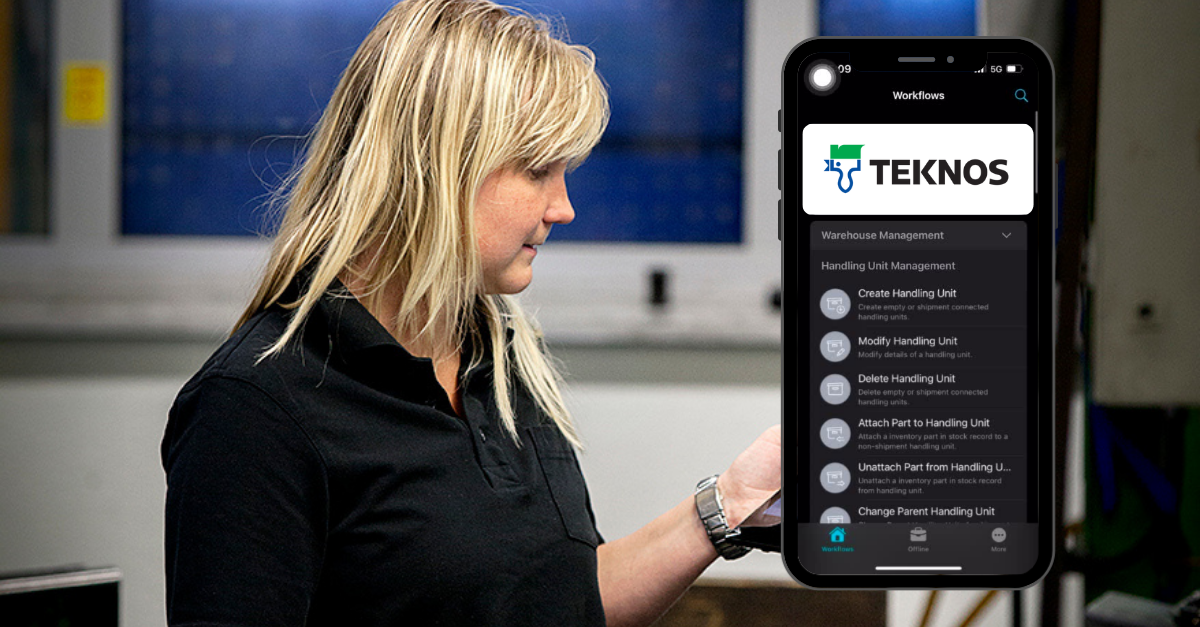
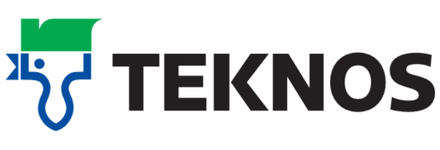
Manufacturing and logistics are closely interrelated on many levels. In a modern enterprise, attention is always on productivity and efficiency. Manufacturers have become very cognizant of the importance of measurement and obtaining data from different processes to create a holistic view of the entire business’s effectiveness.
Improvements on the shop floor are the essential, but optimizations on the logistics and distribution side are required to accelerate maximum production cycle results. Smart internal logistics and inventory management are deeply integrated into production processes and are essential for efficient total process management (TPM).
Focus on business improvement
Most manufacturing companies these days are facing some serious problems that are crossing production and inventory management operations. It is crucial for these companies to correctly understand the root causes of the existing issues to clarify the requirements for improvement.
- Warehouse operations – inefficiencies in connecting the complexity of warehouse operations (order picking, inbound and outbound, inventory management) with the production floor can result in significant financial losses due to faulty packaging management, lack of good coordination of raw materials, utilization of scrap or damage detection.
- Modification problems – difficulties with modifications that are required to meet new business needs. The old software systems installed on the shop floor need to be more flexible to extend the business capabilities that are needed to manage day-to-day operations.
Business solutions from Novacura
Problems in operations with manufacturing and warehouse management can be solved with software solutions that can extend the capabilities of ERP systems with mobile and desktop applications. The most appropriate approach is using a solution that will not make changes to the structure of the ERP system itself but will connect independently on top of it and provide the user with the ability to implement continuous modifications whenever required by the business.
Novacura Flow is an example of a flexible software solution that integrates seamlessly with ERP systems, offering mobile warehouse solutions that enhance efficiency in inventory management and logistics. This approach enables users to respond effectively to ongoing changes driven by production demands and mobile warehouse support for operational needs.
