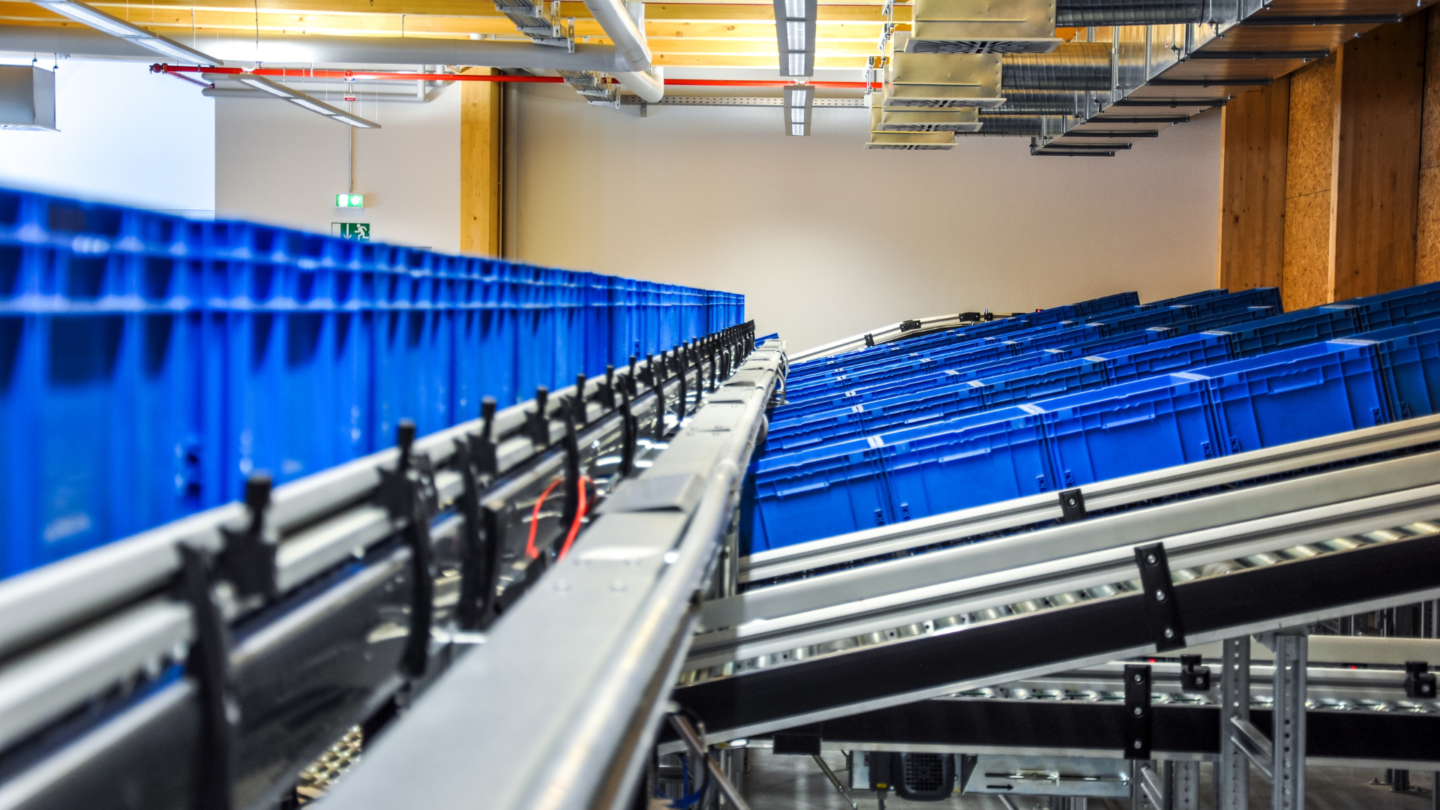
Inventory control over a long period of time can no longer rely on manual data entry using paper forms. The dependence on the manual data entry method cannot be verified in a short period of time and can cause inventory discrepancies that have serious financial implications for the organization. Traceability of goods in manufacturing requires digital inventory management software.
Production clerks equipped in mobile devices with embedded software can take control of the entire inventory management process. Handheld computers and mobile scanners operating with barcodes, QR codes, RFID technology are able to ensure proper supervision of the internal flow of materials. Providing barcode material labels when products are inbounded is the solution that should be implemented in any factory. There is no doubt that the use of mobile devices with embedded operate software in manufacturing can influence all stages of production and increase its quality of:
- Material consumption – consumption registering and preventing shortage of
raw materials. - Processing inbound – good traceability from dock registration to inventory
putaway process. - Order picking – accurate collection from direct stock locations.
