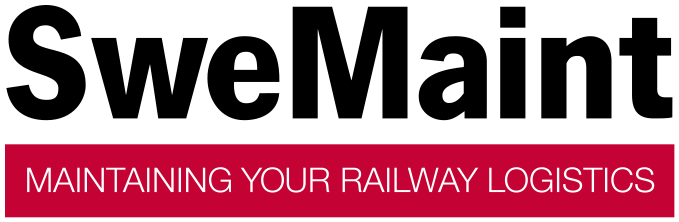
Novacura Flow users can meet a variety of functional requirements even despite its expanded complexity. We help companies reduce the problems associated with high-cost fluctuations in maintenance and support them in reaching significant return on investment (ROI). We offer IFS implementation services along with WMS capabilities. Contact us today and see what we can do for your business. Learn more about FSM from Novacura here.