The example presented above explains how users can use Novacura Flow, with access to Novacura Flow Studio, environment for developing applications for internal operational needs in warehouses.
The warehouse solution for Teknos
TEKNOS GROUP OY. is one of the global coatings company from Finland that offers a wide range of paints and coatings for the manufacturing industry, building professionals, and consumers. The company operates in 20 countries in Europe, Asia, and the US, with more than 1500 employees globally. They have achieved outstanding results with their business approach and development in industry-driven product quality.
In early 2022, TEKNOS GROUP OY selected Novacura Flow to optimize its warehouse mobility solutions. Since then, the company has begun implementing Novacura solutions for mobile warehouse solutions, which are essential in their manufacturing processes. Novacura had the opportunity to speak with Peter Muhonen, ICT Manager, Supply Chain – and RnD Solutions, about recent developments.
Improving the warehouse operations
Before implementing Novacura Flow, Teknos already used the Novacura service to connect its IFS ERP system with its existing software solution. Although the company wanted to continuously improve its operations, it encountered the following problems:
- Problems with the functionality of the existing systems – the supporting software operations were not flexible enough to meet growing customer demand. There were problems with the application’s UI, and staff could not perform their tasks effectively.
- Warehouse operations inefficiencies – managing day-to-day operations, such as picking customer orders, putting pallets away, and counting parts, was inefficient. The lack of warehouse mobile solutions made it difficult to streamline these processes.
- Seamless integration without additional equipment – the transition to Novacura Flow allowed Teknos to enhance mobile devices for warehouse operations without purchasing new hardware. Previously used handheld scanners and printers remained fully operational.
Teknos could take advantage of the new solution without purchasing additional equipment. Previously used handheld scanners and printers could still be utilized.
By implementing Novacura solution, we have been able to get rid of legacy mobile solution limitations in functionality and usability. Now we can perform all warehouse operations with mobile devices. By completely removing the need for warehouse workers to walk back and forth to PC workstation to report operations, we have been able to increase our warehouse performance. Warehouse workers in all Teknos sites are very content with usability of the solution. The co-operation with Novacura in the implementation of the warehouse solution worked smoothly and initial scope to replace legacy solution was ready according to agreed schedule. During the project, Teknos team learned Novacura tool, and our own team has since independently extended the solution scope to cover all warehouse processes.
Warehouse solutions
Teknos has focused on improvements using warehouse standards in several different operational dimensions. The first made key improvements were in the area of warehousing, where mobile solutions played a significant role in the following operations:
- Picking customer orders in the warehouse – mobile applications were built from the beginning and equipped with functions to support the order packing process, significantly reducing the time needed to ship goods.
- Racking incoming pallets to the warehouse – goods receiving, putting away, and allocations supported by mobile apps, which reduced relocation time.
- Counting parts in the warehouse – manufacturing inventory control software was implemented to support inventory cycle counts and stock control, helping to avoid quantity discrepancies.
After implementing mobile solutions for these processes, the Novacura Flow system was extended to other warehouse operations, driving process improvement and enhancing overall efficiency.
An example of a mobile application Modify Handling Unit for warehouse management that allows the modification of a handling unit (warehouse object). This function is very useful when stock discrepancies need to be corrected and the data updated remotely in the ERP system and the correct label re-printed.
Benefits and future potential
Here are some of the benefits that Teknos has been able to accomplish to improve its operations.
- Easy learning process – personnel was able to learn the Novacura Flow low-code platform in less than three months to be ready to build their own mobile apps connected to ERP. Personnel can create business solutions totally on their own to solve current operational problems.
- Clear user interface – the interface is easy to follow for computer and mobile device users in the warehouse and is fully integrated, so all users see each other’s transactions and options.
- Flexible system configuration – operations teams can implement new transactions into the ERP system without extensive ERP modification.
- Ready-made solutions – personnel can leverage existing solutions from Novacura Marketplace and implement minor customizations when operations require.
The outcome of a project to develop a complete mobile solution for all warehouse processes, has exceeded our expectations in terms of efficiencies gained and user satisfaction. A significant part of the solution was implemented by Teknos own team and we are now fully capable to develop new solutions without support from Novacura. Having learned Novacura platform capabilities during the project, we have identified other areas where we could extend and enhance ERP solution functionalities with Novacura. We are now extending the Novacura tool to manufacturing processes by developing a mobile solution for shop floor reporting.
Summary
Teknos began working with Novacura after we supported the company in implementing IFS and integrated systems a long time ago. In 2022, the company found the Novacura Flow solution to be an effective way to streamline its operations.