- Packing and pelletizing – easy determining delivery destination and good quality order checks.
- Outbound and shipping management – efficient dispatch and reliable ETA with
track & trace. - Inventory control – quick inventory control and accurate cycle count.
What is manufacturing traceability?
Manufacturing traceability refers to the ability to monitor and track materials, parts, and products—whether individually, by batch, lot, or shipment—throughout the entire manufacturing process and into the supply chain. This capability has evolved significantly from the days of manual records and paper-based tracking. The introduction of barcode technology was transformative, enabling manufacturers to track any item associated with a barcode, including raw materials, components, subcomponents, and finished goods.
Modern manufacturing traceability systems go further by leveraging advanced tools like barcodes, RFID, and data analytics to provide real-time visibility into production processes, not just physical items. This comprehensive traceability begins the moment raw materials and parts enter production and continues until the final product exits the facility. By offering detailed insights into each stage of production, today’s systems help manufacturers ensure quality, boost efficiency, and maintain regulatory compliance, ultimately enhancing operational control and customer satisfaction.
Manufacturing in the COVID-19 era – Top 3 challenges and how to overcome them (PDF)
- Top 3 challenges for manufacturers during the pandemic
- What are the root causes of the challenges?
- Proposed solution
- How to implement iT
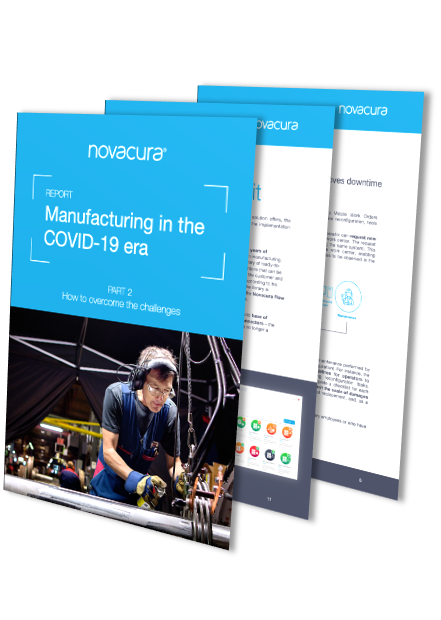
Effective traceability of materials
Embedded software connected to ERP systems can be enough to fulfil general needs of particular warehouse management but its customization is almost impossible. Modification of ERP system is difficult and time consuming therefore any sort of random software cannot be suitable for complexity of production process. The manufacturing industry is closely dependent on the dynamic changes occurring in each industry sector. Ongoing changes regarding market demand are forcing factories to respond. Adjusting production lines and Warehouse Management Systems (WMS) is already part of its strategy.
To secure effective material traceability, manufacturing facilities should consider selecting the most appropriate solution with the possibility of flexible software modification. The software should not only be suitable for the existing hardware, but in the first place, it should provide operations workers with the right control over inventory. Software used on mobile devices should be capable to:
- ERP connection – extracting and uploading to the warehouse servers data on all processes.
- Labels generating – interface with a printer to provide barcode labels for order picking, shipping, inventory classification, etc.
- QR & Barcode Reader – scan labels to identify inventory and share operation tasks
- Improve inventory management – provide a detailed overview of current stock levels, prioritize orders picking volumes, guide on suitable inventory replenishment (remove obsolete inventory, etc.)
- Improve order picking system – optimize employees movement between picking locations, prevent empty locations during order picking, streamline dispatch process and all system delivery transactions etc.
- User profiles and tasks – profiled user access to the system and synchronization of tasks and processes for different departments. Capability for tasks overhanded to forklift, combilift, reach truck and EPT drivers etc.
- Mobile interaction in real time – providing OPS employees with individualized work instructions (tasks changing, special demands) displayed on mobile devices.
- Flexibly adjustments and customization – should allow to easily add and remove an additional options if a new process or inventory is required.
Inventory management software should be able cover inventory management requirements in any configuration. Good software should provide mobile solutions integrated with required inventory processes and ERP system. A professional inventory traceability solution should have a tangible impact on reducing supply chain errors and increasing customer retention rates.
The benefits of manufacturing traceability
Manufacturing traceability brings numerous benefits by enhancing control, accuracy, and efficiency across the production process. Here’s a look at the main advantages of implementing robust traceability systems in manufacturing:
1. Robust Data Collection
Effective production traceability in manufacturing starts with gathering meaningful data that offers valuable insights, not just raw information. By attaching barcode labels or RFID tags to materials, parts, or products, manufacturers can capture details such as price, origin, certifications, tolerances, and handling instructions. These identifiers allow each item to be tracked throughout the production process, making it easy to locate parts, review workflow histories, and assess the impact of any adjustments in real time.
2. Powerful Analytics for Informed Decisions
Manufacturing tracking systems provide real-time data that can be analyzed using analytics software, enabling rapid, data-driven decision-making. This capability not only supports troubleshooting but also allows manufacturers to test preventive measures without disrupting production. Maintaining an accurate database of genealogical records further supports continuous improvement, offering insights from historical data that help optimize processes over time.
3. Improved Accuracy and Forecasting
The real-time data provided by automated traceability systems enhances forecasting accuracy across inventory, equipment, labor, and profitability metrics. It ensures precise tracking of product origins and locations, which can be essential for limiting liability and ensuring compliance. By replacing manual data collection with digital traceability, manufacturers benefit from more reliable, shareable data and consistent reporting, facilitating better collaboration and ensuring all teams work from a unified source of truth.
4. New Revenue Opportunities
Streamlined, agile manufacturing processes can become a competitive differentiator. Industrial traceability enables manufacturers to demonstrate efficiency, flexibility, and responsiveness, all of which are attractive to potential customers. Additionally, traceability systems with advanced analytics allow growing companies to test for scalability, adapt to process changes, and implement new equipment—all without disrupting current production, setting the stage for expansion and innovation.
5. Profitability Levers
Operational efficiency drives profitability, and traceability systems place numerous profit-enhancing levers at a company’s fingertips. From improved production efficiency to stricter quality control, traceability supports cost-saving measures across the board. It also minimizes the financial risks associated with noncompliance, theft, and recalls, allowing manufacturers to safeguard their bottom line while focusing on growth.
In summary, manufacturing traceability strengthens production control and supports a proactive approach to quality, compliance, and process improvement, making it an essential tool for modern manufacturing success.
Implementation of the raw material inventory management software
Dealing with internal challenges that occur during different processes without good software solutions isn’t possible these days. Modern warehouses with manufacturing or distribution processes should implement customized software to streamline the warehouse management system (WMS) and supply chain.
Novacura is a software development company that provides comprehensive solutions for all inventory management requirements, manufactures and supply chains. Core idea of our solution is about integrating our software with existing ERP systems. We provide modifiable software solutions that allow to create users customized applications for PC workstations, mobile devices needed for complex inventory management. Unlimited customization options allow to comprehensively meet all standard and new process and product requirements. Nonvacua software use IoT connectors to arrange connection between well-known ERP systems. In this way, customized applications are able to interact with internal network. In this way, customized applications are able to interact with and manage inventory data stored on internal servers.
Implementing Novacura software can expand inventory management capabilities to provide unique features:
- Improve system transactions displayed from existing ERP – customized applications from Novacura can convert existing ERP transactions and extend ERP system about new options and system transactions.
- IoT connectors – we have already prepared connectors to the most popular ERP systems (IFS Applications, Infor M3, IBM Maximo, SAP, Oracle and more).
- Ready to use solutions – we have created ready-to-use industry applications, that are suitable for logistics, manufacture, supply chains etc. Applications can be directly uploaded into an existing warehouse environment and can still be modified in terms of processes and products.
- Process modelling platform – we provide digital platform that allow to create their user customized applications in Business Process Management environment.
- Fast implementation – our experience in expertise allows us to implement software in different industries in a very short time (matter of weeks depend on internal requirements)
Novacura develops software with almost 20 years of experience across multiple industries. In close cooperation with IFS system developers we’re able to maintain complete implementing of IFS ERP system. We implement IFS systems or connect to existing ERP systems with extended functions provided by Novacura software.
Our customers can benefit through:
- Improve efficiency and accuracy of data entry
- Reducing the number of manual work
- Facilitate material traceability
- Framework of continuous improvement
- Customized and simple solution for warehouse work
- Ability to learn how to develop new solutions or adapt existing ones in-house
- A cost-effective way to integrate mobile devices with your ERP system
Novacura provide solutions that go far beyond inventory management, integrated solutions for manufacturers, global distributors and the supply chain. We implement our software across the world in different industries to provided quick respond on the dynamic changes in many industries. With our solutions, you can streamline your internal processes and progress in the fast moving industrial world.
If you are interested in implementing the presented solutions, please contact us. We will help you shape the final solution and we will take care of the whole implementation plan.