Novacura supports manufacturing companies in increasing their capabilities without extensive modification of existing systems. Our solution has a proven track record of nearly 20 years in the market. We help our customers meet minimum ROI requirements. If you’re looking for an experienced partner to optimize your business process management, Novacura is the right choice. Contact us today and see how much we can do for your company.
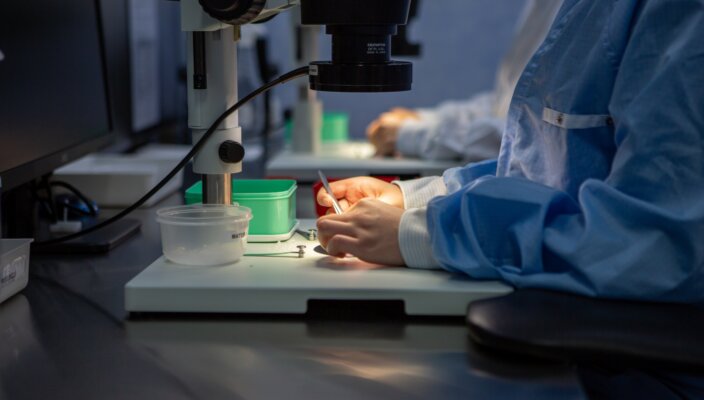
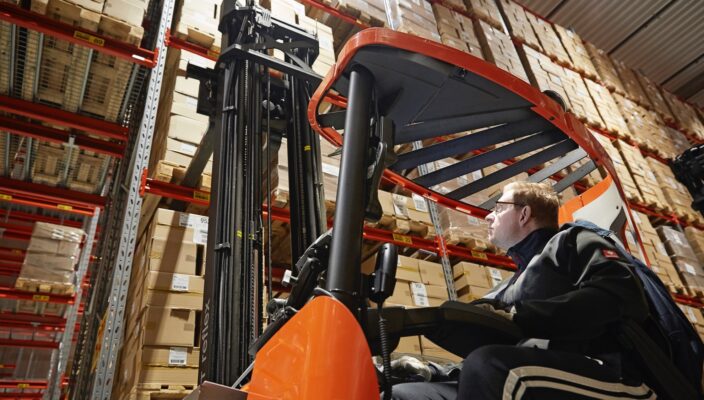
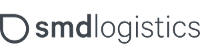
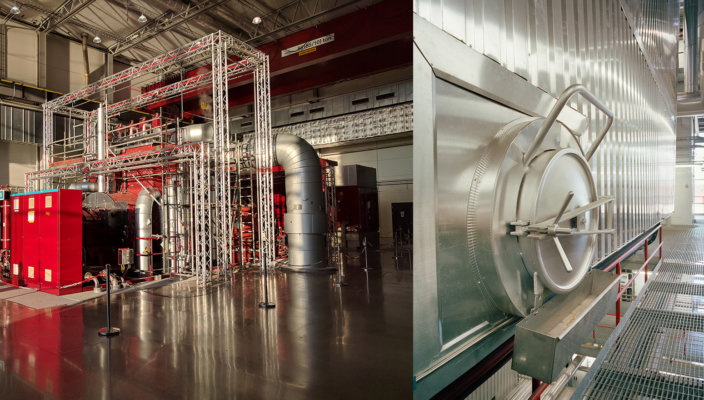
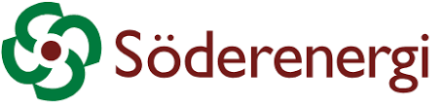
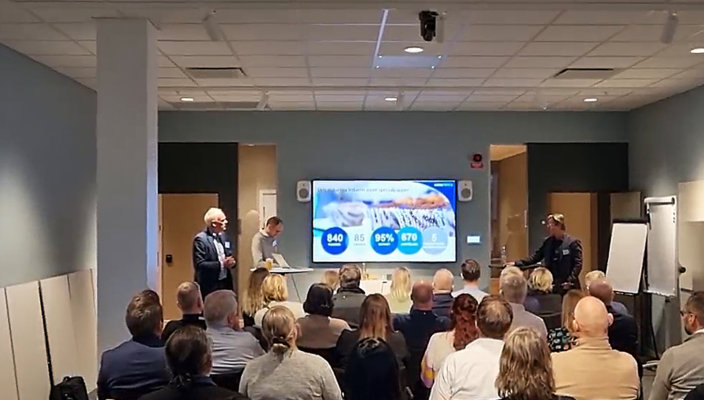
